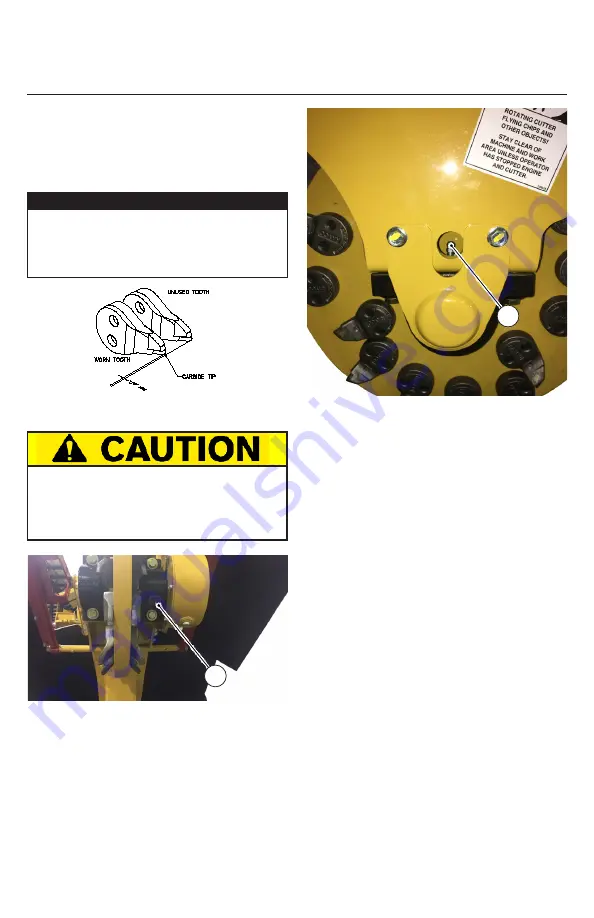
RG74T-R Operator · Service · Maintenance
800.392.2686
47
2. Discard any tooth that has lost more than 1/8” of original
bite, whether lost through usage or grinding.
3. Grind off a minimal amount from the end, just enough
to restore the original taper and radius on the end. The
end of the cemented carbide tip and the end of the steel
shank should be flush after grinding.
Cutter Wheel Bearings
Lubricate
Lubricate the cutter wheel bearings zerk(1) fitting DAILY. Fill
with high-temperature
(NLGI 2)
grease until you can visually
see the old grease purge itself out all the way around the seal
diameter and new grease beginning to purge out.
This will ensure that the dirt and debris that gets collected
inside the seal area is flushed away from the internal bearings
thus providing longevity to the bearing and races.
Engine Leaks - Check
Check for leaks as described in the “After First 50 Hours”
interval of the Cummins Engine Operation Manual.Engine
Mounts - Check
Check and tighten if necessary all engine mounts.
Maintenance
NOTICE
Sharpening cemented carbide cutting teeth requires
a special process. Have your teeth sharpened only
by a qualified machinist for obtaining a proper edge
and to avoid injury.
1
INSERT GREASE SLOWLY AND CAREFULLY TO
PREVENT DAMAGE TO THE BEARING SEALS. USE
EXTRA CAUTION WHEN USING A HIGH PRESSURE
OR HIGH VOLUME GREASE GUN.
1
Summary of Contents for RG74T-R
Page 23: ...RG74T R Operator Service Maintenance 800 392 2686 23 Safety ...
Page 24: ...RG74T R Operator Service Maintenance 24 Operation 3 5 6 8 1 4 11 2 7 4 9 10 12 13 ...
Page 35: ...RG74T R Operator Service Maintenance 800 392 2686 35 Operation ...
Page 55: ...RG74T R Operator Service Maintenance 800 392 2686 55 Main Wiring Harness 35170 G ...
Page 58: ...RG74T R Operator Service Maintenance 58 Hydraulic Schematic 805039 ...