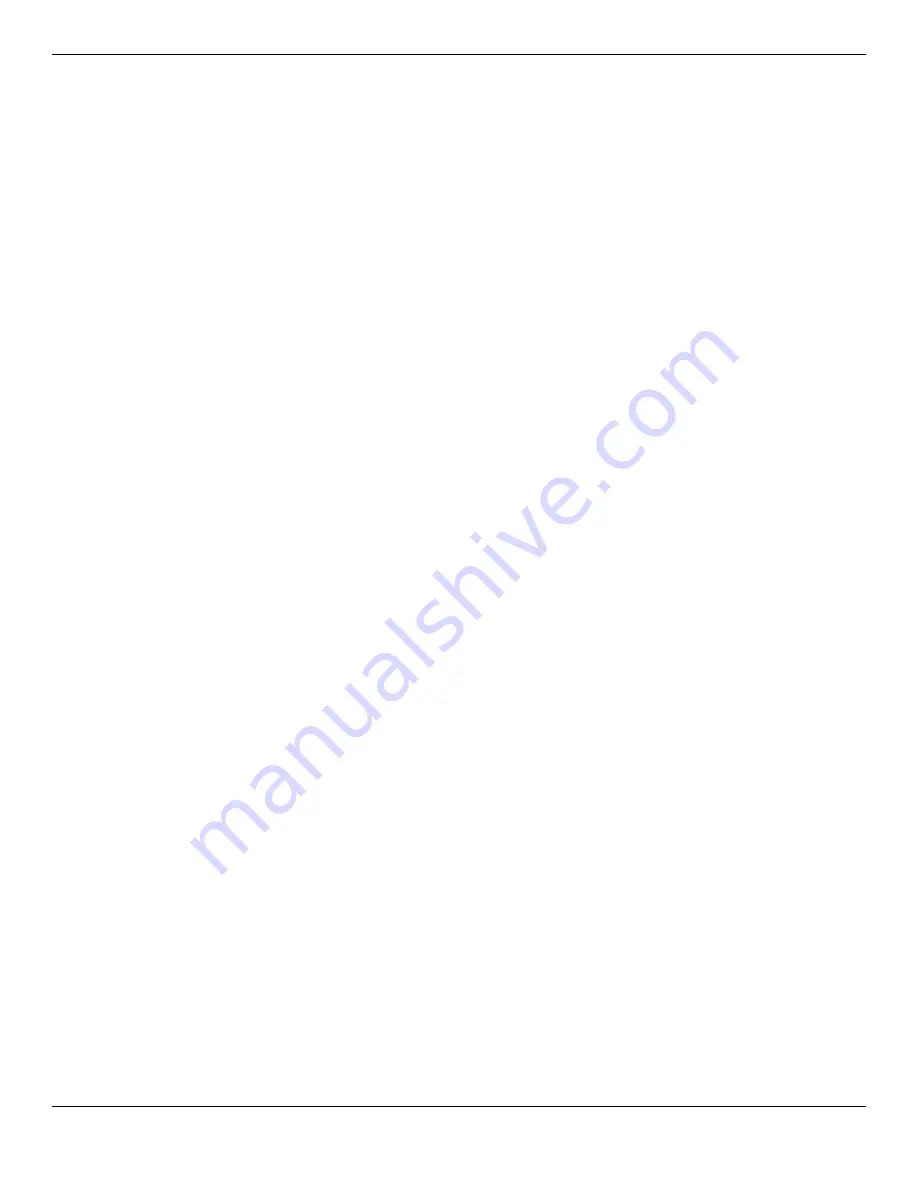
R980 Series of Tire Changers
25
P/N 5900158 — Rev. F - March 2022
17.
Locate the Tubing piece
coming out of the Assist Tower
and route it down and through the
single Vertical Steel Tube near the top of the Main Tower.
18.
Push the end of the Tubing piece coming out of the Assist Tower onto the Straight Connector end
of the New Air Hose.
19.
Apply power and air to the Tire Changer.
20.
Test the tools on the Assist Tower to verify they are working correctly.
If you run into issues with your Assist Tower you cannot fix, visit
, or call
BendPak Ranger
at
(805) 933-9970
.
Test the Tire Changer
Make sure the following items have been done
before
putting the Tire Changer into normal operation:
•
Check for pneumatic (air) pressure
. The Tire Changer requires pneumatic energy to
perform certain functions.
To see if the Tire Changer has air pressure, take the Air Chuck and lightly step on and hold down
the Inflation Foot Pedal. If air comes out, the Air Source is connected and working.
•
Test the power source
. Other Tire Changer functions require electric power. Step on and hold
down the Turntable Foot Pedal to check for electric power. If the Turntable turns, you have power.
•
Make sure there is Tire lubricant available
. Your shop probably has a brand of Lube that
it prefers. Make sure some is in the Lube Bucket on the Tire Changer. Always use Lube; it makes
changing Tires easier and helps prevent damage to the Tire and the Wheel.
•
Test the Tool Arms
. Manually move each Tool Arm separately from side to side. Use the Assist
Tower Controls to raise and lower the Tool Arms (they move up and down together). If the Tool
Arms can do these things, they are working correctly.
•
Change some non-customer Tires
. To get used to the Tire Changer, BendPak Ranger
recommends have all potential Operators change some
non-customer Tires
before putting the
Tire Changer into normal operation.
Final Checklist before Operation
Do the following things
before
putting your Tire Changer into normal operation:
•
Review the Installation Checklist to make sure all steps have been performed.
•
Verify the Tire Changer is getting electric and pneumatic power.
•
Check to see that all Anchor Bolts are in position and tightened, if you installed them.
•
Make sure the Tire Changer has been used to change some non-customer Tires.
•
Leave the Manual with the owner/operator.
Summary of Contents for R980AT
Page 60: ...R980 Series of Tire Changers 60 P N 5900158 Rev F March 2022 Labels ...
Page 61: ...R980 Series of Tire Changers 61 P N 5900158 Rev F March 2022 ...
Page 62: ...R980 Series of Tire Changers 62 P N 5900158 Rev F March 2022 ...
Page 83: ...R980 Series of Tire Changers 83 P N 5900158 Rev F March 2022 Assist Tower Optional ...
Page 87: ...R980 Series of Tire Changers 87 P N 5900158 Rev F March 2022 Maintenance Log ...