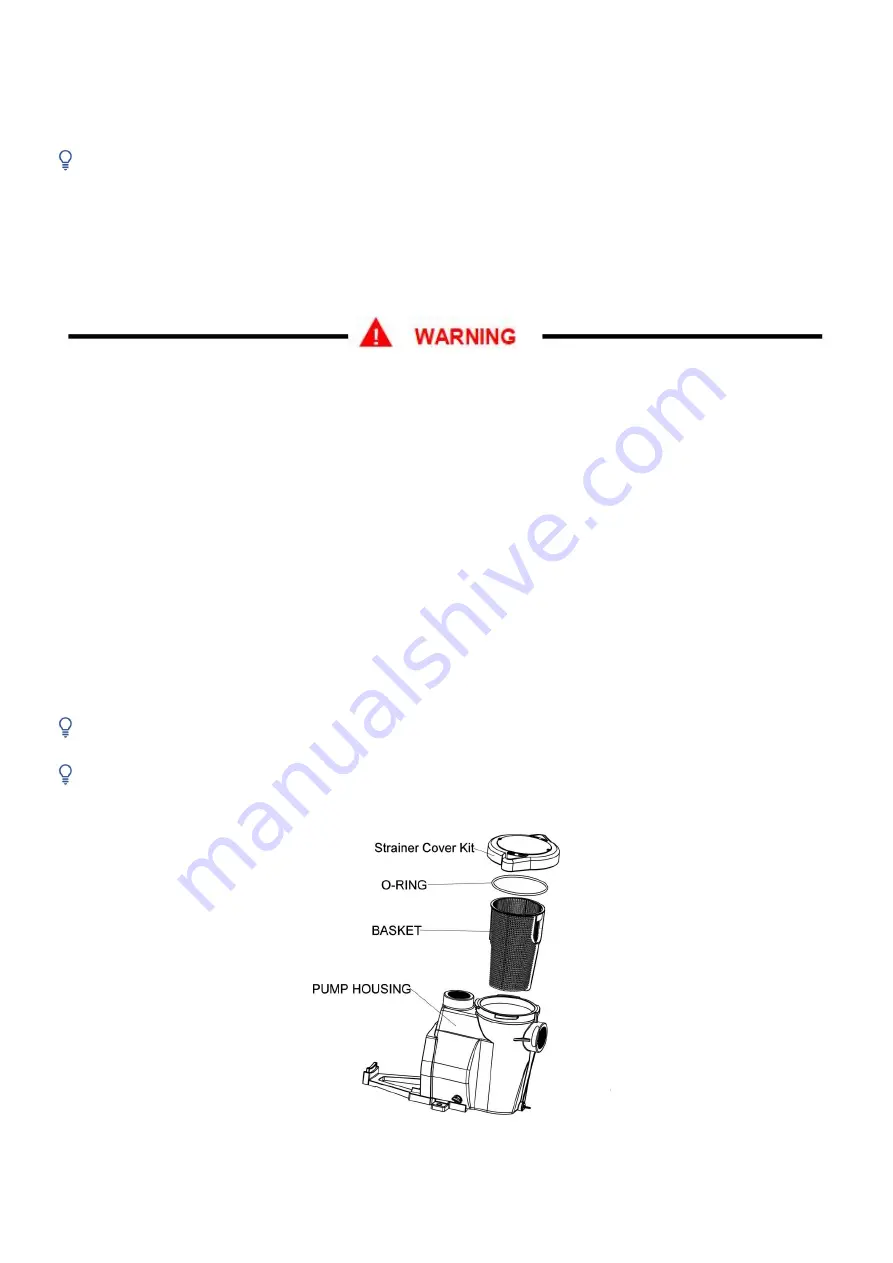
16
5.
Put the basket back into the housing. Be sure to align the notch in the bottom of the basket with the rib in the
bottom of the volute.
6.
Fill the pump pot and volute up to the inlet port with water.
7.
Clean the cover, O-ring, and sealing surface of the pump pot.
NOTICE:
It is important to keep the lid O-ring clean and well lubricated.
8.
Reinstall the lid by placing the lid on the pot. Be sure the lid O-ring is properly placed. Seat the clamp and lid on the
pump then turn clockwise until the handles are horizontal.
9.
Turn the power on at the house circuit breaker. Reset the pool time clock to the correct time, if applicable.
10.
Open the manual air relief valve on top of the filter.
11.
Stand clear of the filter. Start the pump.
12. Bleed air from the filter until a steady stream of water comes out. Close the manual air relief valve.
THIS SYSTEM OPERATES UNDER HIGH PRESSURE
. When any part of the circulating system (e.g., Lock Ring,
Pump, Filter, Valves, etc.) is serviced, air can enter the system and become pressurized. Pressurized air can cause the
lid to separate which can result in serious injury, death, or property damage. To avoid this potential hazard, follow
above instructions.
Winterizing
You are responsible for determining when freezing conditions may occur. If freezing conditions are expected, take the
following steps to reduce the risk of freeze damage.
Freeze damage is not covered under warranty.
To prevent freeze damage, follow the procedures below:
1.
Press the
Start/Stop
button to stop the pump and shut off electrical power for the pump at the circuit breaker.
2.
Drain the water out of the pump housing by removing the two thumb-twist drain plugs from the housing. Store the
plugs in the pump basket.
3.
Cover the motor to protect it from severe rain, snow and ice.
NOTICE:
Do not wrap motor with plastic or other air tight materials during winter storage. The motor may be
covered during a storm, winter storage, etc., but never when operating or expecting operation.
NOTICE:
In mild climate areas, when temporary freezing conditions may occur, run your filtering equipment all
night to prevent freezing.
Strainer Pot Assembly