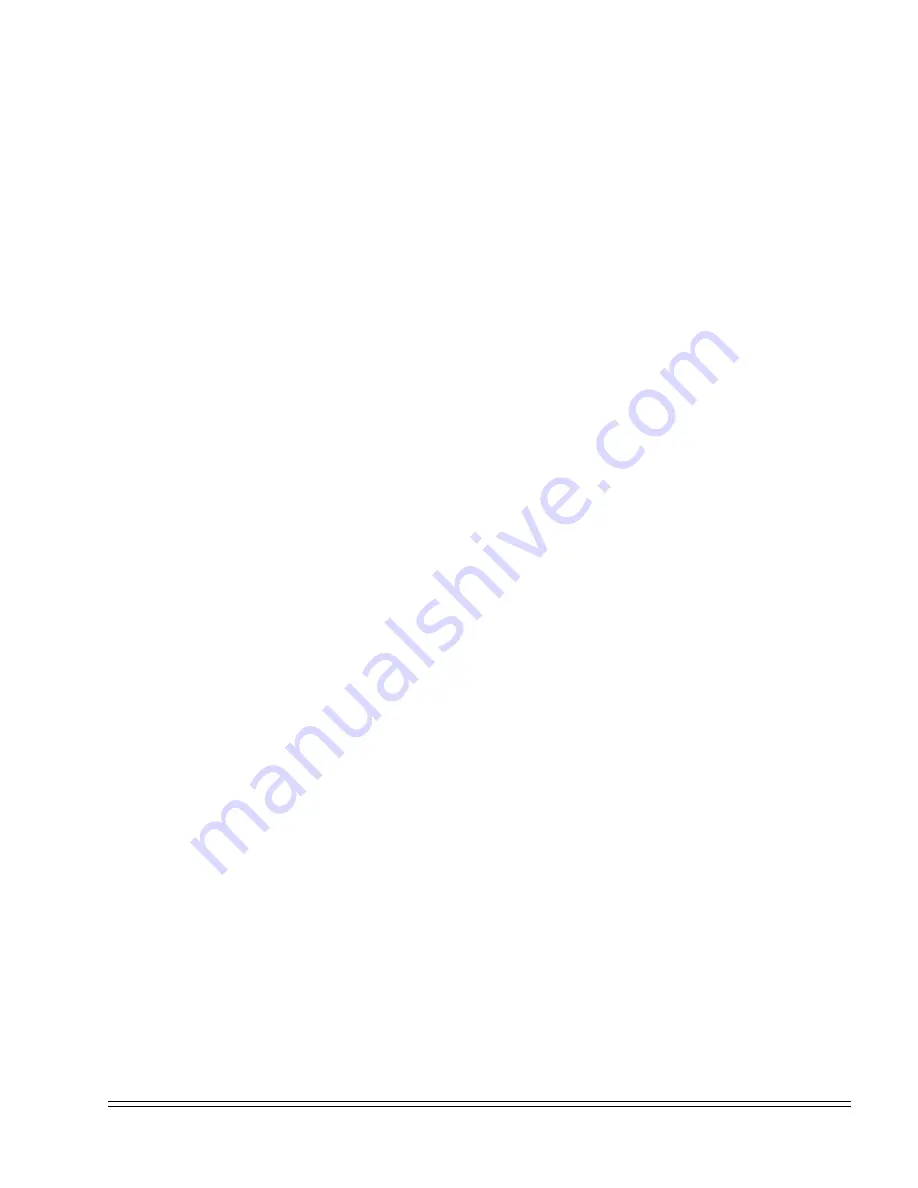
Industrial / Air Master Series
Quincy Compressor
50161-105, March 2008
41
3501 Wismann Lane, Quincy Ill. - 62305-3116
TITLE & LIEN RIGHTS: The equipment shall remain personal property, regardless of how affixed to any realty or
structure. Until the price (including any notes given therefore) of the equipment has been fully paid in cash, Seller
shall, in the event of Buyer’s default, have the right to repossess such equipment.
PATENT INFRINGMENT: If properly notified and given an opportunity to do so with friendly assistance, Seller will
defend Buyer and the ultimate user of the equipment from any actual or alleged infringement of any published United
States patent by the equipment or any part thereof furnished pursuant hereto (other than parts of special design,
construction, or manufacture specified by and originating with Buyer), and will pay all damages and costs awarded
by competent court in any suit thus defended or of which it may have had notice and opportunity to defend as aforesaid.
STANDARD WARRANTY: Seller warrants that products of its own manufacture will be free from defects in
workmanship and materials under normal use and service for the period specified in the product instruction manual.
Warranty for service parts will be Ninety (90) days from date of factory shipment. Electric Motors, gasoline and diesel
engines, electrical apparatus and all other accessories, components and parts not manufactured by Seller are
warranted only to the extent of the original manufacturer’s warranty.
Notice of the alleged defect must be given to the Seller, in writing with all identifying details including serial number,
type of equipment and date of purchase within thirty (30) days of the discovery of the same during the warranty period.
Seller’s sole obligation on this warranty shall be, at its option, to repair or replace or refund the purchase price of any
product or part thereof which proves to be defective. If requested by Seller, such product or part thereof must be
promptly returned to seller, freight prepaid, for inspection.
Seller warrants repaired or replaced parts of its own manufacture against defects in materials and workmanship under
normal use and service for ninety (90) days or for the remainder of the warranty on the product being repaired.
This warranty shall not apply and Seller shall not be responsible or liable for:
(a)
Consequential, collateral or special losses or damages;
(b)
Equipment conditions caused by fair wear and tear, abnormal conditions of use, accident, neglect or misuse
of equipment, improper storage or damage resulting during shipping;
(c)
Deviation from operating instructions, specifications or other special terms of sale;
(d)
Labor charges, loss or damage resulting from improper operation, maintenance or repairs made by
person(s) other than Seller or Seller’s authorized service station.
In no event shall Seller be liable for any claims whether arising from breach of contract or warranty or claims of
negligence or negligent manufacture in excess of the purchase price.
THIS WARRANTY IS THE SOLE WARRANTY OF SELLERS AND ANY OTHER WARRANTIES, WHETHER
EXPRESS OR IMPLIED IN LAW OR IMPLIED IN FACT, INCLUDING ANY WARRANTIES OF MERCHANTABILITY
AND FITNESS FOR PARTICULAR USE ARE HEREBY SPECIFICALLY EXCLUDED.
LIABILITY LIMITATIONS: Under no circumstances shall the Seller have any liability for liquidated damages or for
collateral, consequential or special damages or for loss of profits, or for actual losses or for loss of production or
progress of construction, whether resulting from delays in delivery or performance, breach of warranty, negligent
manufacture or otherwise.
ENVIROMENTAL AND OSHA REQUIREMENTS: At the time of shipment of the equipment from the factory, Quincy
Compressor / Ortman Fluid Power will comply with the various Federal, State and local laws and regulations
concerning occupational health and safety and pollution. However, in the installation and operation of the equipment
and other matters over which the seller has no control, the Seller assumes no responsibility for compliance with those
laws and regulations, whether by the way of indemnity, warranty or otherwise.
June 30, 2003
Summary of Contents for Air Master Series
Page 46: ......