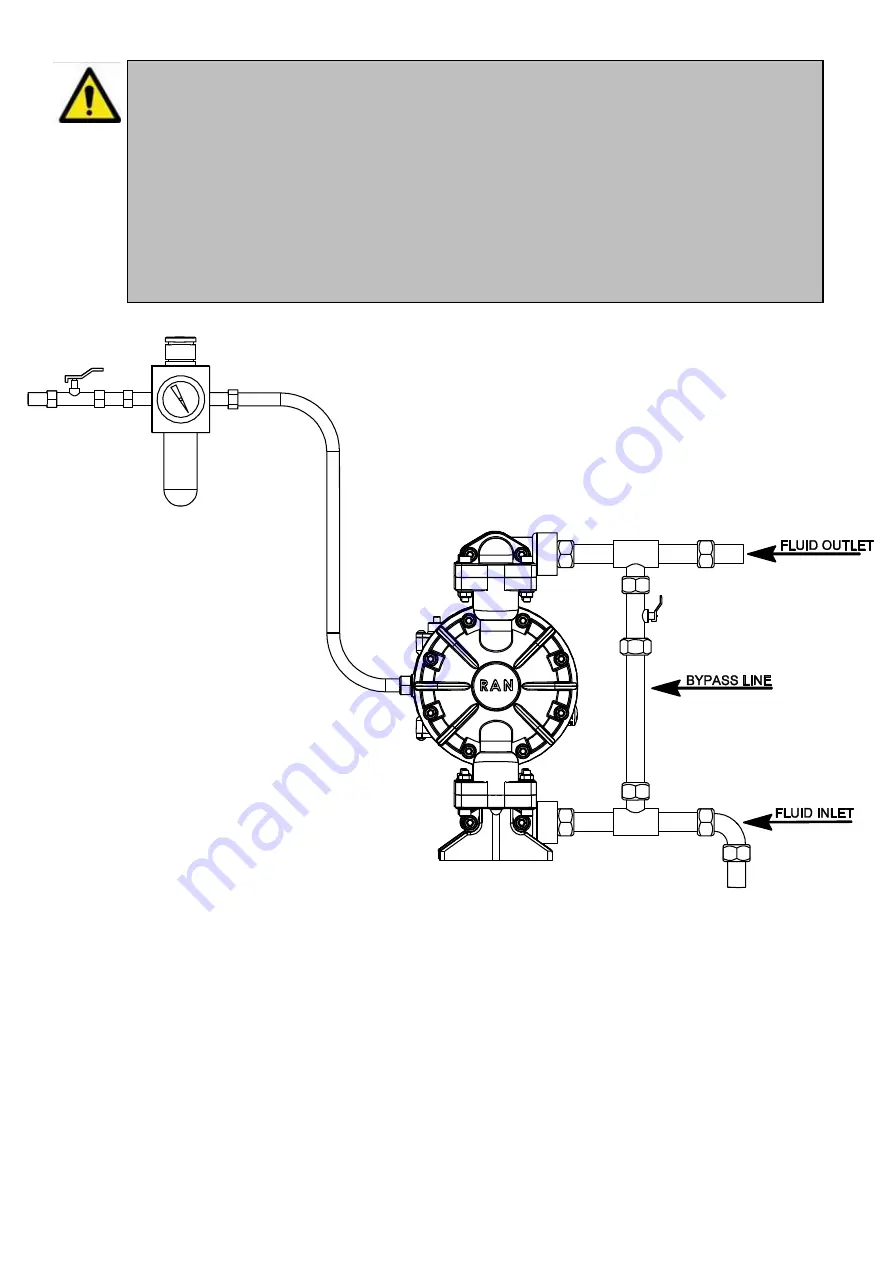
11
Figure 8c - Bypass line installation
Caution. It is advisable to install a pressure relief system (bypass line)to
relieve high levels of pressure that may occur if the pump is pressurised for a
long period when not operating.
On some uncontrolled systems the back pressure generated from a closed
outlet hose can cause the pump to stop or even reverse operation. In this case
a pressure relief system (bypass line) MUST be installed.
When using long pipelines, that may be pumping cold fluid with hose placed
in a warmer area such as underground tank or buried underground, in
sunshine or near other heat sources the hose may be affected by thermal
expansion of the liquid, causing an increase in pressure. Hose rupture may
result. In this case, a pressure relief system (bypass line) must be installed.