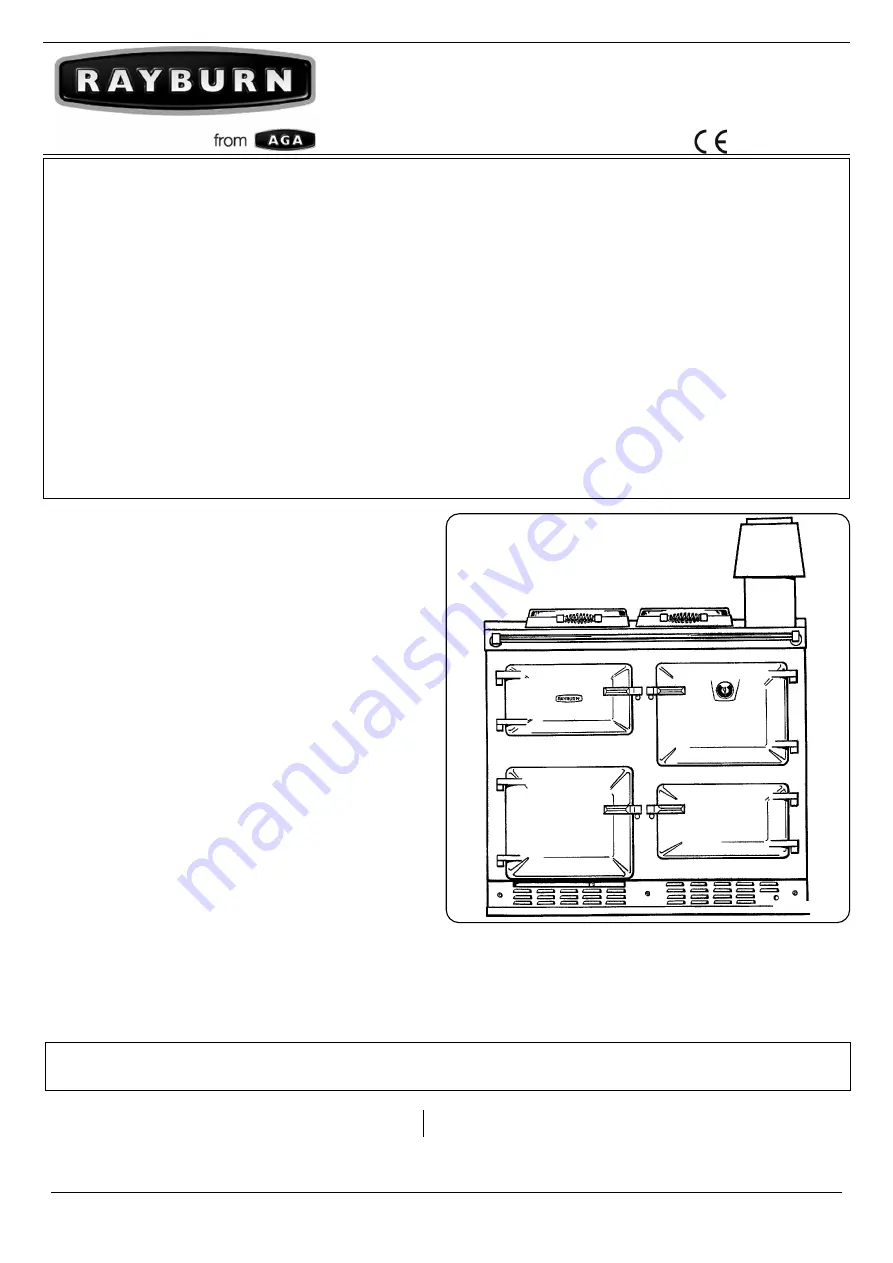
1
Heatranger 480AG (CF)/480AL (CF)
Installation and Servicing Instructions
09/22 EINS 512112
LPRT 512180
Consumer Protection
As responsible manufacturers we take care to make sure
that our products are designed and constructed to meet the
required safety standards when properly installed and used.
IMPORTANT NOTICE: PLEASE READ THE ACCOMPANYING
WARRANTY.
Any alteration that is not approved by AGA,
could invalidate the approval of the appliance, the warranty
and could also infringe the current issue of the statutory
requirements.
All local regulations including those referring to national
and European standards need to be complied with when
installing this appliance.
Control of Substances - Health & Safety Important
This appliance may contain of the materials that are
indicated below. It is the Users/Installers responsibility to
ensure that the necessary personal protective clothing
is worn when handling, where applicable, the pertinent
parts that contain any of the listed materials that could be
interpreted as being injurious to health and safety, see below
for information.
Firebricks, Fuel beds, Artificial Fuels
- when handling use
disposable gloves.
Fire Cement
- when handling use disposable gloves.
Glues and Sealants
- exercise caution - if these are still in
liquid form use face mask and disposable gloves.
Glass Yarn, Mineral Wool, Insulation Pads, Ceramic Fibre,
Kerosene Oil
- may be harmful if inhaled, may be irritating
to skin, eyes, nose and throat. When handling avoid inhaling
and contact with skin or eyes. Use disposable gloves,
face-masks and eye protection. After handling wash hands
and other exposed parts. When disposing of the product,
reduce dust with water spray, ensure that parts are securely
wrapped.
Introduction
THIS APPLIANCE MUST BE INSTALLED IN ACCORDANCE
WITH THE RULES IN FORCE AND USED ONLY IN A
SUFFICIENT VENTILATION SPACE.
USE ONLY ON FULLY PUMPED SYSTEMS
This Rayburn Gas combination appliance is combined
cooker and hot water boiler providing central heating and
domestic hot water in addition to special cooking facilities. It
is available in open flue form, operating on natural draught,
the boiler being designed for use in fully pumped, open or
sealed systems. Two separate independent controlled gas
burners provide heat. One burner for central heating boiler
section, providing heating and hot water, whilst the other
burner provides heat to the cooker.
REMEMBER, when replacing a part on this appliance,
use only spare parts that we require. Do not use
reconditioned or copy parts that have not been clearly
authorised by AGA.
Regulations
In the interests of safety all gas appliances should be
installed by competent persons, in accordance with the
regulations in force.
FOR USE IN GB & IE
DESN 512129
PLEASE READ THESE INSTRUCTIONS BEFORE INSTALLING THE APPLIANCE