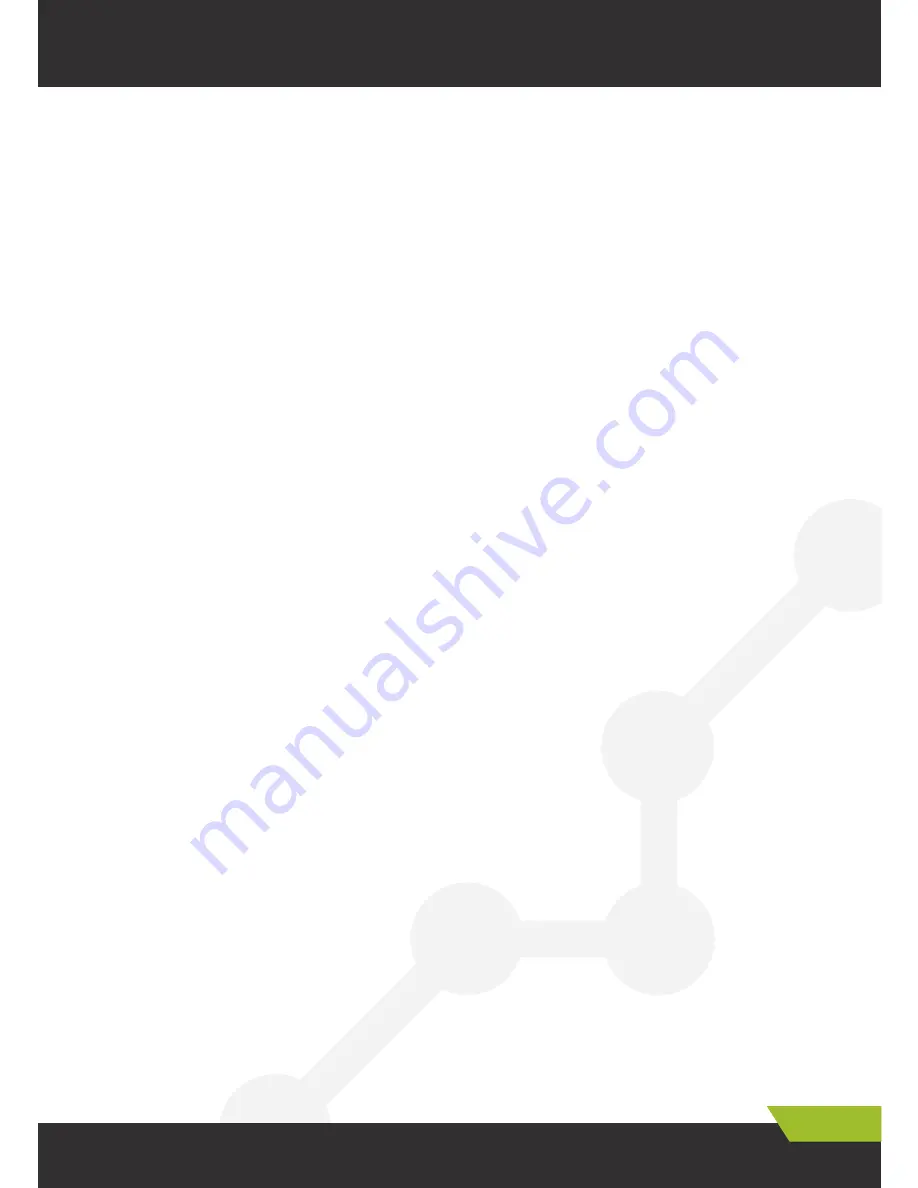
Edition of 09.11.2016
19
PLDS880. Servo-step motor DSP driver
• “Settings → Information” is description of configuration program
operation, driver parameters.
• “Settings → Language” is selection of configuration program
interface language.
Description of adjustable parameters:
• “Work_Current_Max” is maximum operating current of step motor
phases, peak current. Current is increased to this value automatically
at overloading. Range is 0.2 – 1.0 (corresponds to 2A-10A).
• “Work_Current_Min” is nominal operating current of step
motor phases specified in SM technical certificate. Range is 0.2-0.8
(corresponds to 2A-8A).
• “PI_I_Kp” is PI regulator proportional gain in step motor phase
current regulating loop. Range is 1.0-4.0. Impacts SM acceleration, LF
resonance.
• “PI_I_Ki” is PI regulator integral gain in step motor phase current
regulating loop. Range is 0.0-1.0. Impacts SM acceleration, LF
resonance.
• “PI_M_Kp” is PI regulator proportional gain in frequency multiplier
loop. Range is 0.1-4.0. Value PI_M_Kp <1 permits to smooth STEP
command impulse irregularities. Value PI_M_Kp>1 permits to react
more strongly on STEP command input impulse change.
• “PI_M_Ki” is PI regulator integral gain in frequency multiplier loop.
Range is 0.0-1.0.
• “PI_POS_Kp” is PI regulator proportional gain in position
regulating loop. Range is 0.1-4.0. The higher is PI_POS_Kp the faster
SM rotor is placed in set position.
• “PI_POS_Ki” is PI regulator integral gain in position regulating
loop. Range is 0.0-1.0. Value PI_POS_Ki >0 makes lag effect at SM rotor
placement in set position.
• “PI_SPEED_Kp” is PI regulator proportional gain in speed
regulating loop. Range is 0.1-4.0. The higher PI_SPEED_Kp value is the
higher is SM winding current reaction to STEP command speed change.
• “PI_SPEED_Ki” is PI regulator integral gain in speed regulating
loop. Range is 0.0-1.0. PI_SPEED_Ki > 0 value makes lag effect at SM
winding current reaction at STEP command speed change.
• “Elec_Damp_K” is step motor damping rate (resonance