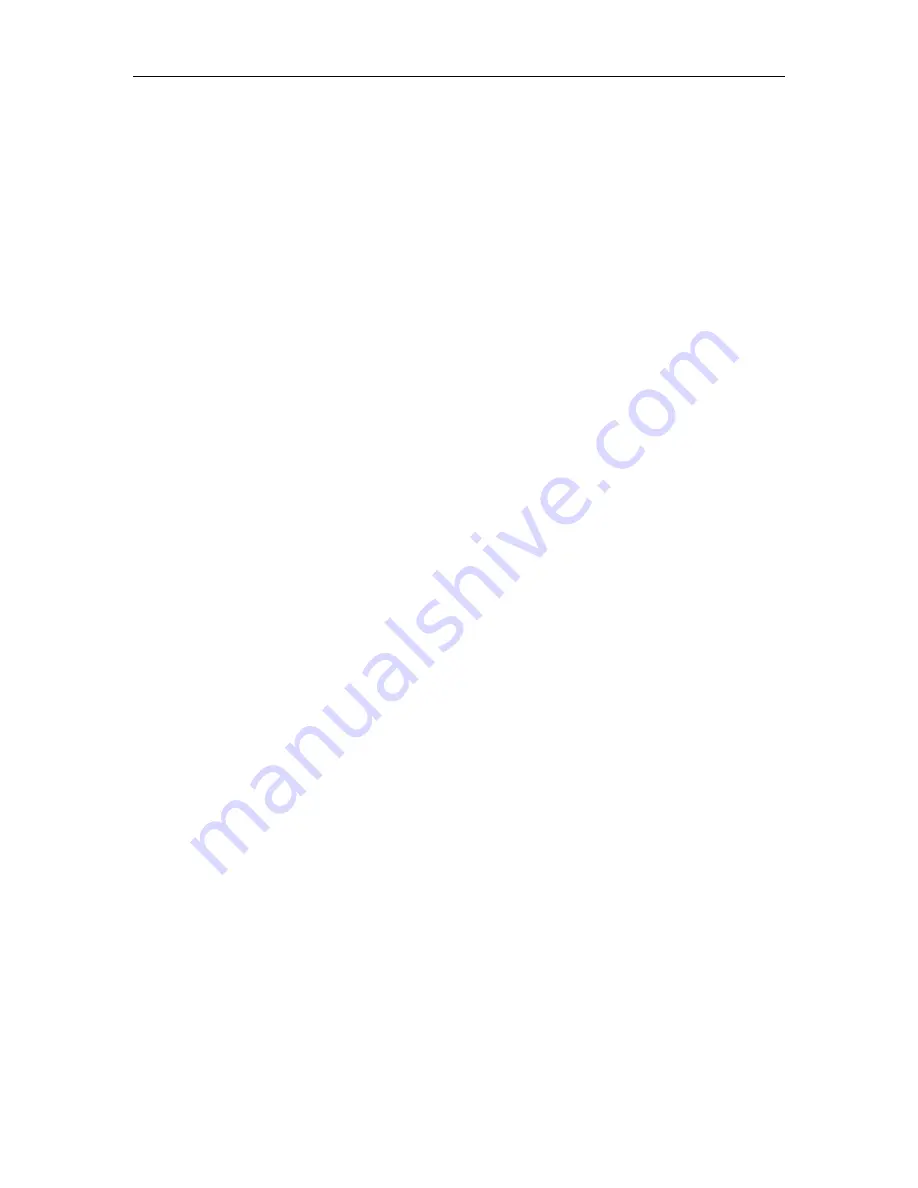
UG-1037
ePAQ-9100
16
Software Description
Copyright © 2017 QEI
(group of 8 control output points). Together, they complete a current loop that
energizes the selected relay.
The CPI includes circuitry to insure that only one output relay is energized at a
time. If more than one relay is being energized, because of component failure, a
selected row/ column detector aborts the command.
A 34 pin IDC header connector (CONTROL) is used for the connection via ribbon
cable to the control output point panels (6COP1’s).
3.3.3
Status Panel Interface (SPI)
The Status Panel Interface (SPI) provides the means for the system to sample
digital input data points. These digital points can be configured in various ways,
for example:
Individual Status Points (on/off indications)
Accumulators, where the pulse count reflects a value.
Pulse Duration Input (PDM), where the pulse width reflects a value
The SPI is capable of monitoring up to 16 individual Status Input Panels (6SIP1)
each containing 16 inputs, for a total of 256 individual digital input points. Some
communication protocols, may limit the number of input points defined as status
points to a lesser number of points.
The SPI, under program control, reads the state (0 or 1 value) of the digital points
in the selected 6SIP1 panel. This value is stored in RAM for further processing.
Via a 26pin IDC header (STATUS), 6SIP1’s can be connected to the ePAQ-9100
via ribbon cable.
3.4 Power Section
The ePAQ-9100 can operate at one of three operating voltages: 120VAC,
125VDC or 20-60 VDC. From this single input voltage, the ePAQ-9100 makes of
the internal voltages required to drive all of the logic and communications circuits.
Also, the ePAQ-9100 generates the voltage required to drive Local I/O connected
control points via the 6COP1 panels. However, the ePAQ-9100 does not
generate the required voltage to key status points on the 6SIP1 panels.
4 Software Description
The QEI ePAQ utilizes an application specific embedded real-time operating
system, ERTOS. This operating system was designed to provide a powerful,
efficient, and reliable processing platform for substation data-acquisition,
automation ERTOS provides a comprehensive set of system resources and
services that ensure proper design and operation of system components.
All interactions between components (i.e. protocols), the system hardware and
database are standardized and checked for consistency. In addition to ensuring
interoperability between components, this architecture also helps detect
improperly configured systems.
The ERTOS provides an extensive set of background operational checks on all
processes, so that run-time errors are immediately detected and handled by the
system. This approach has resulted in very high operational software reliability.
QEI has deployed thousands of systems running ERTOS over the past five