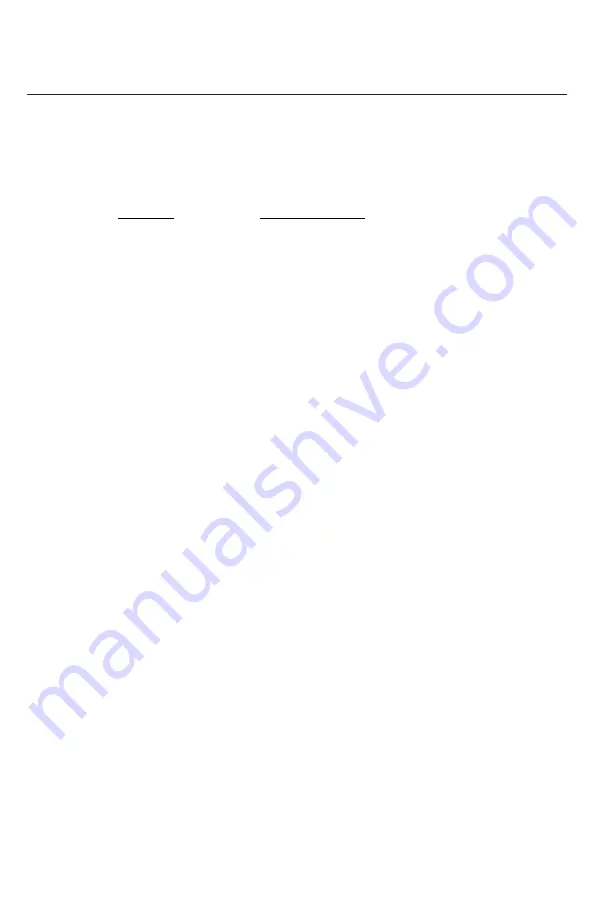
RG74T-R Operator · Service · Maintenance
800.392.2686
63
Track Drive Oil
The track drives should be filled with a Synthetic 75W-90 heavy duty gear oil. This oil should have an API service classification of GL-5
which has an extreme pressure additive. A synthetic 75W-140 or 80W-140 heavy duty GL-5 gear oil could also be used in warm climates to
extend gear life.
MWF Hydrostat Drive
The Hydrostat drive is shipped with Mobil 1 synthetic engine oil, SAE 15W-50.
Do not mix hydrostat and different lubricants!
The Differential Gearbox is shipped with 80-90W performance gear oil. Use this fluid or comparable type when refilling.
Lubricating Grease
All machines are completely serviced at the factory before shipping. The operator should check all grease fittings to familiarize with the
location and correct service schedule plan.
Use the normal shutdown procedure (See “Operating Instructions”), before lubricating the machine.
Apply grease using a standard low pressure/low volume grease gun. Do not use a pneumatic grease gun.
Lubricate with a high quality
NLGI No.2
multipurpose bearing grease having rust inhibitors, good water resistance, antioxidant additives, and a
minimum viscosity of 150 cSt at 40°C and suitable to operate continuously at 212°F / 100°C or higher.
We recommend the following bearing grease that meets this spec:
Chevron Delo EP2
……………....189 cSt @ 40°C / 17.5 cSt @ 100°C / Temperature range -40°C to 177°C (-40°F to 350°F)
Texaco Multifak EP2
………….…173 cSt @ 40°C / 15.6 cSt @ 100°C / Temperature range -34°C to 121°C (-30°F to 250°F)
Citgo Premium Lithium EP2
…..173 cSt @ 40°C / 14.9 cSt @ 100°C / Temperature range -15°C to 121°C ( 5°F to 250°F)
Shell Alvania EP2
…….………….189 cSt @ 40°C / 15.6 cSt @ 100°C / Temperature range -20°C to 100°C ( -4°F to 212°F)
Note: for
extreme cold
temperature areas a
No. 0
grade grease may be used.
Before lubricating make sure all grease fittings and the nozzle of the grease gun is clean.
Cold Weather Lubricants
Before attempting to start the engine, make sure that the oil in the engine, the transmission and the hydraulic system are fluid enough to
flow. Check the oil by removing the dipsticks. If the oil will drip from the dipstick, then the oil is fluid enough to start the engine. Do not use
oil that has been diluted with kerosene. Kerosene will evaporate in the engine. Hydraulic and track drive oil should meet all previous
specifications and have a pour point at least 7.8°C (14°F) lower than the coldest expected ambient temperature.
If the viscosity of the oil is changed for colder weather, also change the filter element. If the filter is not changed, the filter element and the filter housing
can become a solid mass. Drain all hydraulic cylinders and lines. After you change the oil, operate the equipment in order to circulate the thinner oil.
ENGINE-
•
If continuous ambient operating temperatures are below -10°C (+14°F), oil change intervals should be increased. Consult the
Engine
Operator Manual
for details.
•
When you start an engine or when you operate an engine in ambient temperatures that are below -20°C (-4°F), use base oils that can flow
in low temperatures. These oils have lubricant viscosity grade of SAE 0W or SAE 5W.
•
When you start an engine or when you operate an engine in ambient temperatures that are below
-30°C (-22°F), use a Synthetic base stock multigrade oil. The oil should have lubricant viscosity grade of 0W or 5W. Use an oil with a pour
point that is 5-10 degrees lower than the coldest ambient temperature.
Fluids Refill Capacities (Approximate)
Compartment or System
U.S. Gallons Imperial Gallons
Liters
Fuel Tank
Engine Crankcase w/Filter
Total Engine Coolant including Cooler
Hydraulic Reservoir
Lubrication & Fluid Specifications
Summary of Contents for RG74T-R
Page 23: ...RG74T R Operator Service Maintenance 800 392 2686 23 Safety ...
Page 24: ...RG74T R Operator Service Maintenance 24 Operation 3 5 6 8 1 4 11 2 7 4 9 10 12 13 ...
Page 35: ...RG74T R Operator Service Maintenance 800 392 2686 35 Operation ...
Page 55: ...RG74T R Operator Service Maintenance 800 392 2686 55 Main Wiring Harness 35170 G ...
Page 58: ...RG74T R Operator Service Maintenance 58 Hydraulic Schematic 805039 ...