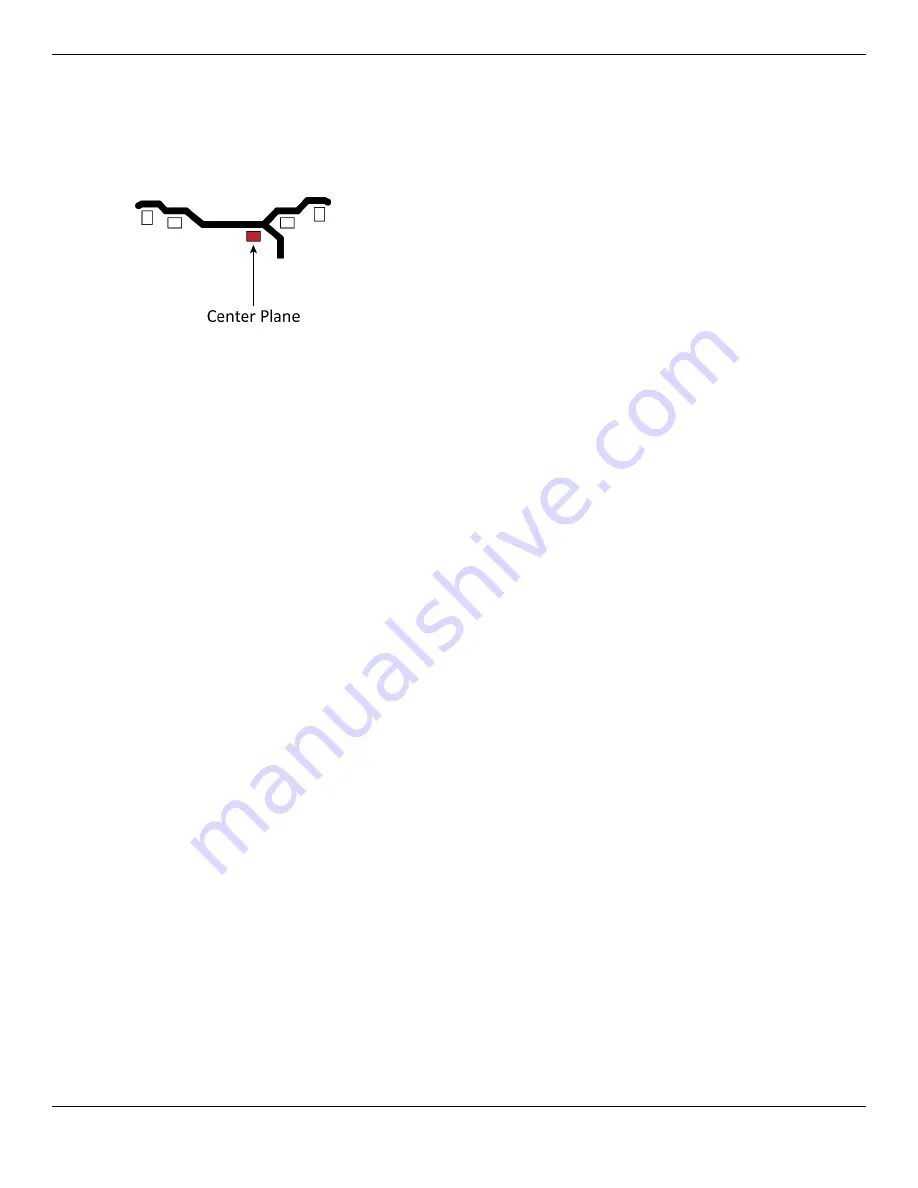
LS43B Laser-Spot™ Wheel Balancer
35
P/N 5900086 — Rev. A1 — 12/212018
Static Balancing
Static Balancing is for older Wheels under 4 inches wide and motorcycle Wheels.
Note
: The Optimize Function is
not
available for Static Mode.
If the Wheel is out of balance, weight goes on the Center Plane when using Static Mode.
To Balance a Wheel using Static Mode
:
1.
Make sure you are wearing ANSI-approved eye protection: safety glasses, face shield, or goggles.
2.
Visually inspect the Balancer to make sure everything is in place. The Hood should be
up
.
3.
Mount the Wheel you want to balance.
Refer to
Mounting a Wheel
for mounting instructions, if needed.
4.
Turn the Balancer Off and then back On, to reset it.
5.
On the Control Panel, press the
F
button until the
STA
(Static) indicator is lit.
6.
Pull out the Inner Arm and place it on the
Center Plane
and hold it there;
wait for the Balancer
to beep
.
7.
When the Balancer beeps, return the Inner Arm to its normal location.
Numerical values appear in the Inner and Outer Windows. If they do not, it means the
measurement was not noted correctly by the Balancer and thus you will
not
be able to correctly
balance the Wheel. Start over at Step 4.
8.
Lower the Hood; the Wheel spins briefly.
9.
Raise the Hood when the Wheel stops.
The Inner Window shows
St
and the Center Plane indicator is lit.
The Outer Window shows the weight you need to add to the Center Plane, if weight needs to be
added.
10.
Turn the Wheel slowly to find the best location to put the weight.
11.
When the Wheel is in the right location, it automatically locks and a laser beam appears at the spot
where the Balancer wants you to add the weight.
12.
Add the correct amount of weight centered on the laser location.
13.
Lower the Hood to spin the Wheel again.
The Outer Window shows
00
When the Wheel is balanced.
Summary of Contents for Laser-Spot LS43B
Page 44: ...LS43B Laser Spot Wheel Balancer 44 P N 5900086 Rev A1 12 212018 Wiring Diagram...
Page 45: ...LS43B Laser Spot Wheel Balancer 45 P N 5900086 Rev A1 12 212018 Labels...
Page 46: ...LS43B Laser Spot Wheel Balancer 46 P N 5900086 Rev A1 12 212018...
Page 63: ...LS43B Laser Spot Wheel Balancer 63 P N 5900086 Rev A1 12 212018 Maintenance Log...
Page 64: ...1645 Lemonwood Drive Santa Paula CA 93060 USA 2018 BendPak Inc All rights reserved bendpak com...