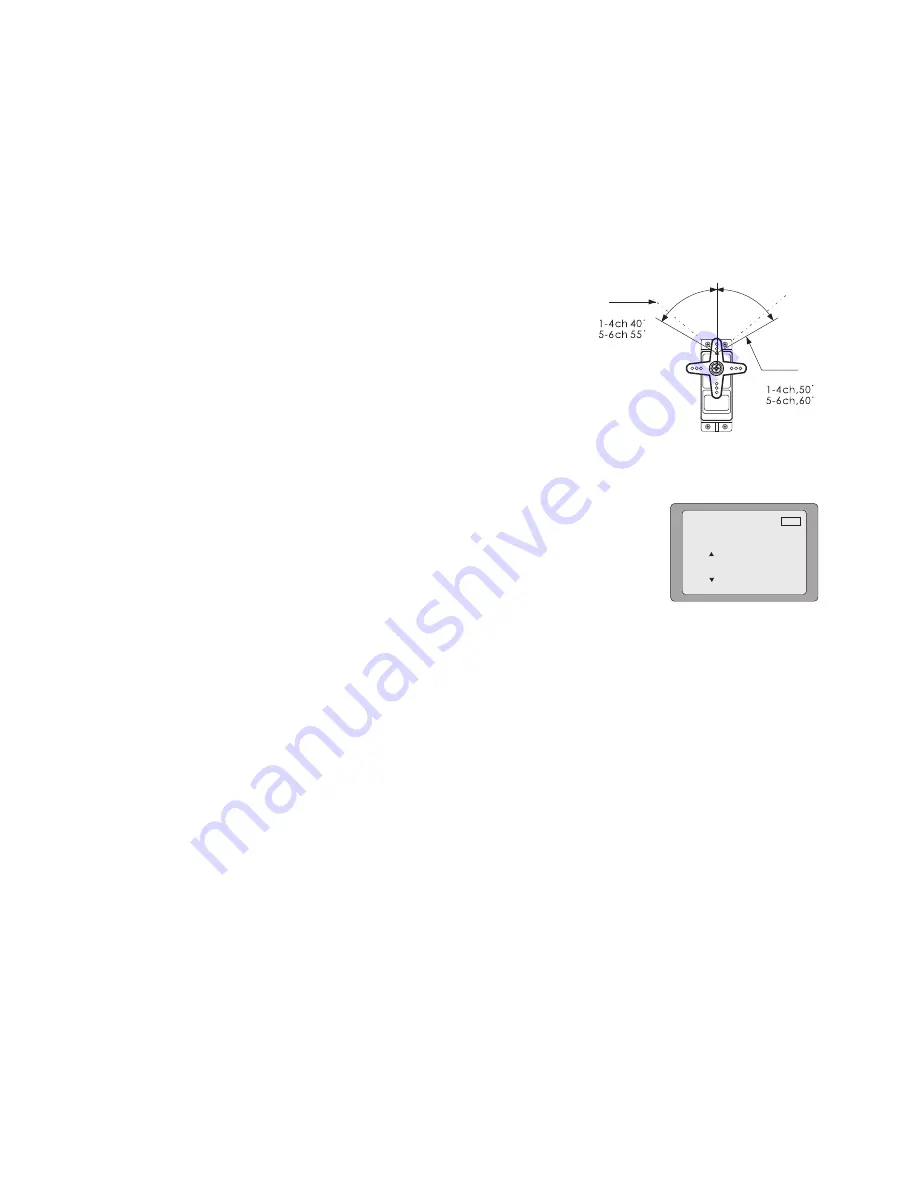
4. Position the dual rate switch where desired for the value you wish to change.
5. Enter the amount of exponential with the DATA INPUT lever. (As stated above, an exponential value with a “-” in front
of it makes the initial servo movement less, or “softer.”)
6. Flip the switch to the other position to enter the exponential value for that switch position.
7. Repeat for the settings on the other channel.
1
2
3
4
0
-
120
%
At 120
%
At 100
%
EPA - End Point Adjustment
Note:
Since changing the “end points” will also change the dual rates, the end points should be set prior to setting the dual rates. If you
set the dual rates first, and then go back and change the end points, the dual rate throws will also change.
The EPA function is designed to “fine tune” the servo throws in cases where
changing the pushrod hookup will not achieve the correct throw. The pushrods
should first be connected to the servo arms and control horns so the correct, or
near correct control surface throw will be achieved. THEN the EPAs may be used
to make small changes in the servo throw until the desired control throw is
achieved. The control throws should be set up so that the “end points” are as near
to 100% as possible. If the EPA values must be set below 70% or above 120% to
get the desired throw, you should strongly consider changing the pushrod
connections so the values can be set closer to 100%. (When the EPA is set to
100% the maximum servo throw for channels 1, 2, 3 & 4 is approximately 40
°
and approximately 55
°
for channels 5 & 6.)
To set the end points:
1. Enter the programming mode and use the MODE key to access the “EPA” screen. The
channel number being adjusted will show on the left side on the screen and the % symbol
will be flashing.
2. To change the RIGHT aileron throw move the aileron stick to the right, then push the
DATA INPUT lever up or down to change the value and the throw.
PPM
1
CH
100
%
Epa
3. Move the stick to the left and use the DATA INPUT lever to change the LEFT aileron throw.
4. Use the SELECT key to display the other channels and set the other end points. Notice that moving the stick (or switch
or dial) from one end to the other changes the value displayed and the position of the arrow for that “end” of the control
input.
TRIM - Trim Settings
There are four trim levers (“trims”) on the front of the transmitter. Three of the trims are for adjusting the neutral position
of the aileron, elevator and rudder servos. The fourth trim is for setting the idle r.p.m. of the engine when the throttle
stick is all the way down. The intended use of the trims is to make small servo adjustments, in flight, to get the model
properly “trimmed” (so it will fly straight-and-level). Because the trims are intended to be used while the model is in
flight, you do not have to “enter the program” to adjust the trims. Simply push or pull on the trim levers while flying and
the neutral position of the servos will shift. Keep in mind that you should start out with the control surfaces centered
when the servos are centered and the trims are “zeroed” (or near zero). THEN you can adjust the trims once airborne.
Center the servos:
1. Turn on the transmitter and receiver. Operate the controls to make sure the servos respond in the correct direction.
Use the reversing function to reverse any servos necessary.
2. Center the throttle control stick.
3. Place the servo arms on the servos so they are perpendicular to the pushrods (see page 5). It is okay to cut off any
unused servo arms.
4. Connect the pushrods to the control surfaces. Adjust the length of the pushrods until the control surfaces are
centered when the servos are centered.
Note:
The throttle trim affects the throttle servo only when the throttle stick is below “1/2 stick.” This way, the final closing of the
carburetor can be adjusted without affecting the servo throughout the rest of the range.
9