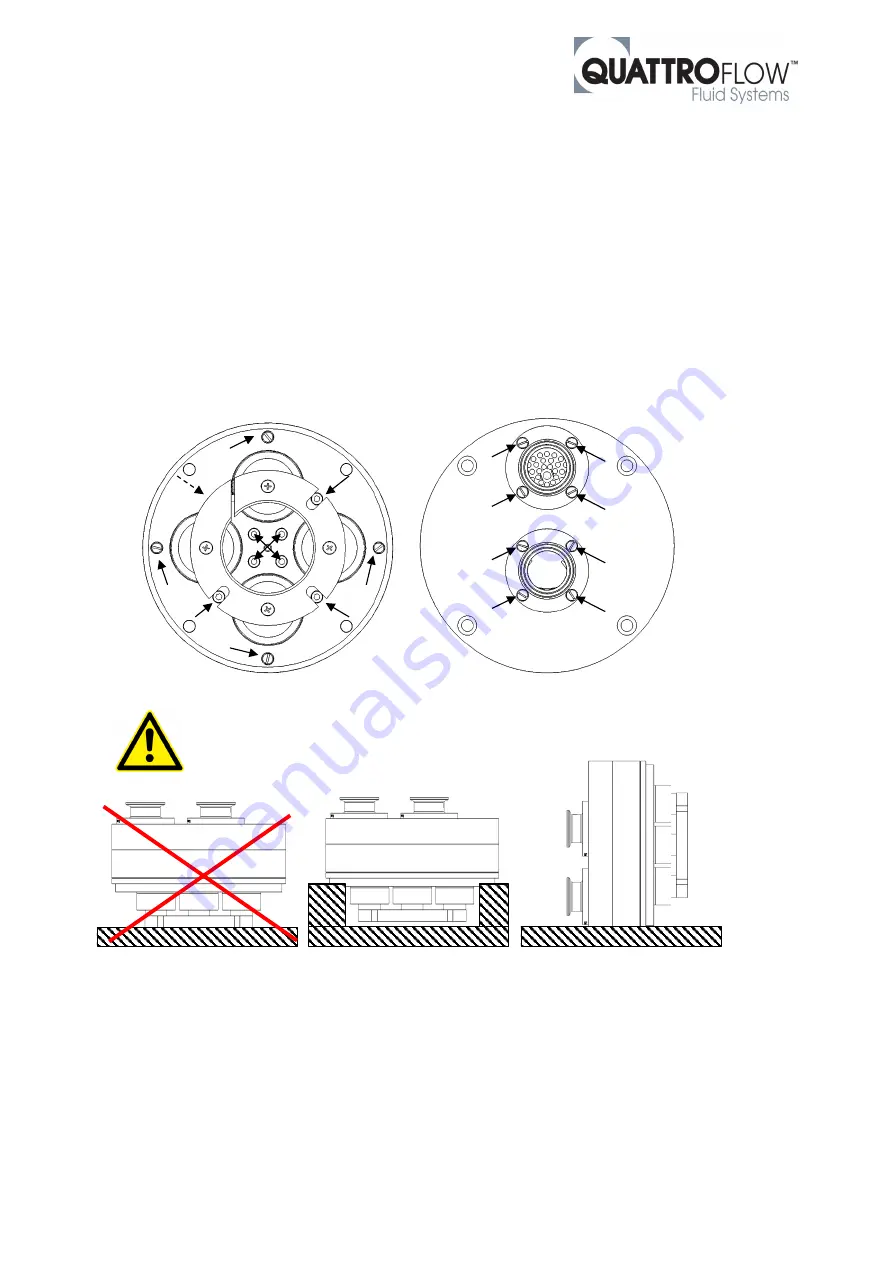
QF4400SU; edition 2018-11; page 7 of 19
2.5. Cleaning
Cleaning of the single-use pump chamber is not provided, since they are replaced after use.
2.6. Autoclave
To autoclave a non-installed pump chamber we recommend the following steps.
1. Removal of the single use pump chamber from the package.
2. Close in and outlet of the pump e.g. by connecting hoses. Ensure that a free interchange of
gas and steam over a sterile barrier (e.g. sterile filter) at in- and outlet is available.
3. Autoclaving of the prepared pump chamber in a vacuum autoclave at max. 130°C (266°F) for
max. 30 min. Follow instructions of the autoclave manufacturer.
4. After cooling down, the screws of the membrane housing cover and the connectors should be
verified and retorqued if necessary. The corresponding screws are marked and shown in the
attached picture. The screw below the clamp ring (see dashed arrow) is accessible using a
short allen key (5 mm; e.g. from Wera Tools, Code 05022045001).
Please make sure that the pump chamber is not placed on the clamp ring during the
autoclave process. The clamp ring should not be loaded during autoclaving.
2.7. Gamma Irradiation
The single use pump chamber can be gamma irradiated with a maximum dose of 50 kGy.