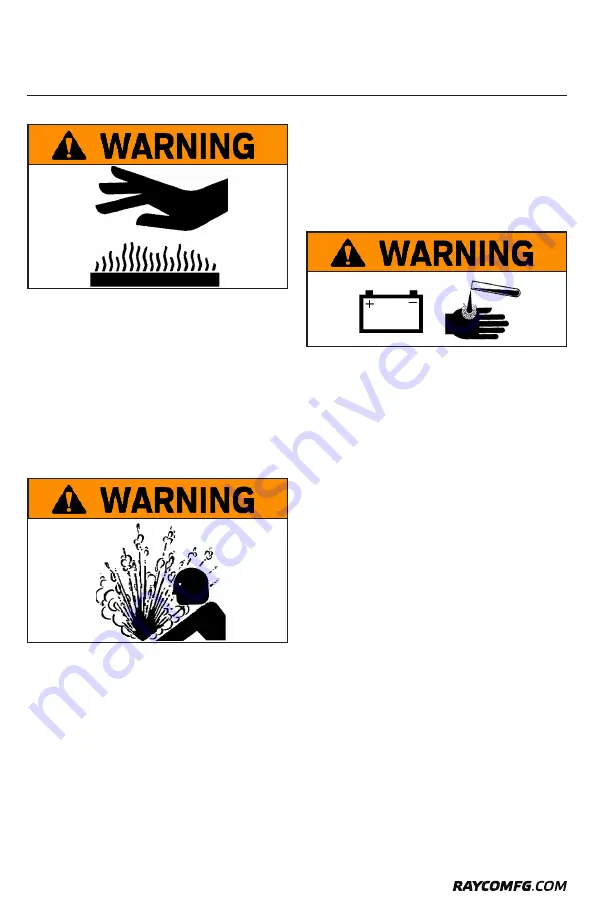
RG165T-R Operator · Service · Maintenance
14
Safety
Burn Prevention
Do not touch any part of an operating engine. Allow the
engine, radiator, exhaust and hydraulic reservoir to cool before
any maintenance is performed. Relieve all pressure in the
air system, oil system, lubrication system, fuel system, and/
or in the cooling system before any lines, fittings or related
items are disconnected.
In addition, avoid contact with other related hot engine parts
such as exhaust manifolds, turbochargers and mufflers.
External exhaust parts become very hot during operation.
Paper, cloth, and wooden materials could ignite if they come
in contact with these parts.
Coolant
When the engine is at operating temperature, the engine
coolant is hot. The coolant is also under pressure. The
radiator and all lines to the heaters or to the engine contain
hot coolant.
Any contact with hot coolant or with steam can cause severe
burns. Allow cooling system components to cool before the
cooling system is drained.
Check the coolant level only after the engine has been stopped.
Ensure that the filler cap is cool before removing the filler
cap. The filler cap must be cool enough to touch with a bare
hand. Remove the filler cap slowly in order to relieve pressure.
Cooling system conditioner contains alkali. Alkali can cause
personal injury. Do not allow alkali to contact the skin, the
eyes or the mouth.
Oils
Hot oil and hot components can cause personal injury. Do
not allow hot oil to contact the skin. Also, do not allow hot
components to contact the skin.
Remove the hydraulic tank filler cap only after the engine
has been stopped. The filler cap must be cool enough to
touch with a bare hand. Follow the standard procedure in
this manual in order to remove the hydraulic tank filler cap.
Batteries
Electrolyte is an acid. Electrolyte can cause personal injury.
Do not allow electrolyte to contact the skin or the eyes.
Always wear protective glasses for servicing batteries. Wash
hands after touching the batteries and connectors. Use of
gloves is recommended.
Fire & Explosion Prevention
All fuels, most lubricants, and some coolant mixtures are
flammable.
Flammable fluids that are leaking or spilled onto hot surfaces
or onto electrical components can cause a fire. Fire may
cause personal injury and property damage.
Remove all flammable materials such as fuel, oil, and debris
from the machine. Do not allow any flammable materials
to accumulate on the machine. Serious personal injury can
occur when fuel or oil is spilled on yourself or your clothes,
which can ignite.
Store fuels and lubricants in properly marked containers away
from unauthorized persons. Store oily rags and any flammable
materials in protective containers. Do not smoke in areas
that are used for storing flammable materials.
Do not operate the machine near any flame.
Extinguish all cigarettes, cigars, pipes and other sources
of ignition.
Exhaust shields (if equipped) protect hot exhaust components
from oil spray or fuel spray in case of a break in a line, in a
hose, or in a seal. Exhaust shields must be installed correctly.
Do not weld on lines or on tanks that contain flammable fluids.
Do not flame cut lines or tanks that contain flammable fluid.
Clean any such lines or tanks thoroughly with a nonflammable
solvent prior to welding or flame cutting.
Check all electrical wires daily. Repair any wires that are
loose or frayed before you operate the machine. Clean all
electrical connections and tighten all electrical connections.
Dust that is generated from repairing nonmetallic hoods or
non metallic fenders can be flammable and/or explosive.
Repair such components in a well ventilated area away from
open flames or sparks.
Summary of Contents for RG165T-R
Page 23: ...RG165T R Operator Service Maintenance 800 392 2686 23 Safety ...
Page 24: ...RG165T R Operator Service Maintenance 24 Operation 11 7 1 3 2 5 6 8 4 9 10 12 13 14 15 16 ...
Page 47: ...RG165T R Operator Service Maintenance 800 392 2686 47 Maintenance ...
Page 62: ...RG165T R Operator Service Maintenance 62 Hydraulic Schematic 806797 TOP ...
Page 63: ...RG165T R Operator Service Maintenance 800 392 2686 63 Hydraulic Schematic 806797 TOP BOTTOM ...
Page 69: ...RG165T R Operator Service Maintenance 800 392 2686 69 ...