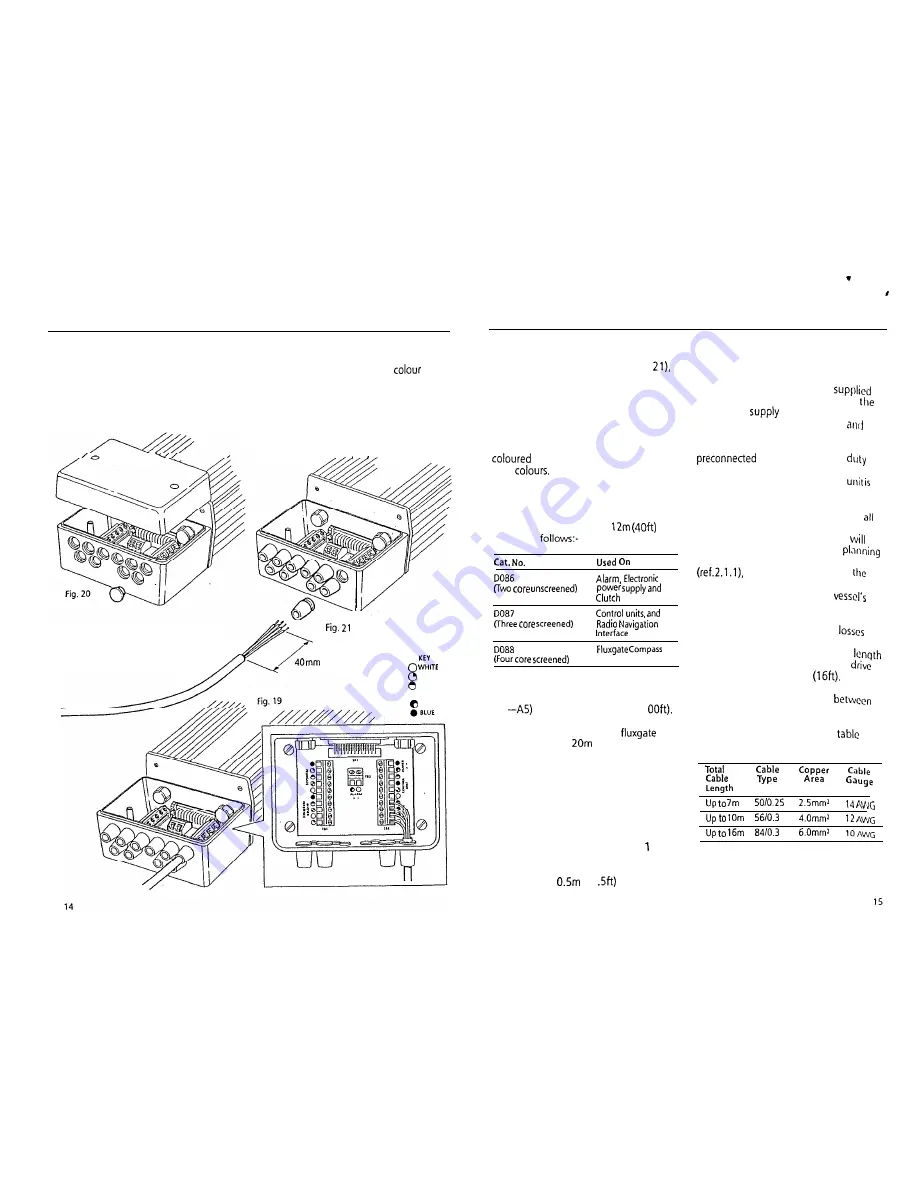
2.3 CABLING AND POWER
SUPPLIES
2.3.1 Signal Cabling
Cable interconnections between all sub
system modules are shown schematically
(in Figs 1 and 12). All peripheral units
connect to the connector unit where they
are permanently hard wired to
coded connector blocks situated on a
central printed circuit board (Fig. 19).
The end face of the connector unit is
fitted with ten blanking discs (Fig. 20).
which are easily pressed out and replaced
by the special rubber grommets supplied
with each peripheral unit fixing kit
,
YELLOW
GREEN
@ R E D
BROWN
(Fig. 2 1). After cutting the
interconnecting cable to length (Fig.
it may be passed through the inserted
rubber grommet and prepared for
connection to the relevant connector
block (Fig. 19).
Each connector block is clearly
identified on the printed circuit board and
each wire position is identified by
dots which match the individual
wire
The cable screen should be
connected to terminals identified by a
white dot.
Each peripheral unit is supplied with 6m
(20ft) of interconnecting cable. Additional
cabling can be supplied in
cut
lengths as
The total length of screened core cable
connected to the serial bus (connectors
Al
should not exceed 30m (1
Similarly, the total length of
interconnecting cable to the
should not exceed
(60ft). If it is
necessary to exceed the above maximum
length recommendations, please consult
Nautech’s Product Support Department
for specific advice. In general the length
of interconnecting cables should be kept
to an absolute minimum to reduce the
possibility of interference by other
electronic equipment.
All cables should be run at least m
(3ft) from existing cables carrying radio
frequency or pulsed signals, and should
be clamped at
(1
intervals.
2.3.2 DC Power Supplies
(Fig. 22).
Flexible connection tails fitted with
insulated spade connectors are
with the course computer to connect
main power
(Blue and Brown) and
drive unit motor connections (Red
Black).
All four flexible wire tails are
to a four-way heavy
terminal block for connection to the main
power cabling. Similarly, the drive
supplied with flexible tails for the motor
power connection (Red and Black).
Before commencing power cabling,
interconnecting terminal blocks should be
screwed into a position where they
remain dry and protected. When
the position of the course computer
it is important to reduce
overall length of heavy power cable
between the drive unit and the
central power distribution panel to a
minimum.
Excessive lengths will generate
in
the cable and will reduce system
performance. In addition, the cable
between the course computer and
unit must be less than 5m
Having sited the course computer,
measure the total cable length
the drive unit and the vessel’s central
distribution panel and select the
appropriate cable size from the
below.