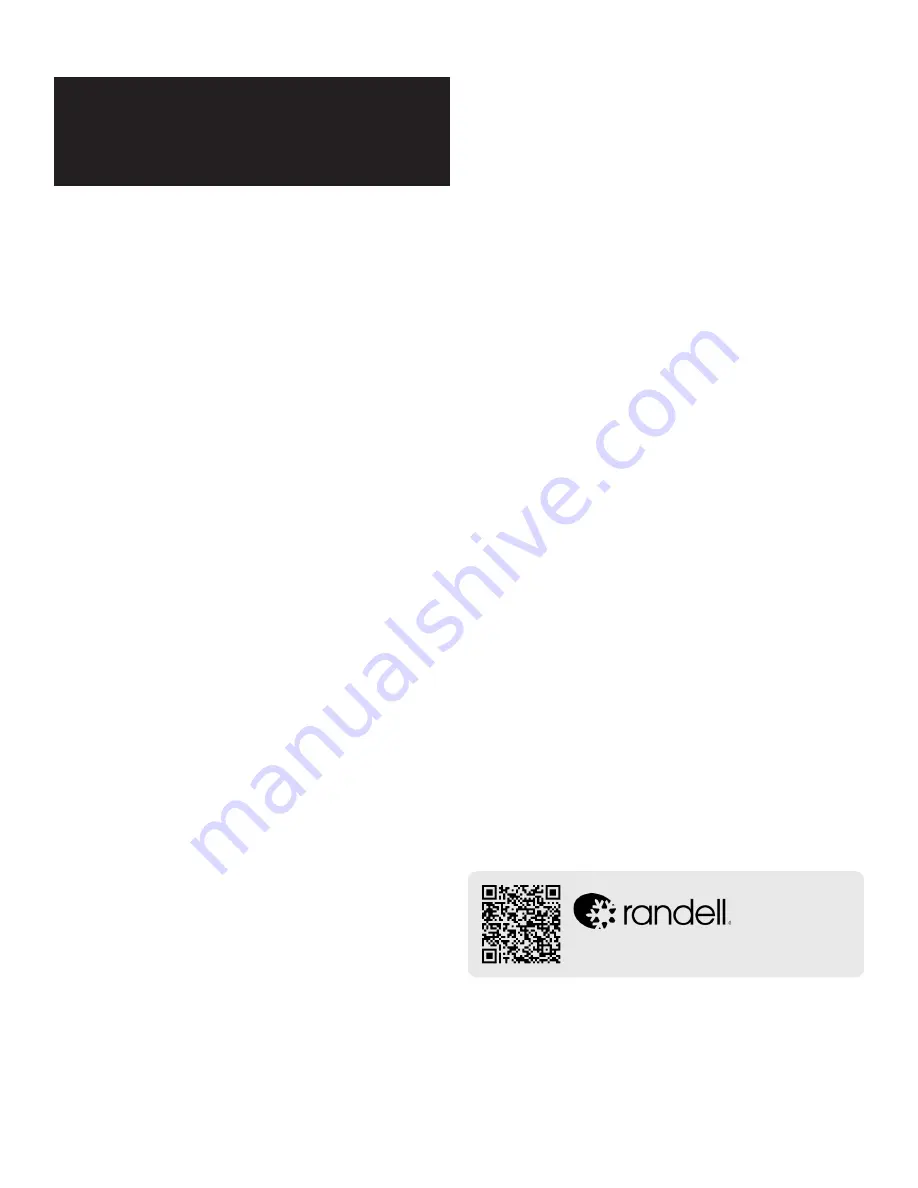
9
OM-RCS-24 SERIES CHEESER STATION
SERVICE
CAUTION: COMPONENT PARTS SHALL BE REPLACED WITH FACTORY OEM PARTS.
SERVICE WORK SHALL BE DONE BY FACTORY AUTHORIZED SERVICE
PERSONNEL, SO AS TO MINIMIZE THE RISK OF POSSIBLE IGNITION DUE TO
INCORRECT PARTS OR IMPROPER SERVICE.
CAUTION: BEFORE MAKING ANY REPAIRS, ENSURE THE UNIT IS DISCONNECTED
FROM ITS POWER SOURCE.
This piece of equipment uses a R290 Refrigeration system. This equipment has
been clearly marked on the serial tag the type of refrigerant that is being used.
There is also a warning labels stating that the unit contains R290 refrigerant. R290
is safe to use as long as you follow these warning labels.
No smoking or open flames when servicing this equipment. If needed, use a CO2
or powder type fire extinguisher.
Replacement parts used on any R290 Refrigeration system cabinet must have
specific UL certification for non-sparking components.
Only authorized service technician, certified in R290 system should service this
equipment.
MANIFOLD SET
A R134A manifold set can be used for servicing this equipment.
REFRIGERANT RECOVERY
Follow all national and local regulations for R-290 refrigerant recovery.
LEAKING CHECKING AND REPAIR
Leak check an R-290 system the same way you would an R-134a or R-404A
system with the following exceptions.
1. Do not use a Halid leak detector on a R290 system.
2. Electronic leak detector must be designated specifically for combustible gas.
Use of a bubble solution or an ultrasonic leak detector are acceptable.
When repairing a leak, it is recommended using oxygen free dry nitrogen with a
trace gas not exceeding 200PSI.
When accessing an R290 system, piercing valves are not to remain on the
equipment in a permanent manner. After charge is recovered, Schrader valves
are to be installed on the process stubs. Proper charge is to be weighed into the
system and the system is to be leak checked afterwards.
The R290 equipment must have red process tubes and other devices through
which the refrigerant is serviced, such as any service port. This color marking
must remain on the equipment. If marking is removed, it must be replace and
extend at least 2.5 centimeters (1”) from the compressor.
CHARGING
Follow the charge amount specified on the data tag. It is recommended to use the
shortest hoses possible to prevent undercharging.
• Ensure the system is sealed and leak checked
• Evacuate system to a minimum 500 micron
• Weigh in correct charge
• Leak check the system again
• Bleed the refrigerant from the high side hose to the low side hose
• Disconnect the hoses
• Remove line taps
WARRANTY
Congratulations on the purchase of your new Unified Brands equipment. We hope you
enjoy many years of reliable service in connection with the same. Please review all of
the important safety and operational information contained in the Operator’s Manual
for this equipment before it is placed in service. If you have any questions related to
equipment set up, operations, or service, please call 888-994-7636.
In addition, please review the sales terms and conditions set forth below.
*****IMPORTANT NOTICE*****
WARRANTIES, LIMITATIONS ON WARRANTIES, AND LIMITATION OF REMEDIES
The following Warranties, Limitation on Warranties, and Limitation of Remedies are
included in the terms of sale for this product. Please read this entire warranty and all
warranty modifications, disclaimers, and limitations of remedies set forth herein before
accepting or using this equipment or product. Customer acknowledges and accepts
the provisions of this notice by Customer’s acceptance and use of the product. If these
provisions are not acceptable and agreed to by Customer, then please return this
product in its unused condition to Unified Brands or a Unified Brands authorized dealer.
UNIFIED BRANDS warrants this product against defects in material and workmanship
under normal use and services for which this product was designed. This warranty
runs only to the original end user and is in lieu of any other liability for defects.
THE WARRANTIES EXPRESSED IN THESE TERMS AND CONDITIONS ARE IN PLACE
OF ANY AND ALL OTHER EXPRESS WARRANTIES (UNLESS SEPARATELY STATED IN
PRINTED MATERIAL PREPARED BY US DESCRIBING OUR EQUIPMENT) AND EXCLUDE
ALL IMPLIED WARRANTIES, INCLUDING, BUT NOT LIMITED TO, ANY WARRANTY OF
MERCHANTABILITY OR FITNESS FOR ANY PARTICULAR PURPOSE; NOR ARE THERE
ANY OTHER WARRANTIES, EXPRESS OR IMPLIED, BY OPERATION OF LAW OR
OTHERWISE. In no event shall UNIFIED BRANDS be liable for damages or delay or
for any consequential, special or contingent damages arising out of any breach of
our warranty, whether or not we have knowledge of specific needs or our employees
or agents have given any specific assurances. Anyone claiming that there has been
a breach of warranty by UNIFIED BRANDS must give us written notice within THIRTY
(30) days after discovery of the relevant defect or the right to assert such claim will
have been waived conclusively and provided further that any such claim must also be
asserted within the general warranty period for such equipment and/or parts.
UNIFIED BRANDS will not be liable for any expense incurred without our prior written
authorization for alterations made outside of our factory or for repairs which are
not performed by UNIFIED BRANDS authorized service departments using UNIFIED
BRANDS factory parts. Nor shall we be responsible for the performance of equipment
as to which any repairs, revisions or alterations have been made by others.
THE EXCLUSIVE REMEDY OF THE USER OR BUYER AND THE EXCLUSIVE LIABILITY OF
UNIFIED BRANDS OR ANY SELLER OF UNIFIED BRANDS PRODUCTS, FOR ANY AND ALL
CLAIMS, LOSSES, INJURIES, OR DAMAGES (INCLUDING CLAIMS BASED ON BREACH
OF WARRANTY, CONTRACT, NEGLIGENCE, TORT, STRICT LIABILITY, OR OTHERWISE)
RESULTING FROM OR ARISING OUT OF THE USE OF HANDLING OF THIS PRODUCT,
SHALL BE THE RETURN OF THE PURCHASE PRICE OR AN AMOUNT NOT TO EXCEED
THE ORIGINAL PURCHASE PRICE OF THE PRODUCT OR, AT THE ELECTION OF UNIFIED
BRANDS OR THE SELLER, THE REPLACEMENT OF THE PRODUCT.
https://unifiedbrands.net/
Randell-Warranty-Information