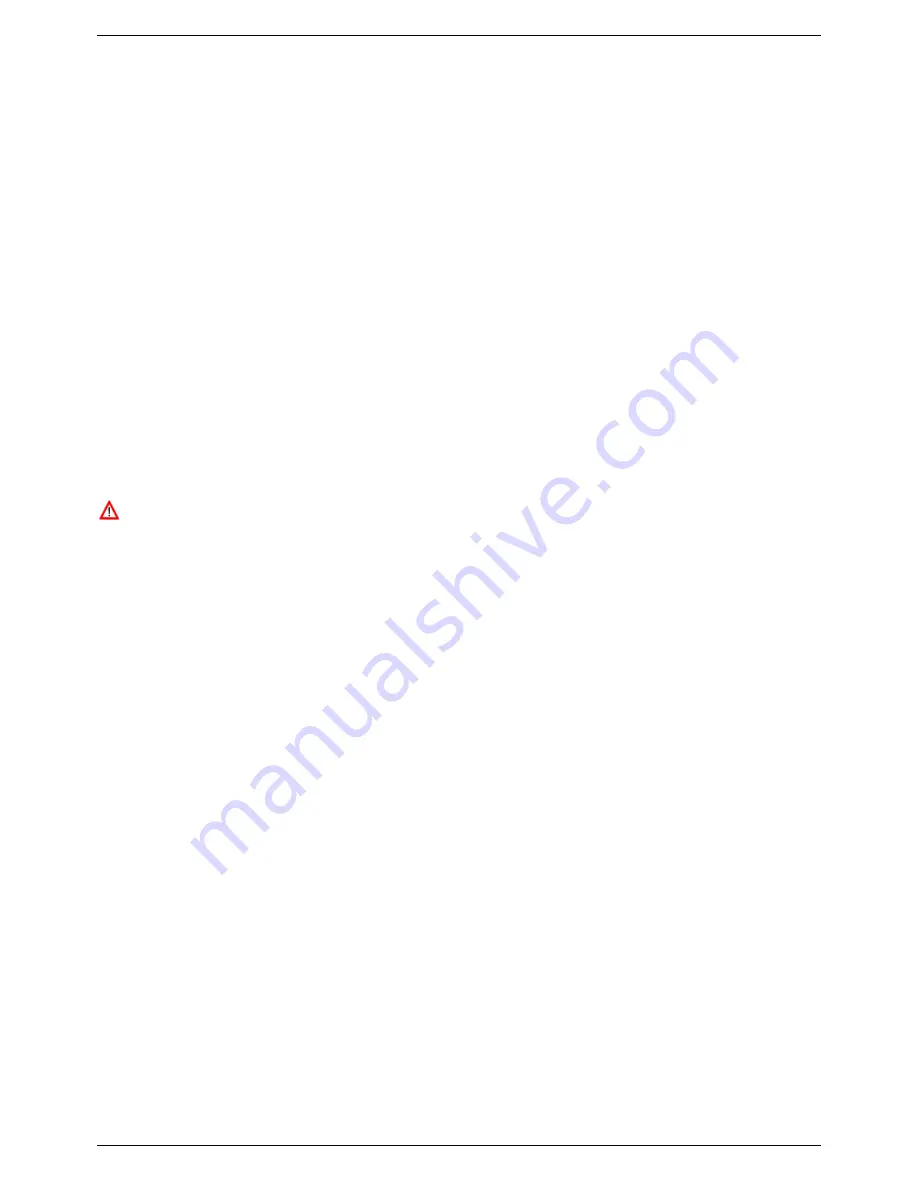
INSTALLATION INSTRUCTIONS
11
3. INSTALLATION
(authorised personnel)
3.1 Reference standard
This appliance meets the requirements of:
- IPX4D rating for electrical appliances.
- EMC DIRECTIVE 89/336 CEE
- LVD DIRECTIVE 73/23 CEE
- BOILER EFFICIENCY DIRECTIVE 92/42 CEE
Failure to install a gas appliance correctly and in accordance with the above norms could lead to prosecution. It is in
the interest of the installer and safety that the law is complied with.
The manufacturers instructions form an integral part of the installation and should be left with the appliance but do
not over ride in anyway statutory obligations.
3.2 Boiler room – Installation requirements
Please refer to local and national standards in force in the Country of destination of the product. In particular the
manufacturer recommends:
The presence of threaded connections on the gas line, require that the room in which the appliance is
installed is ventilated by means of air intakes.
Summary of Contents for RK 25 /B
Page 2: ......