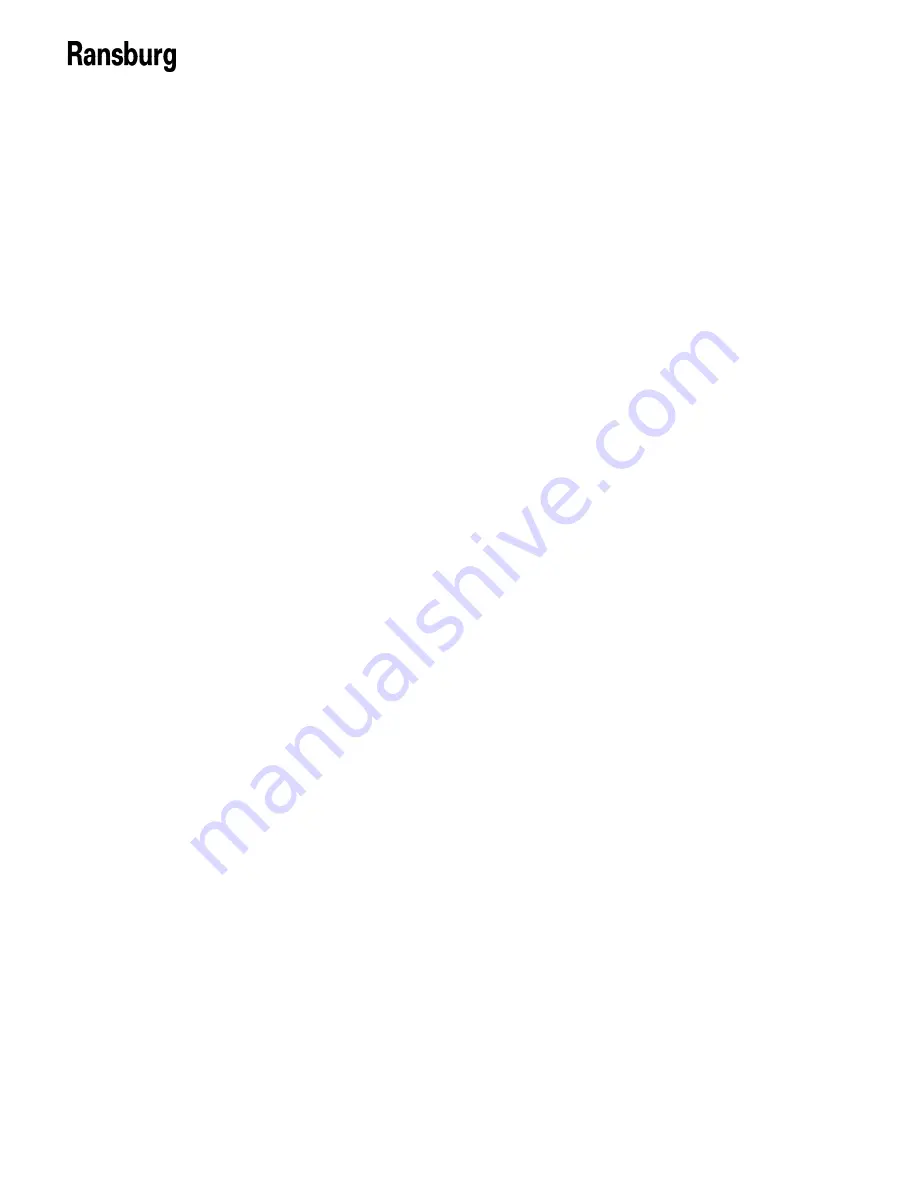
Technical Support Representative will direct you to the appropriate telephone number for or-
dering Spare Parts.
Manufacturing
1910 North Wayne Street
Angola, Indiana 46703-9100
Telephone: 260-665-8800
Fax: 260-665-8516
Technical Service — Assistance
320 Philips Ave.
Toledo, Ohio 43612-1493
Telephone (toll free): 800-233-3366
Fax: 419-470-2233
www.ransburg.com
Form No. LN-9415-01
© 2015 Finishing Brands, Americas..
Litho in U.S.A.
Models and specifications subject to change without notice.
01/15