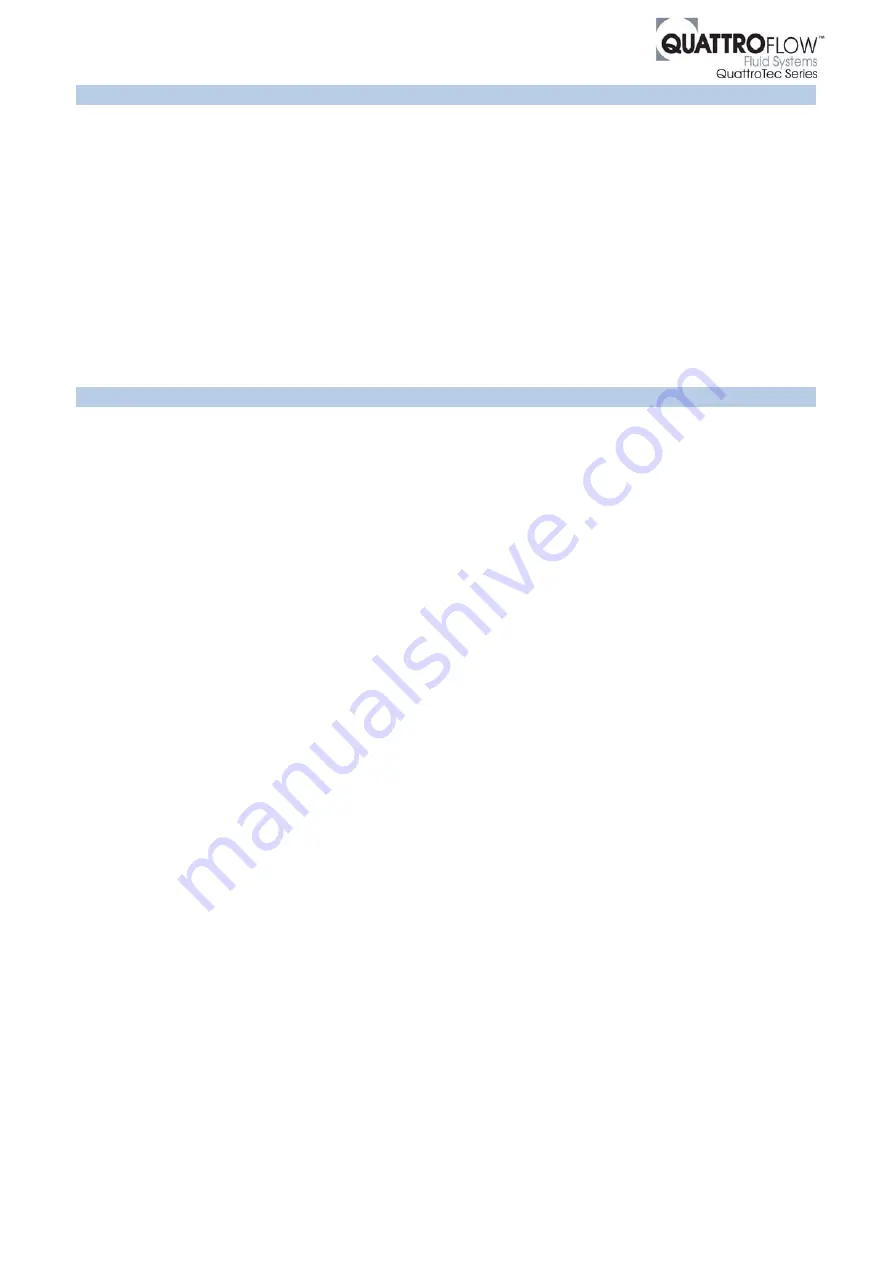
10
Cleaning
CIP
Depending
on
the
products
in
contact
with
the
pump
and
given
requirements
the
cleaning
procedure
needs
to
be
adapted
accordingly.
It
is
the
responsibility
of
the
user
to
verify
the
cleaning
efficiency.
Safety
rules
and
safety
measures
like
protective
glasses,
gloves
and
protective
clothing
have
to
be
followed
and
used
when
working
with
chemicals
like
sodium
hydroxide
(NaOH).
As
a
general
rule
we
recommend
to
clean
the
pump
according
to
the
following
procedure.
1.
Pre
rinse
the
pump
with
pure
water,
until
residual
amounts
of
product
have
been
removed.
2.
Cleaning
step
with
0.5
M
NaOH
(ca.
50°C)
at
80%
of
the
maximum
RPM
for
approximately
30
min.
Check
before,
if
surrounding
conditions
(e.g.
pipe
diameter,
system
pressure
rating)
allow
to
operate
the
pump
at
this
speed.
3.
Final
rinse
with
pure
water,
until
neutrality
has
been
achieved
(e.g.
by
measuring
conductivity
or
pH
of
the
rinse
water).
Steaming
in
place
SIP
For
steaming
in
place
the
pump
chambers
needs
to
be
installed
on
the
pump
drive.
During
the
steaming
process,
the
temperature
in
the
pump
must
not
exceed
125°C
(257°F)
and
should
not
last
longer
than
30
min.
The
cooling
of
the
pump
chamber
should
be
against
air.
Depending
on
the
SIP
conditions
it
may
be
necessary
to
shorten
the
maintenance
intervals
for
the
elastomers
significantly.
The
tightening
torques
of
the
front
bolts
of
the
pump
chamber
have
to
be
verified
after
each
SIP
cycle.
Summary of Contents for QT 10
Page 7: ...QT 30 0 psii 43 p psi 87 psi 7...
Page 17: ...17 Pump chamber incl connections QT10 C Drive unit QT10 A...
Page 20: ...20 Components QT20 Drive unit A ring drive B pump chamber C Ring drive QT20 B...
Page 21: ...21 Pump chamber incl connections QT20 C Drive unit QT20 A...
Page 24: ...24 Components QT30 Drive unit A ring drive B pump chamber C base plate D Ring drive QT30 B...
Page 25: ...25 Pump chamber incl connections QT30 C Drive unit and base plate QT30 A D...