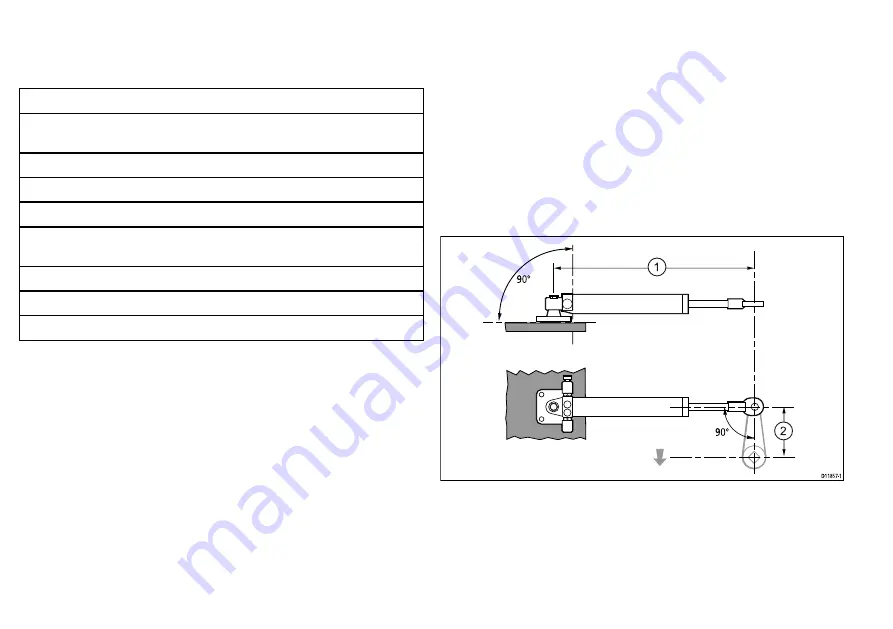
3.1 Mounting checklist
Mounting the Hydraulic Linear Drive system involves the following
tasks:
Mounting Task
1
Ensure you have read and understood the
2
Align the hydraulic ram.
3
Secure the hydraulic ram to your vessel.
4
Connect the hydraulic ram to the vessel’s steering system.
5
Perform a steering check to ensure the hydraulic ram is mounted
correctly.
6
Mount the hydraulic pump.
7
Mount the reservoir.
8
Fill the reservoir with hydraulic fluid.
3.2 Hydraulic ram alignment
When mounting the hydraulic ram ensure it is correctly aligned.
Hydraulic ram
• The hydraulic ram must be at right angles to the mounting surface.
• The hydraulic ram must be in the mid stroke position and at right
angles to the tiller arm when the rudder is at midships.
The following diagram illustrates correct alignment of the hydraulic
ram. The hydraulic ram in the top half of the diagram shows the
view from astern. The bottom half of the diagram shows the view
from above. The grey arrow indicates the aft direction.
D11857-1
90º
90º
1
2
1.
Hydraulic ram at the mid stroke position.
2.
Tiller arm radius, as follows:
•
Type 2
: 180 mm (7.1 in).
•
Type 3
: 267 mm (10.5 in).
22
Hydraulic Linear Drive Installation instructions
Summary of Contents for E12207
Page 2: ......
Page 4: ......
Page 6: ...6 Hydraulic Linear Drive Installation instructions ...
Page 20: ...20 Hydraulic Linear Drive Installation instructions ...
Page 28: ...28 Hydraulic Linear Drive Installation instructions ...
Page 40: ...40 Hydraulic Linear Drive Installation instructions ...
Page 41: ......
Page 42: ...www raymarine com ...