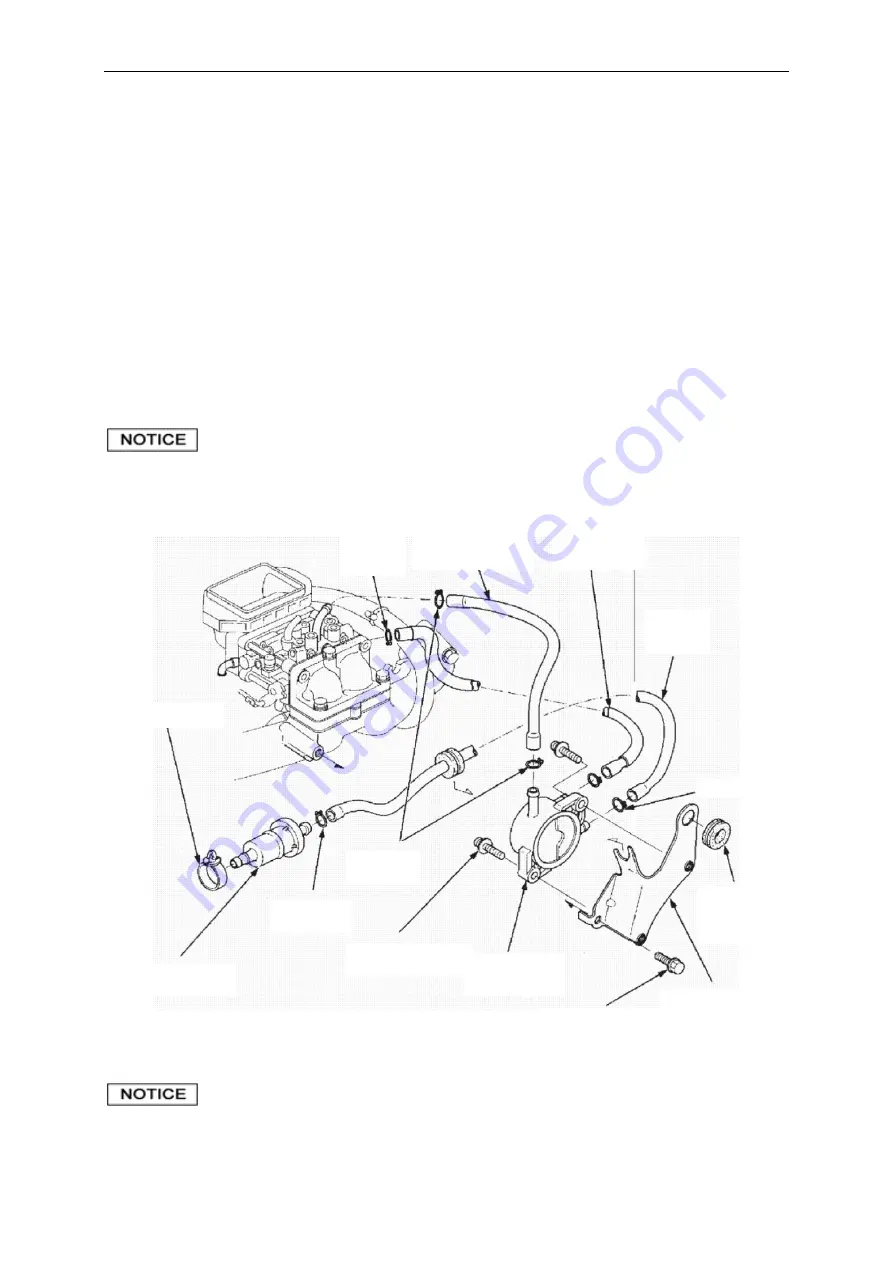
Part IV Wiring Diagram
21
you can go to authorized dealer of the Company to change the main metering hole and adjust the carburetor.
Otherwise, the gasoline engine shall be used by reducing power.
Even if being equipped with proper carburetor, every 300 m's rise in ASL will reduce the power of the
gasoline engine by about 3.5%. This reduction will be greater if it is not equipped with proper carburetor.
If a carburetor applicable to high ASL application is equipped to a gasoline engine for low ASL
application, too thin mixed gas will cause the power reduction of gasoline engine, overheating and even
cause more serious damage.
The gasoline is fed into the carburetor from the fuel tank and fuel filter. The fuel filter can filter out
impurities mixed in the gasoline and oxides in the fuel tank. If the quality is defective, some impurities will
enter the carburetor through the fuel filter. In addition, gasoline contains components capable of forming
gelatinous substance, which will condense gelatinous substance after a long time of deposition to attach to
components of the carburetor (such as main metering hole), oil way and the surface of float chamber. Air is
fed into the carburetor by way of air filter. Based on the consideration that intake resistance shall not be too
great and other factors, filter device shall not be too dense, hence some tiny impurities in air will still enter
the carburetor via the air filter.
1)
Gasoline pump
To remove the gasoline pump and the carburetor, please drain the gasoline in the oil pipe
thoroughly first.
a)
Remove the air filter and the fan guard decoration sheet (refer to maintaining the air filter)
b)
Carry out disassembly according to the above figure from right to left.
The oil pipe is vulnerable. So, please pay attention to inspecting it during disassembly and
installation, and replace it immediately if it is damaged.
2)
Carburetor
Pipe
clamp
Oil pipe (long)
Pipe clamp
Oil pipe
(short)
Negative
pressure pipe
Pipe clamp
Pipe clamp
Pipe clamp
Fuel filter
Bolt M6 × 16
Bolt M6 × 16
Gasoline pump
components
Gasoline pump
bracket
Rubber sleeve for
gasoline pump
bracket