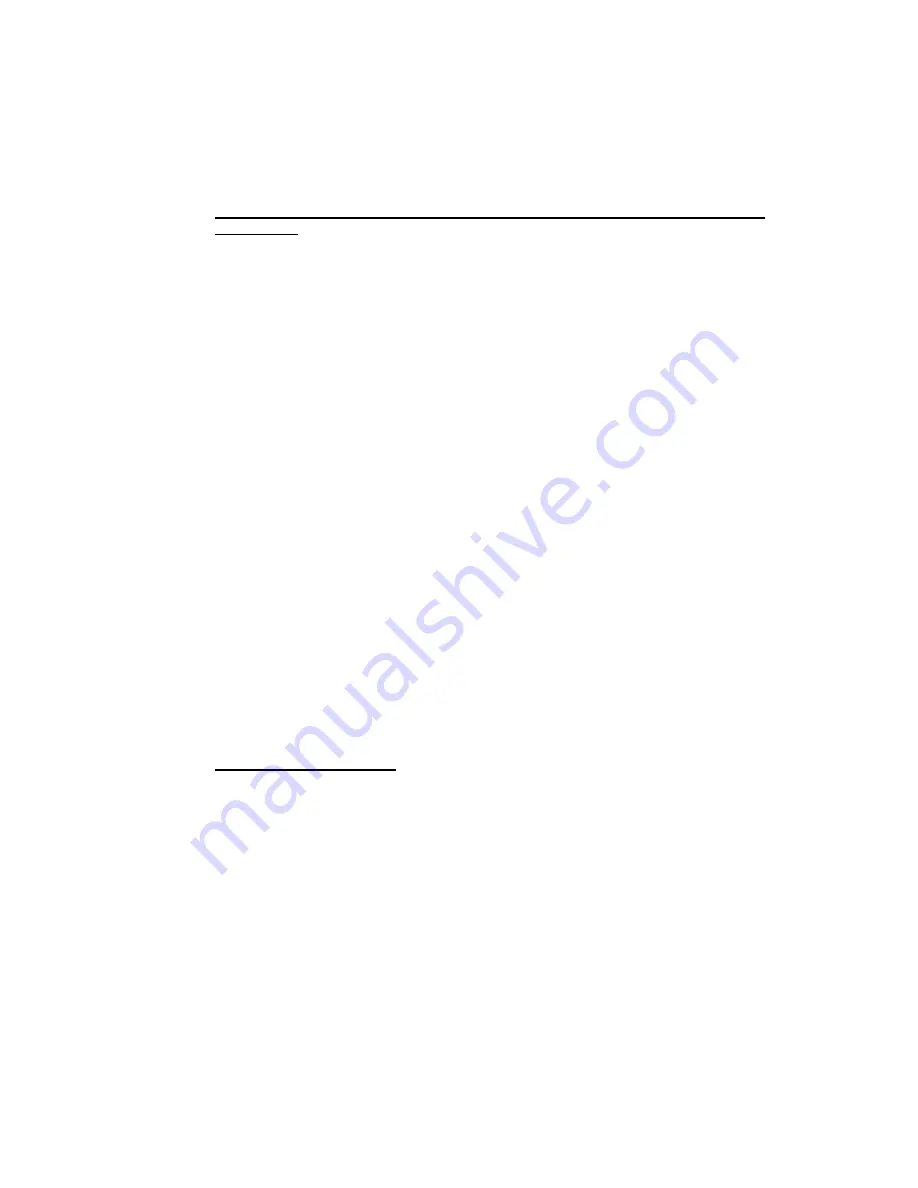
15
15
Operating Machine
1.
Ensure machine has been setup as previously stated
2.
Fit reel of wire to machine, ensuring correct size rollers are fitted. For steel only use wire
of 0.6mm, 0.8mm and 1.0mm, for aluminium only use wire of 0.8mm, 1.0mm, 1.2mm.
DO NOT USE 1.2MM STEEL WIRE AS THIS WILL OVERLOAD MACHINE AND VOID
WARRANTY
3.
Feed wire into wire feed assy and into guide tube, clamp down top pressure feed rollers
and set tensioner pressure.
4.
Press torch switch and wire will feed to torch head (adjust wire feed speed to approx 3) –
When wire has come through torch to welding tip release trigger.
5.
Turn on gas and set flow rate to approx 14 LPM
6.
Set welding voltage and wire feed speed according to thickness of job
7.
Ensure you are wearing the correct safety clothes & equipment for welding (i.e welding
mask, gloves, apron etc)
8.
Select welding voltage (power) required on front panel
9.
Select wire feed speed required on ‘wire speed’ knob
10.
Set ARC force switch to middle position for medium weld inductance (know as choke on
traditional welding power sources)
Low setting = Soft ARC (less splatter & penetration)
High setting = Strong ARC (more penetration)
11.
Press torch trigger to start welding process.
Note: You can finely adjust the welding current knob to fine tune weld arc length to either
DIP or SPRAY welding
When welding actual voltage and amperage will be shown in corresponding LED display
meters on machine
Tips on welding aluminium
When welding aluminium as the wire is much softer than steel wire you have to fit a teflon
liner in place of the steel liner in mig torch, this is so the wire feeds much smoother and
stops it snarling at rollers.
To fit a teflon liner, remove steel liner from torch and fit teflon liner so you have about 10
inches left coming out end of mig torch at the machine end. In the brass euro body where
torch fits onto you will see a brass guide tube, remove this tube and fit torch to machine
and cut off excess teflon liner as required. You want the teflon liner to get as close to the
wire feed rollers as possible. Best way to cut liner is with a sharp stanley knife blade.
Next you will need to fit U-Groove rollers made specifically for alloy wire to the feed unit.
These are available from R-Tech. Remove the steel rollers (V-Groove) from the machine
and fit U-Groove rollers ensuring correct size groove is in line with the welding wire
guides. For Aluminium you can use up to 1.2mm wire.
Adjust the wire tensioner to minimum pressure and tighten down until wire is gripped, too
much pressure will deform wire and end up with snarls by rollers.
Fit oversize welding tip. These are available and have and ‘A’ after tip size. I.E 1.0A where
as for steel wire it would just say 1.0
Summary of Contents for I-MIG200
Page 1: ...I MIG200 MIG MMA WELDER OPERATION INSTRUCTIONS www r techwelding co uk...
Page 2: ...2 2...
Page 18: ...18 18 Wiring Diagram...
Page 19: ...19 19...
Page 20: ...20 20...