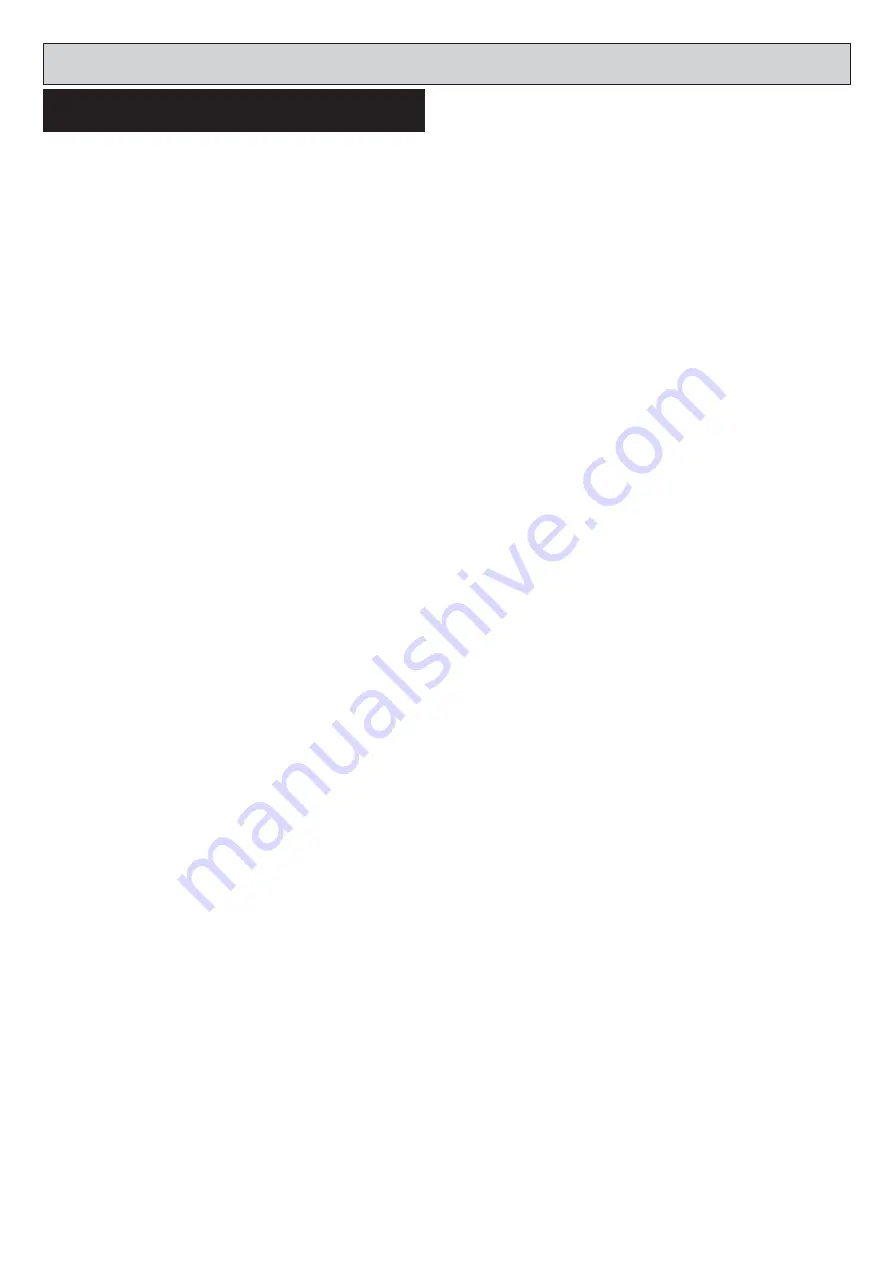
BURNER WILL NOT START
1.
Check that external wiring is correct.
2.
Check for 230V supply on terminal 1 at control box base, this will also determine if the thermostats are calling for
heat.
Check that incoming Neutral conductor is correctly wired onto terminal 2.
3.
Press reset button to ensure that the control box has not gone to lockout.
4.
Check air pressure switch is in provide air condition and fan is running.
5.
If burner still refuses to start, change control box.
BURNER FAN RUNS WITH CONTINUOUS PRE-PURGE
1.
Check wiring to air pressure switch across terminal 8 & 11 at control box base.
2.
Check air pressure switch.
3.
Check fan inlet ducts and fan for blockages.
4.
Check plastic air tubes are correctly connected.
BURNER STARTS, FLAME NOT ESTABLISHED, CONTROL BOX GOES TO LOCKOUT, AFTER END OF SAFETY
1.
Check gas supply to valves is on.
2.
Check ignition is present after end of pre-purge period.
3.
Check start gas valve is energised and is opening during safety time.
4.
If necessary change control box.
BURNER STARTS FLAME ESTABLISHED, CONTROL BOX GOES TO LOCKOUT
1.
Check polarity of wiring for Live and Neutral to control box base. live to terminal 1. Neutral onto terminal 2 at control
box base.
2.
Check flame detection probe is correctly positioned. Ensure that the probe insulation is sound, free from cracks or
moisture.
Check that the probe is not in contact with other metallic parts of the burner.
3.
Check the burner is effectively earthed and boned to the incoming earth wire from the mains supply.
4.
Check for interference to the flame signal from the ignition spark. This can be determined with a d.c. micro-ammeter
(µA). Connect the meter between terminal 12 and the incoming wiring to the flame probe. Correct polarity of the
meter connections must be correctly observed, with the positive side of the meter connected onto terminal 12 at
the control box wiring base. If flame is established and the meter tends to move in a reverse direction this can be
an indication that the ignition is causing interference to the flame signal. It may also be an indication that there is
insufficient earth contact with the flame. A correct reading should be approximately 15 - 20 µA.
5.
Change control box if necessary.
28
TROUBLESHOOTING-BURNER
Fault Finding
Summary of Contents for Heatranger 480GB
Page 15: ...Replacement of parts Electrical FIG 20 DESN 511140 14...
Page 23: ...Electrical Controls 22 CONTROL CIRCUIT BOILER FIG 30...
Page 24: ...Electrical Controls 23 CONTROL CIRCUIT COOKER FIG 31...
Page 25: ...Electrical Controls 24 WIRING DIAGRAM BURNER ONLY FIG 32...
Page 26: ...25 WIRING DIAGRAM APPLIANCE Electrical Controls FIG 33...
Page 30: ...29...
Page 31: ...30...
Page 32: ......
Page 33: ......