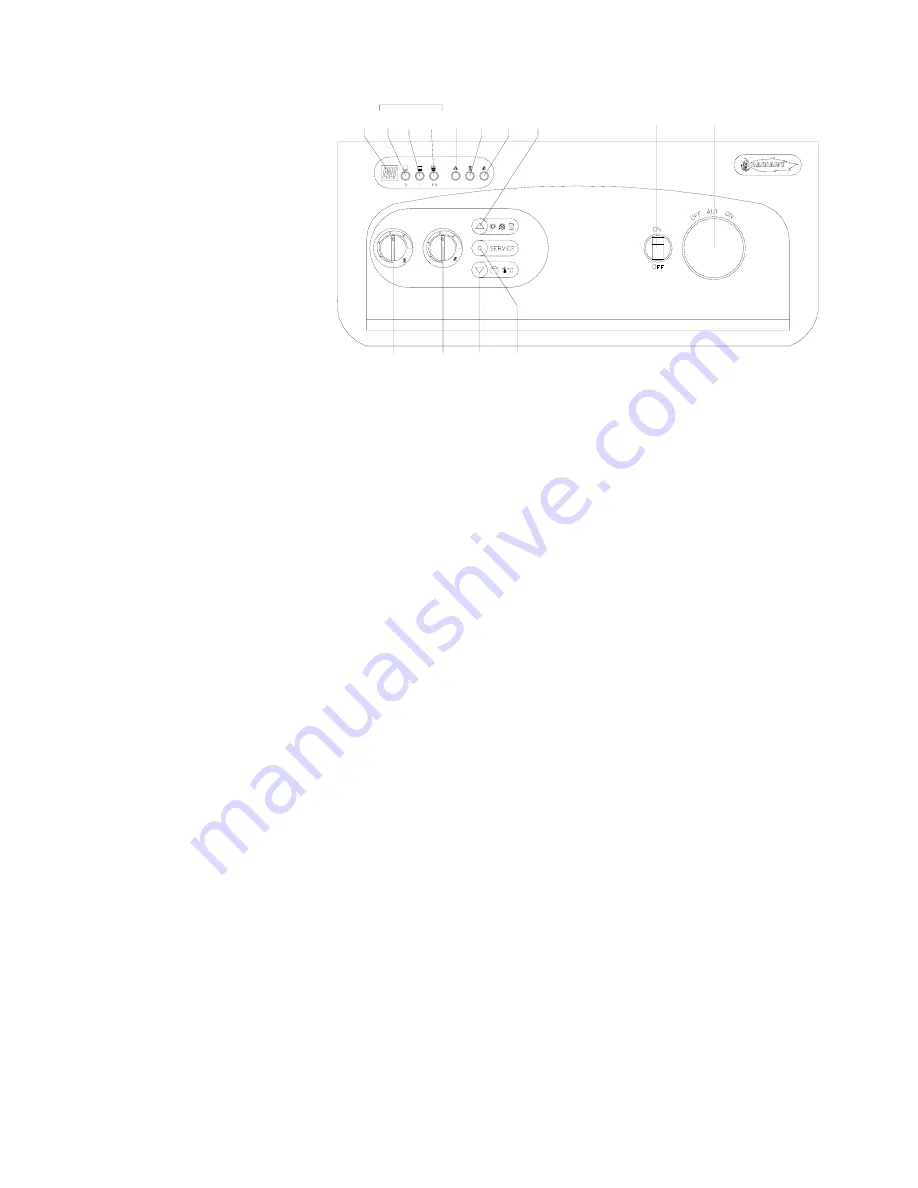
Installation Manual
COMBI - TA01A011.B1003
9
CONTROL PANEL
LEGEND
(see fig. 1)
1.
ON / OFF POWER SWITCH
2.
HEATING TEMPERATURE
ADJUSTMENT KNOB
3.
DOMESTIC HOT WATER
TEMPERATURE ADJUSTMENT KNOB
4.
OUTSIDE TEMPERATURE DISPLAY
PAD (ONLY WITH OPTIONAL OUTSIDE
TEMPERATURE SENSOR FITTED)
5.
CHIMNEY-SWEEPER SELECTION PAD
/ PARAMETER SETTING SERVICE PAD
6.
MODE SELECTION PAD (SUMMER
ONLY / WINTER ONLY / SUMMER
AND WINTER)
7.
SPACE FOR AN OPTIONAL TIME
CLOCK
8.
DOMESTIC HOT WATER MODE
(STABLE LIGHT)
DOMESTIC HOT WATER OPERATION
(FLASHING LIGHT)
9.
HEATING MODE (STABLE LIGHT)
HEATING OPERATION (FLASHING LIGHT)
10.
GENERAL LOCK-OUT WITH FLASHING ERROR CODE ON DISPLAY (14)
11.
WATER PRESSURE LEVEL
1.5 BAR
INDICATOR
12.
WATER PRESSURE LEVEL
1 BAR
INDICATOR
13.
WATER DEFICIENCY INDICATOR
14.
TEMPERATURE AND ERROR CODES DISPLAY
ERROR CODES:
1.
IONISATION LOCK-OUT
2.
HIGH LIMIT THERMOSTAT LOCK-OUT
3.
FLUE SAFETY THERMOSTAT LOCK-OUT (Not applicable)
4.
WATER PRESSURE SWITCH LOCK-OUT
5.
HEATING SENSOR FAILURE
6.
DOMESTIC HOT WATER SENSOR FAILURE
12.
STORAGE TANK WATER SENSOR FAILURE
14.
AIR PRESSURE SWITCH / WATER PRESSURE SWITCH LOCK-OUT
22.
REQUEST OF PARAMETERS RE-SETTING
STARTING UP THE BOILER
After connecting up the water supply, before starting up the boiler, carry out the following procedures:
Preliminary procedure
•
Do as follows:
•
make sure the power supply for the boiler is the same as that
stated on the plate (230V - 50Hz) and that the live, neutral and
earth connections have been properly connected;
•
make sure the type of gas being supplied is the same as the type
for which the boiler has been tested and approved (see plate
data);
•
make sure the unit is properly earthed;
•
make sure there are no flammable liquids or materials in the
immediate vicinity of the boiler;
•
make sure that any shut-off valves in the heating circuit are
open;
•
open the gas cock and check the gas seals, making sure the
counter shows no sign of leaks; in any case, double check by
using a soapy solution and eliminate all eventual leaks. The
checking procedure for the gas burner attachment is carried out
with the boiler working;
•
make sure the electrical mains switch is OFF;
•
remove the front cover by pulling it forwards;
•
undo the side screws and rotate the panel downwards
Filling the system
After making sure the gas cock is closed, fill the heating system as follows;
•
fill the system until a pressure of 1.5 bar has been reached (light no. 11 ON; see fig. 1) and then close the filling tap (see fig. 2 pag 10)
located under the boiler;
•
make sure the cap on the auto air vent valve is slightly loose to allow air to escape from the system (see fig. 1 pag 10);
•
undo the cap on the circulation pump to eliminate any eventual air locks; it is a good idea to purge all radiators of air at this point too;
•
before starting up the boiler the water pressure must be checked again; if this is seen to be below 0.5 bar , bring it back up to 1.5 bar
(light no. 11 ON; see fig. 1)
and then close the filling tap
located under the boiler;
ELECTRONIC WATER
PRESSURE GAUGE
10
2
3
14 13
11
4
5
9
8
6
7
1
12
Fig. 1
Summary of Contents for RSF 30
Page 2: ......