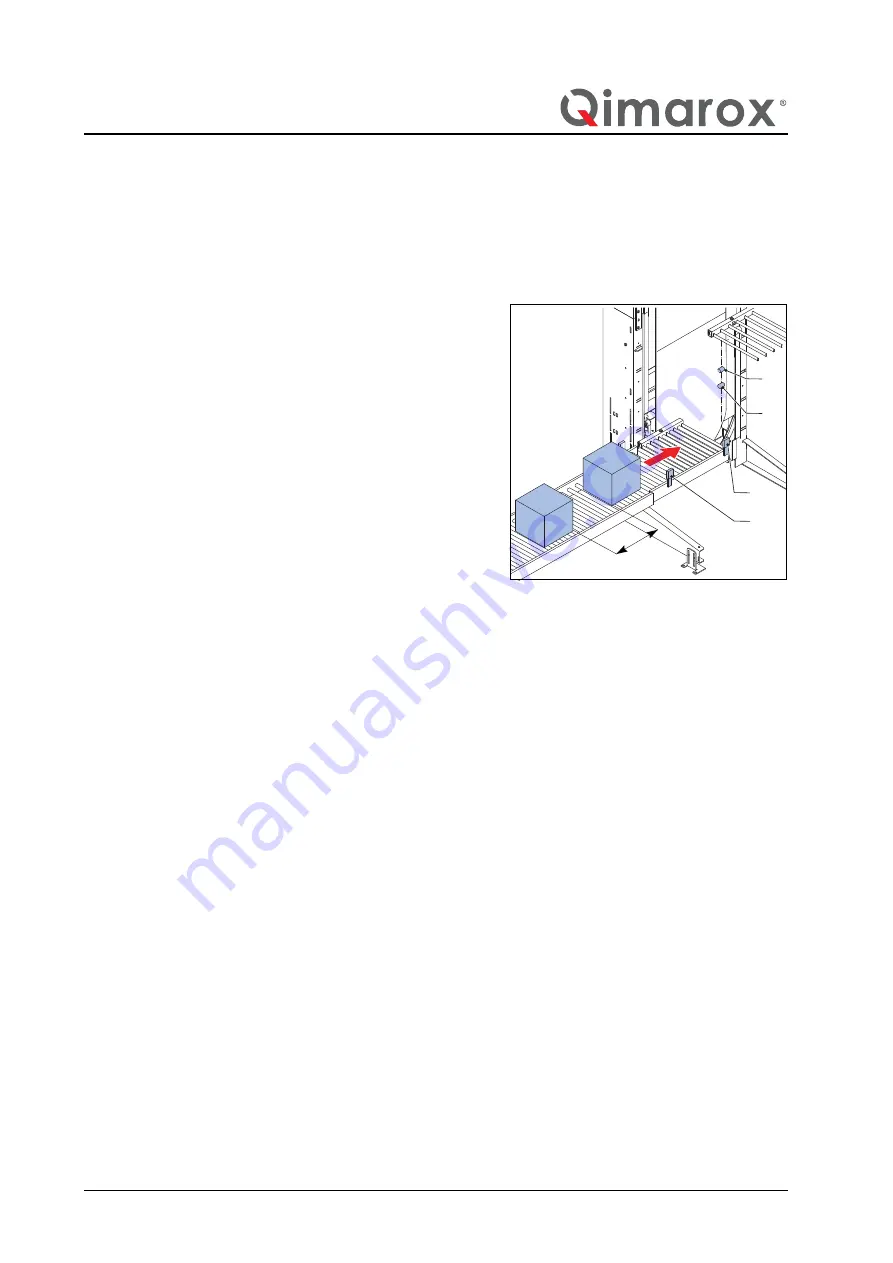
Application information
46
UM-PRORUNNER_Mk5-1.2-EN-US
Check the circulation of the product carriers
It is necessary to check the movement of the product carriers during normal operation by
means of time monitoring in the software. When the time is exceeded, the machine must
immediately stop to avoid damage.
5.4.3
Control advice
The following are important points about the
software control of the machine:
•
Make sure that the products are fed to the
machine with a time interval (X) spaced
between them. If products run into each
other, sufficient space must be created
between these products on the transition
to the infeed conveyor.
•
Make sure all the photocells and sensors
(S1, B7, B1 and B3. Refer to
) have
been adjusted correctly to the product and
the trolley. Inaccurate settings can result
in machine malfunction.
•
The product run into the machine is controlled by the starting pulse from the product
release sensor (B1). The time that the product needs to run in after the starting pulse
is to be determined by experience.
•
Make sure that this position is free from product before the product carrier passes the
putting down position. The check is started when the product carrier passes the time
frame sensor (B3). Dependent on the mutual distance and the position of this sensor,
it is necessary to build in a time frame in the software for this, allowing for virtual
determination of the position of the sensor.
•
The run time (the time the product needs to run in and out of the machine) must be
monitored by the software. If this time is exceeded, the machine must stop
immediately.
•
The continuous movement of the machine must be monitored. This can be done by
applying time monitoring to the passing of the product carriers on the product release
sensor. If this time is exceeded, the machine must stop immediately.
•
A configuration with a crossing infeed involves special control requirements and is
less suitable for high capacities.
B1
X
B3
B7
S1
Summary of Contents for PRORUNNER Mk5
Page 1: ...User Manual PRORUNNER Mk5 Version1 2 26 06 2014...
Page 12: ...About this manual 12 UM PRORUNNER_Mk5 1 2 EN US...
Page 22: ...Safety 22 UM PRORUNNER_Mk5 1 2 EN US 3 5 Safety symbols on the machine Terminal 12 Nm...
Page 38: ...Description 38 UM PRORUNNER_Mk5 1 2 EN US...
Page 58: ...Installation 58 UM PRORUNNER_Mk5 1 2 EN US...
Page 84: ...Maintenance vertical conveyor 84 UM PRORUNNER_Mk5 1 2 EN US...
Page 94: ...Maintenance belt conveyor 94 UM PRORUNNER_Mk5 1 2 EN US...
Page 98: ...Maintenance gravity roller conveyor 98 UM PRORUNNER_Mk5 1 2 EN US...
Page 108: ...Maintenance driven roller conveyor 108 UM PRORUNNER_Mk5 1 2 EN US...
Page 120: ...CE declaration of conformity 120 UM PRORUNNER_Mk5 1 2 EN US...
Page 174: ...Exploded views of product conveyors 174 UM PRORUNNER_Mk5 1 2 EN US...
Page 198: ...Electrical circuit diagrams 198 UM PRORUNNER_Mk5 1 2 EN US...
Page 200: ...Assembly instruction 200 UM PRORUNNER_Mk5 1 2 EN US...