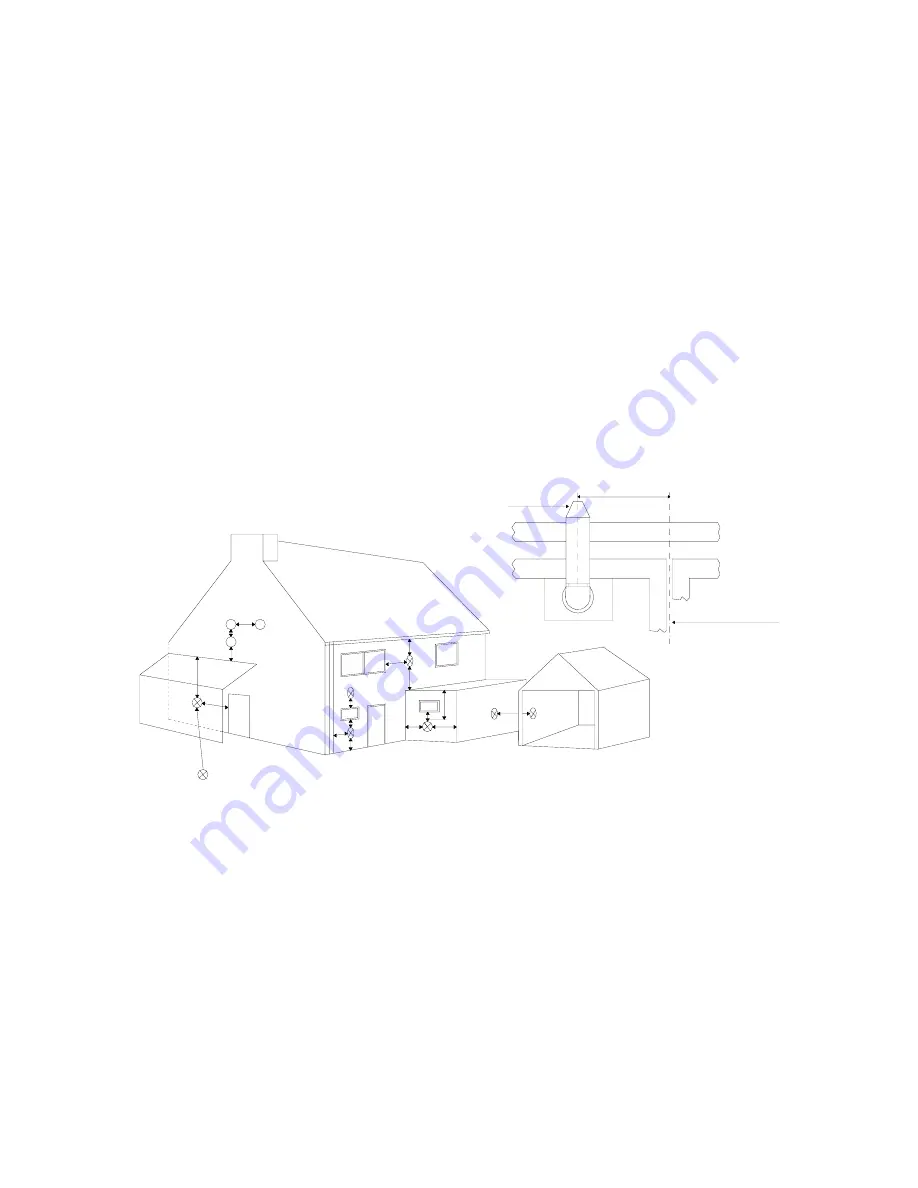
Installation Manual
SYSTEM BOILER – Cod. 99951NA – November 2002
6
FLUE POSITION
IMPORTANT: THE FLUE SYSTEM SHALL BE INSTALLED IN ACCORDANCE WITH THE RECOMMENDATIONS CONTAINED IN BS
5440:1.
The boiler MUST be installed so that the terminal is exposed to the external air.
It is important that the position of the terminal allows free passage of air across it at all times.
If the terminal discharges into a pathway or passageway check that combustion products will not cause nuisance and that the terminal will
not obstruct the passageway.
In certain weather conditions a terminal may emit a plume of steam. Positions where this would cause a nuisance should be avoided.
IMPORTANT REQUIREMENT: The correct dimensional relationship between the terminal and any obstruction, openable window or
ventilator as shown in Fig 1 pag.7 It is ESSENTIAL TO ENSURE, in practice, that products of combustion discharging from the terminal
cannot re-enter the building, or any other adjacent building, through ventilators, windows, doors, other sources of natural air infiltration, or
forced ventilation/air conditioning systems. If this should occur, the appliance MUST BE TURNED OFF IMMEDIATELY and the local gas
region consulted.
Where the lowest part of the terminal is fitted less than 2m (6.6ft) above a balcony, above ground, or above a flat roof to which people have
access, the terminal MUST be protected by a purpose designed guard.
Where the terminal is fitted within 850mm (34in) of a plastic or painted gutter, or 450mm (18in) of painted eaves, an aluminium shield of at
least 1000 mm (40in) long should be fitted to the underside of the gutter painted surface.
The air inlet/products outlet duct and the terminal of the boiler MUST NOT be closer than 25mm (1in) to combustible material.
TERMINAL POSITION
J
E
A
G
M
F
F
A
D
H,I
TOP VIEW REAR FLUE
D
G
L
K
G
N
B.C
TERMINAL
ASSEMBLY
PROPERTY BOUNDARY LINE
300 min
A
Directly below an openable window, air vent or any other ventilation opening.
300 mm
B
Below gutter, drain pipes or soil pipes.
25 mm
C
Below eaves.
25 mm
D
Below balcony or carport roof.
25 mm
E
From vertical drain pipes or soil pipes.
25 mm
F
From internal or external corners.
25 mm
G
Above adjacent ground, roof or balcony level.
300 mm
H
From a surface facing the terminal.
600 mm
I
Facing the terminals.
1200 mm
J
From opening (door, window)in the carport into dwelling.
1200 mm
K
Vertically from a terminal on the same wall
1500 mm
L
Horizontally from a terminal on the same wall
300 mm
M
Above an opening, air brick, opening window etc.
300 mm
N
Horizontally to an opening, air brick, opening window etc.
300 mm
Fig. 1