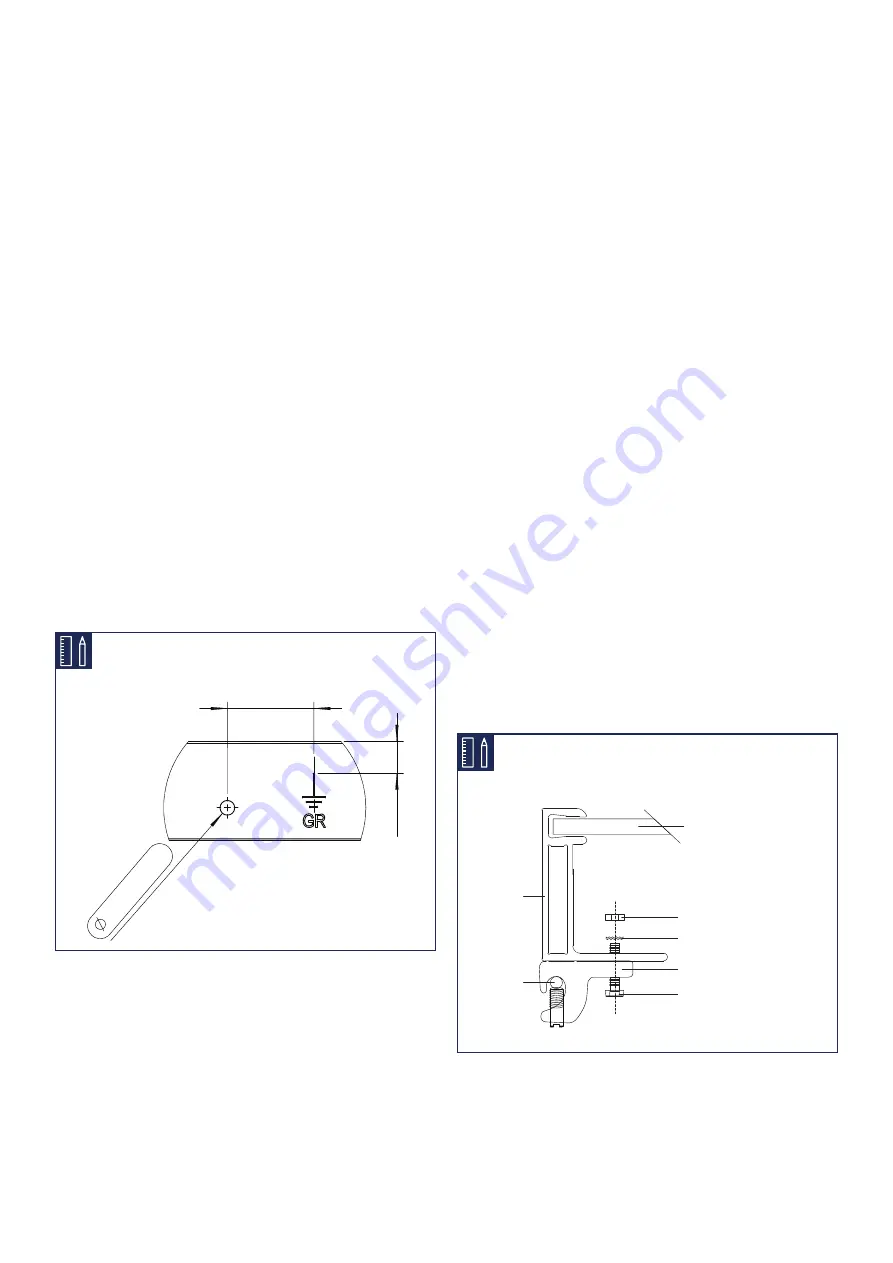
INSTALLATION AND OPERATION MANUAL SOLAR MODULES Q.PEAK DUO XL-G11S.X / BFG
23
5 Grounding
Protective Grounding
In order to prevent electrical shock or fire, the frame of the mod-
ule as well as any non-current-carrying metal parts of the system
must be grounded. While this section provides some informa-
tion about grounding the Qcells frames and modules, reference
should be made to local statutes and regulations for specific
requirements on grounding. The U.S. National Electrical Code ad-
dresses these issues in Article 250. A module with exposed con-
ductive parts is considered to be in compliance with this standard
only when it is either electrically grounded in accordance with the
manufacturer’s instructions and the requirements of the National
Electrical Code, ANSI/NFPA 70 (2014-2017), or when the bonding
means has been evaluated with this module to UL 2703.
Proper grounding is achieved by bonding all exposed non-cur-
rentcarrying metal equipment to the appropriately sized equip-
ment grounding conductor (EGC) or racking system that can be
used for integrated grounding.
Qcells frames are protected from corrosion with an anodized
coating, which has to be penetrated in order to ensure proper
bonding. The different methods listed below are suggested
methods for an appropriate bond between the frame and the
EGC or racking system (that will have to be properly grounded).
The method appropriate for any individual installation will depend
on multiple factors.
■
Dimensions shown are in inches.
0.177” (+0.008/-0)
±0.08
0.79”
0.47”
±
0.08
Option A: Use of a grounding lug
A listed grounding lug can be bonded to the frame using the
grounding holes pre-drilled in the frame. These holes are marked
with a ground symbol, as shown below on the frame section
drawing: To install the grounding lug, follow the specified instruc-
tions of the manufacturer. The grounding lug should be made of
stainless steel or tin plated metals such as aluminum to avoid cor-
rosion.
The grounding lug should be attached to the frame grounding
hole using a stainless steel screw, toothed lock washer or KEPS
nut (in order to penetrate the anodized layer) and backing nut.
Care should be taken to avoid the use of grounding hardware of
dissimilar metals, which may lead to corrosion.
Option B: Integrated grounding methods
The Qcells modules can be bonded with the racking system us-
ing UL1703 or UL2703 certified integrated grounding methods.
The racking system will then have to be grounded so that the
overall system is properly grounded. The listed racking system
and grounding device should be installed in accordance with
the manufacturers’ instructions. An example of such integrated
grounding method is the use of a WEEB clip or Schletter plate
between the module and the racking system, when mounting the
module.
The WEEB washers are generally compatible with Qcells mod-
ules, however each combination module / racking system requires
a specific WEEB washer size. Note that WEEB clips are intended
for single use only; they must not be reused after removal or
loosening. Refer to Wiley’s installation instructions for the specific
use of WEEB washers.
An example of such integrated grounding method is the use of a
washer recognized as meeting UL2703 requirements between
the module and the racking system, when mounting the module.
For example, WEEB washers are generally compatible with Qcells
modules, however each combination module / racking system
requires a specific WEEB washer size. Note that WEEB washers
are intended for single use only; they must not be reused after
removal or loosening. Refer to Wiley’s installation instructions for
the specific use of WEEB washers.
PV Laminate
Backing Nut (Stainless Steel)
Toothed Lock Washer (Stainless
Steel)
Grounding Lug (Stainless Steel
or tin-plated metal)
Equipment
Grounding
Conductor
Aluminum
Frame
Screw (Stainless Steel)