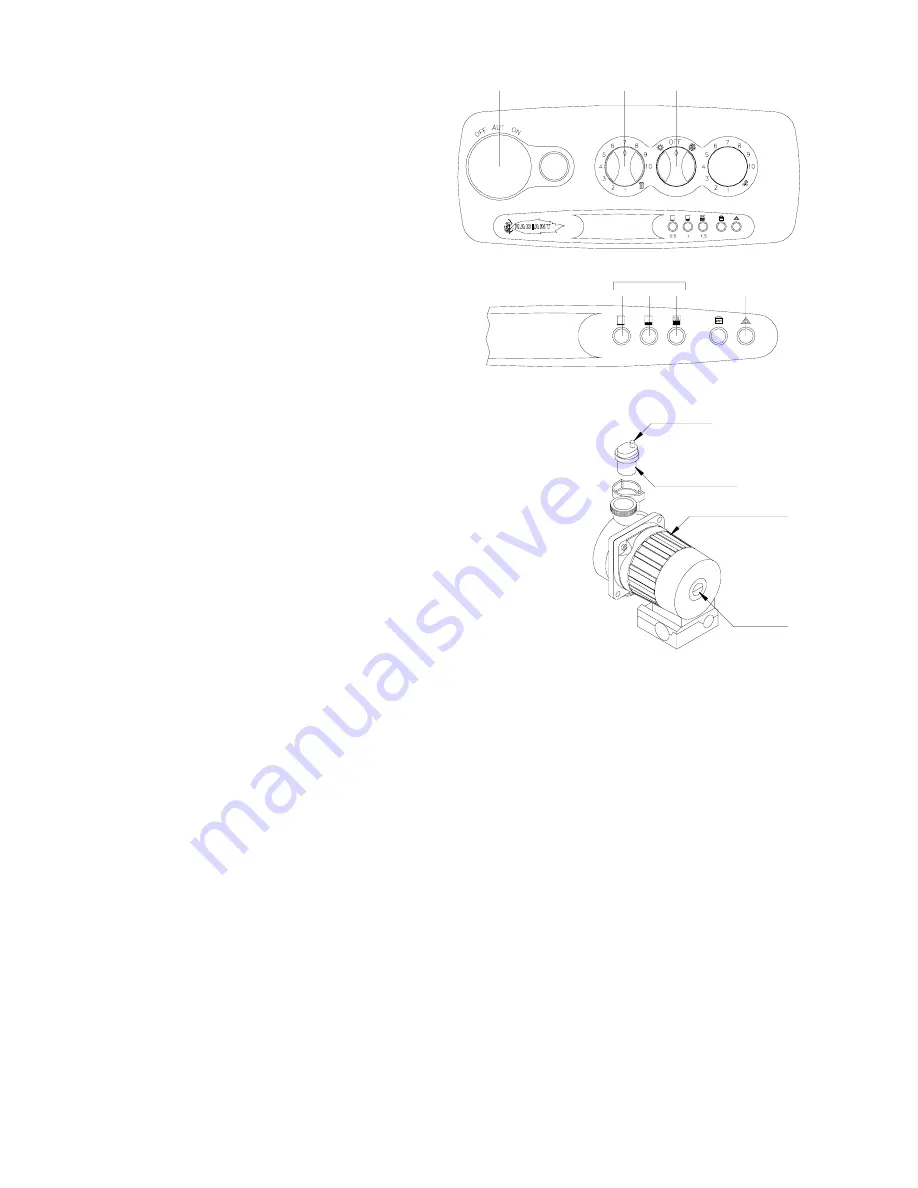
Installation Manual
SYSTEM BOILER – Cod. 99951NA – November 2002
10
0.5
1
1.5
PRESSURE GAUGE
ELECTRONIC WATER
4
5
6
3
2
1
7
AIR VENT
PUMP CUP
AIR VENT VALVE
CIRCULATING PUMP
VALVE CAP
INSTRUMENT PANEL
LEGEND
(see fig. 1)
1.
SUMMER-WINTER ON-OFF SWITCH
2.
HEATING TEMPERATURE ADJUSTMENT KNOB
3.
SPACE FOR ADDING AN OPTIONAL TIMER
SELF- DIAGNOSTIC LEGEND
(see fig. 2)
4.
WARNING: LACK OF WATER IN THE SYSTEM
5.
WATER PRESSURE LEVEL 1 BAR
6.
WATER PRESSURE LEVEL 1.5 BAR
7.
WARNING: CHIMNEY SAFETY DEVICE
ON R OPEN CHAMBER MODEL
8.
WARNING: LOCK-OUT INDICATOR (FIXED LIGHTS
ONLY – NO FLASHING)
STARTING UP THE BOILER FOR 1
st
TIME
After connecting up the water supply, before starting up the boiler, carry out
the following procedures:
Preliminary procedure
Do as follows:
make sure the power supply for the boiler is the same as that stated on
the plate (230V - 50Hz) and that the live, neutral and earth connections
have been properly connected;
make sure the type of gas being supplied is the same as the type for
which the boiler has been tested and calibrated;
make sure the unit is properly earthed;
make sure there are no flammable liquids or materials in the immediate
vicinity of the boiler;
make sure that any shut-off valves in the heating circuit are open;
open the gas cock and check the gas seals, making sure the counter shows no sign of leaks; in any case, double check by
using a soapy solution and eliminate all eventual leaks. The checking procedure for the gas burner attachment is carried
out with the boiler working;
make sure the electrical mains switch is OFF;
remove the front cover by pulling it forwards;
undo the side screws and rotate the panel downwards
FILLING THE SYSTEM
Fill the heating system as follows, making sure that the gas cock is closed:
•
open the tap on the filling loop and fill the system until a pressure of 1.5 bar has been reached (light no. 6 fig.2) and then
close the tap;
•
make sure the cap on the jolly valve is slightly loose to allow air to escape from the system (see fig. 3).
•
undo the cap on the circulation pump to eliminate any eventual air locks. It is a good idea to purge all radiators of air at this
point too;
•
before starting up the boiler the water pressure must be checked again; if this is seen to be below 0.5 bar, bring it back up
to 1.5 bar and then close the tap on the filling loop;
•
switch on the electrical power supply to the boiler;
•
turn the selector switch to the WINTER
position (see fig.1), after a few seconds the pump will come into action;
•
once the boiler is working, if any noises are heard in the system, repeat the above air purging procedures until there is no
air left in the system;
•
check there are no obstructions in the exhaust duct;
Fig. 1
Fig. 2
Fig. 3