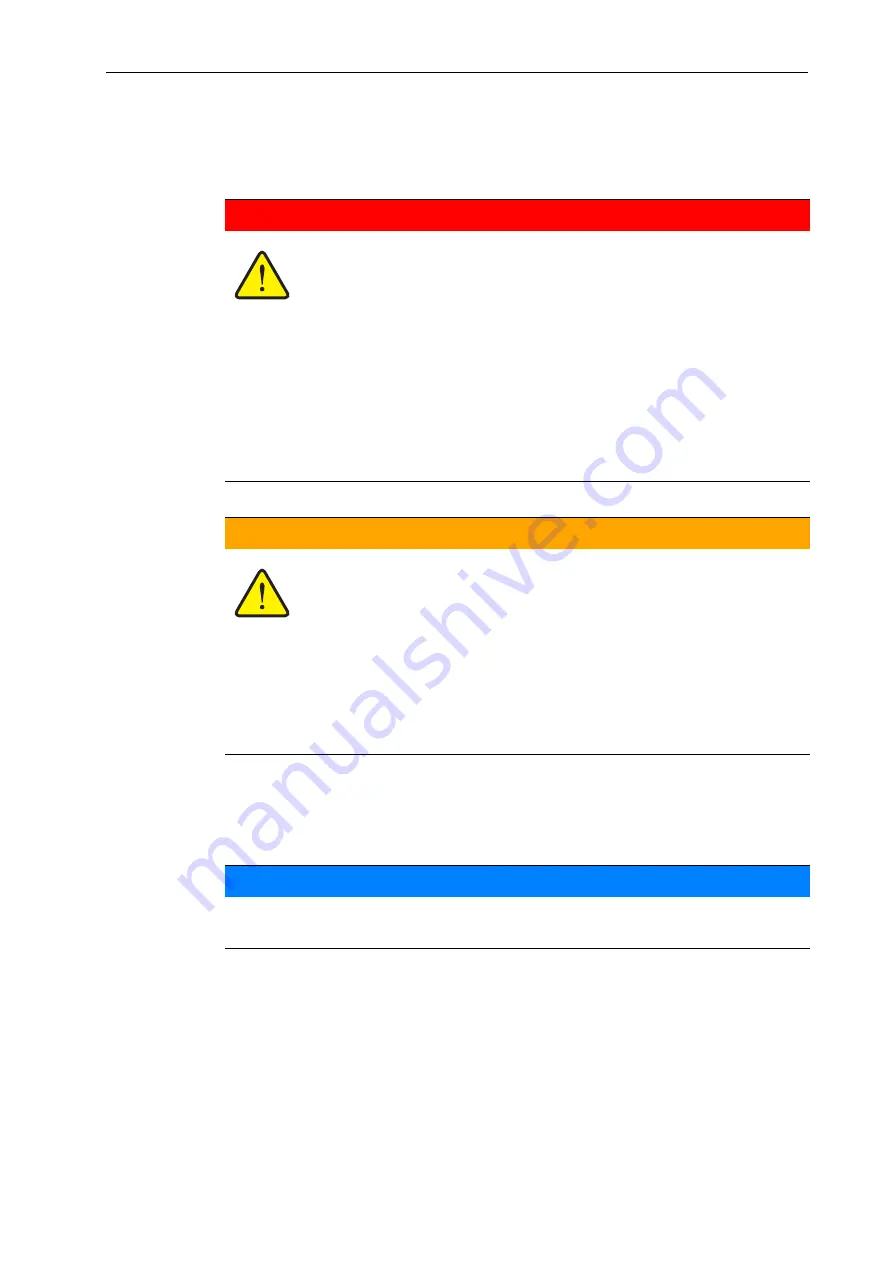
Commissioning
53
7
7.6
Presetting the mounting height
7.6.1
Safety
General instructions before setting the mounting height
We recommend that you choose the highest coupling point on the tractor to
connect the upper link, particularly for high lifting heights.
The lower coupling points on the machine which are meant for the lower links
of the tractor should be used
only in exceptional circumstances
in late fer-
tilising.
n
DANGER
Risk of being crushed under the falling-down machine
If the upper link halves are accidentally rotated totally apart from
each other, it may happen that the upper link cannot compensate
for the tractive forces of the machine. This may result in the
machine abruptly tilting over backwards or falling down.
This can lead to severe personal injury. Machines can be damaged.
When extending the upper link, always observe the maxi-
mum admissible length specified by the tractor or upper link
manufacturer.
Ensure that nobody is present in the hazard zone of the
machine.
n
WARNING
Risk of injury from rotating spreading discs!
The distribution unit (spreading disc, vanes) may catch and pull-in
body parts or objects. Contact with the distribution unit may injure,
crush or cut off body parts.
Maximum admissible mounting heights at front (V) and rear
(H) are to be complied with at all times.
Ensure that nobody is present in the hazard zone of the
machine.
Never remove deflectors mounted on the hopper.
NOTICE
For normal fertilisation and late fertilising,
always
use the
upper coupling
points
of the machine.
Summary of Contents for AXIS-M 30.2
Page 8: ...Inhaltsverzeichnis VI...
Page 10: ...Intended use 1 2...
Page 42: ...Technical data 4 34...
Page 46: ...Axle load calculation 5 38...
Page 48: ...Transportation without tractor 6 40...
Page 110: ...Spreading operation 8 102...
Page 144: ...Index D...
Page 146: ......
Page 147: ......
Page 148: ......