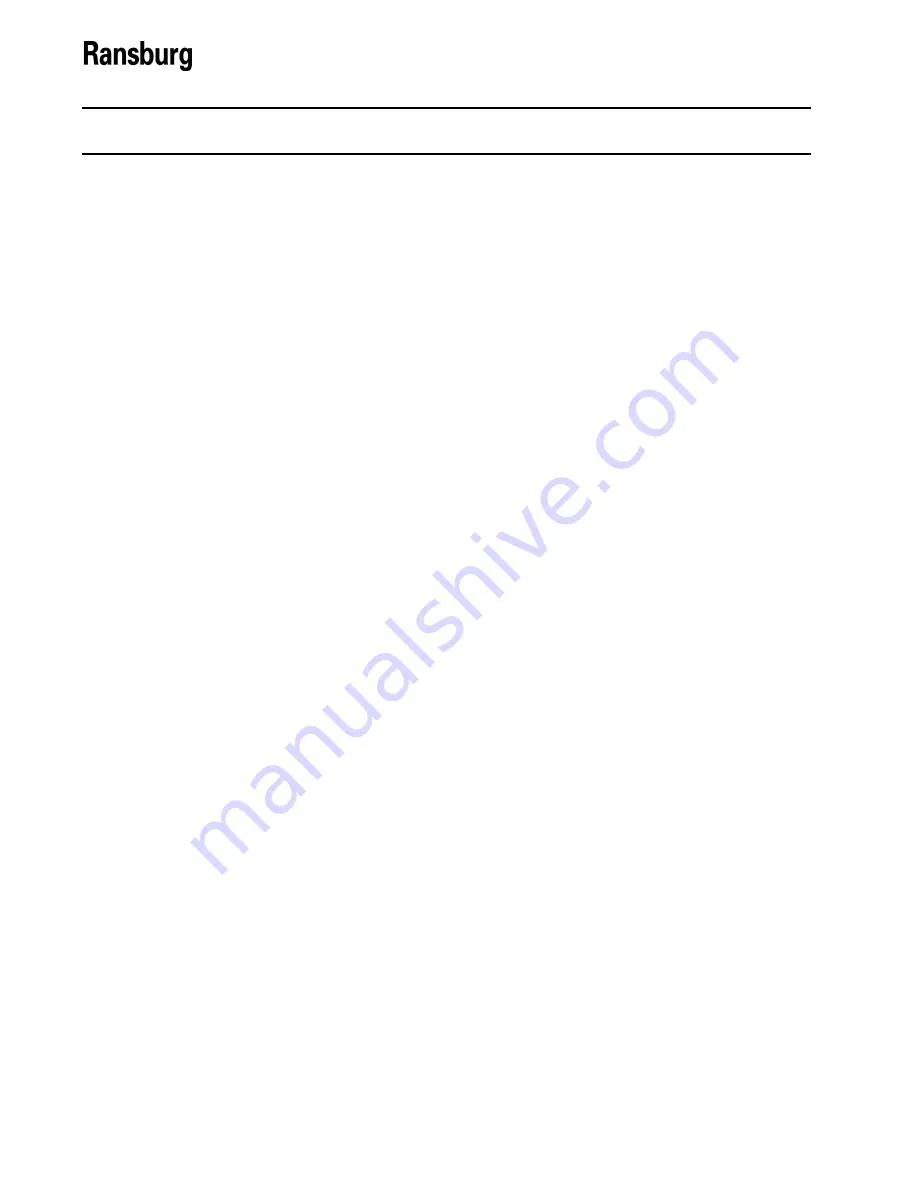
Positive Displacement Pump - Operation
LN-9415-01
10
OPERATION
If the inlet pressure of the pump is too low,
the pump will be starved for material and
will cavitate, resulting in lower flows than
expected. Additionally, if the outbound
pressure is significantly higher than the inlet
pressure, the gears will slip by the material,
also causing the flow to be less than ex-
pected.
On the other hand, if the inlet pressure is
too high (especially at low viscosities),
material can “blow by” the gears in the
meter and the resultant flow will be higher
than expected.
Positive displacement gear pumps are most
accurate when the pressure across the
pump (known as differential pressure) is
minimized. That is, if the inlet pressure can
be maintained at a pressure that is very
close to the outlet pressure, the most
accuracy will be realized. The RCS and
RCS-2 Systems have the ability to control
the inlet pressure automatically based on
the value of the outlet pressure. This,
however, is an optional feature. If you are
interested in enabling this feature on your
RCS or RCS-2 System, contact your
Ransburg representative.
PRINCIPLE OF OPERATION
The external gear pump is a positive dis-
placement (PD) type of pump generally
used for the transfer and metering of liq-
uids. The gear pump is a precision machine
with extremely tight fits and tolerances, and
is capable of working under high differential
pressures.
Typically there is a drive gear driven by a
motor that rotates an idler gear in the
opposite direction. When the gears rotate,
the liquid, which is trapped in the gear teeth
spaces between the housing bore and the
outside of the gears, is transferred from the
inlet side of the pump to the outlet side. The
pumped liquid moves around the outside of
the gears and not between the gears. The
rotating gears continue to deliver a fresh
supply of liquid from the suction (inlet) side
of the pump to the discharge (outlet) side of
the pump, with virtually no pulsations. The
meshing of the gears on the discharge side
of the pump forces the liquid out of the
pump and into the discharge port.
Flow rate through the pump is controlled
simply by varying the RPM of the motor
driving the pump. On RCS and RCS-2
Systems, it is recommended that the RPM
of the pump not be allowed to exceed 150
RPM’s.
The accuracy of the gear pump is directly
affected by both the viscosity of the material
being pumped and the differential pressure
across the pump.
If the material is too thin (e.g. viscosities
less than 30 centipoise), it will not be
properly metered by the pump and inaccu-
rate flow rates will result.