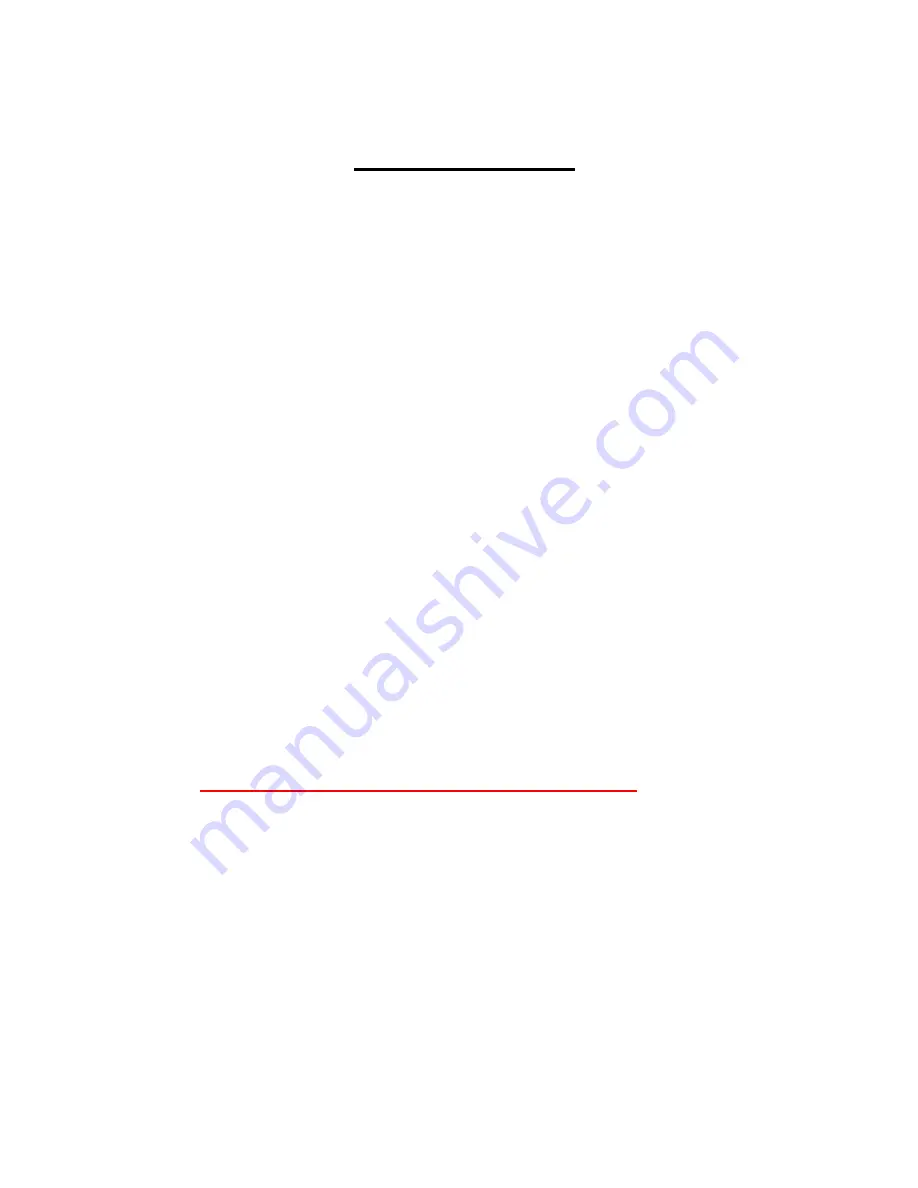
15
FAULT DIAGNOSTICS
1.
Power light not lit
Check machine on/off switch is in the ‘on’ position
Check Input power to machine
Check plug wiring
Check mains trip / fuses
2.
No output - Fan runs - Power light is lit
Check torch connections are secure and torch switch operation, try replacing plasma
cutting torch
3.
No output - Power light is lit - Warning light is lit
Welding application may have exceeded recommended duty cycle, allow machine to
cool down until the warning light goes out.
4.
No output – Power light is lit – Air at torch tip – No Pilot Arc
Check condition of torch consumables and replace if worn
Check pilot arc protecting fuse on front panel of machine and replace if blow – If fuse
keeps blowing contact R-Tech for repair / replacement torch
Please ensure machine is switched off before checking fuses
Check for water in water trap at rear of machine, if water is present, drain air
compressor, clean water out of air lines, empty water trap by pressing water release
button on bottom of air regulator water trap. Fit new consumables as per instructions
earlier in this manual
HF PCB Failure – Contact R-Tech for repair
5.
Machine keeps overheating - Warning light is lit on machine
Check if fan is running – if not contact R-Tech for repair
Check the cooling vents for obstruction, blow out machine with clean dry low pressure
Summary of Contents for PLASMA 80HF
Page 2: ...2 Thank you for selecting the R Tech Plasma 80HF Inverter Plasma Cutter...
Page 17: ...17 Plasma torch switch TS1 Wiring Diagram...
Page 18: ...18...
Page 19: ...19...