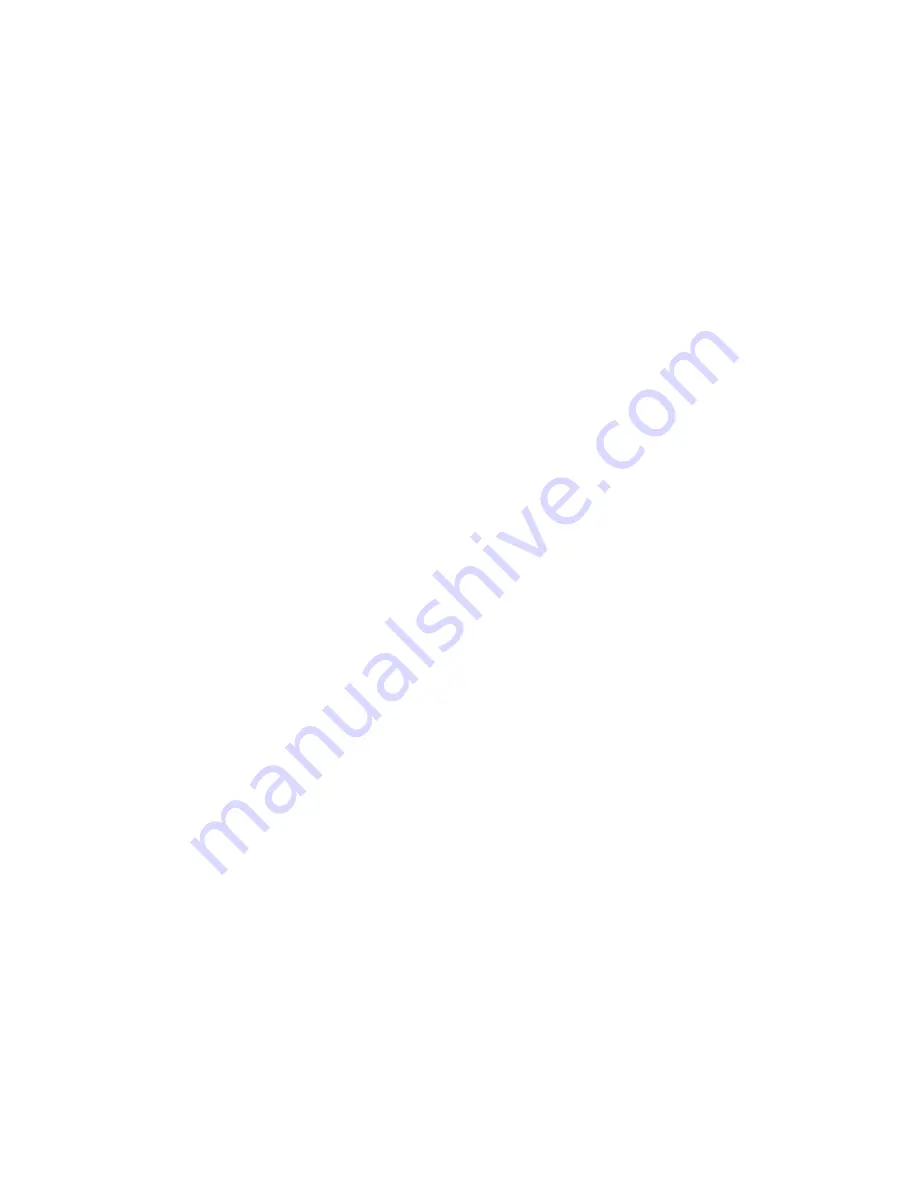
17
Maintenance Procedures
Maintenance must be carried out in accordance with these instructions, and
must be conducted by designated, qualified and competent personnel.
This mixing valve is designed for minimal maintenance under conditions of normal
use.
External surfaces may be wiped clean with a soft cloth, and if necessary, a mild
washing-up type detergent or soap solution can be used.
Warning!
Many household and industrial cleaning products contain mild abrasives
and chemical concentrates, and should not be used on polished, chromed or plastic
surfaces.
Should an internal malfunction occur then this will probably require cartridge renewal.
The cartridge assembly and check valves contain no user-serviceable parts, and
must not be dismantled.
Components are precision-made, so care must be taken while servicing to avoid
damage.
When ordering spare parts, please state product type, i.e. Rada 320 c, and identify
part name and number (refer to
PARTS LIST
). A Seal pack is available, containing
all the seals that may be necessary for renewal during maintenance or servicing.
Lubricants
Important! All seals are pre-lubricated. If you need to lubricate the seals, use
only a small amount of silicone-only based lubricants on this product. Do not
use oil-based or other lubricant types as these may cause rapid deterioration of
seals.
Maintenance Procedure - Cartridge Assembly
Removal
1.
Turn the isolation screw on the isolator valves through 90
o
to isolate the water
supplies to the valve (refer to
Figure 4
). Open an outlet fitting to release pressure
and to assist the draining of residual water.
2.
Remove the temperature knob concealing cap and then the screw using the 3
mm hexagonal wrench (supplied). Remove the temperature knob, the temperature
indicating ring and the hub.
3.
Remove the six screws holding the cartridge assembly into the body.
4.
Use a suitable tool inserted into the cut-outs to lever the cartridge assembly from
the body.
5.
Remove the cartridge assembly from the body.