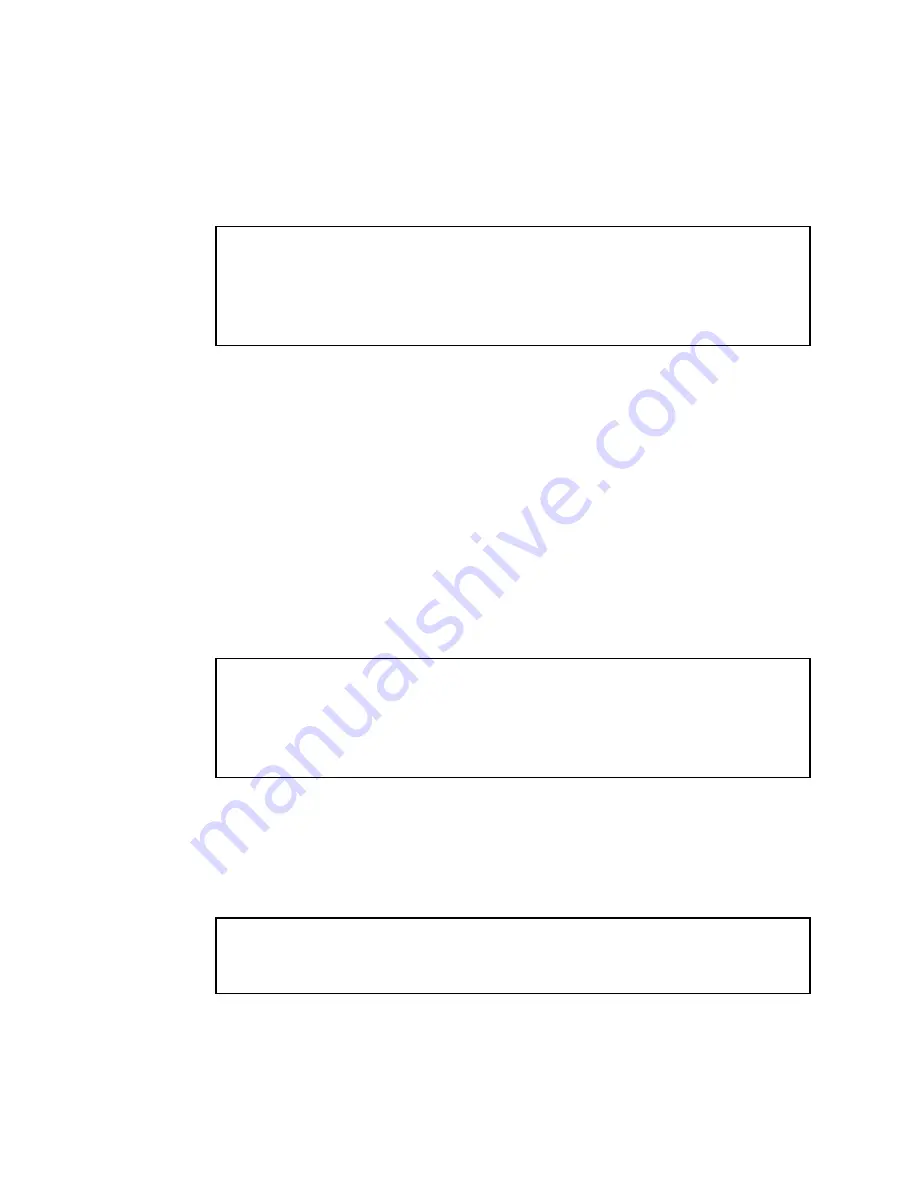
8
4.6 Air Compressor Disassembly
A.
Remove or loosen the four screws which secure the fan shroud to the motor and slide
the shroud off. Remove the four cylinder head bolts and separate them from the
cylinder bolts. Remove the air manifold tube and the cylinder head with the valve
components.
B.
Remove the two cylinder bolts at the motor and lift the cylinder off the piston.
C.
Remove the piston rings, seals and rider rings.
D.
The head gaskets may have become firmly attached to the flat surfaces of cylinder
heads or cylinders. Remove the old gasket material. Use No. 240 grit emery cloth
(or wet/dry abrasive material) to flat sand the cylinder surfaces. Follow with No. 400
grit emery cloth (or wet/dry) to dress these flat surfaces before reassembly with new
gaskets.
4.7 Air Compressor Assembly
A.
Install the new piston springs, rings and rider rings on the piston. Locate the piston
ring joints approximately opposite each other.
B.
Attach cylinder to motor with cylinder bolts and lock washer and finger tighten bolts.
Move the piston to the top dead center position and adjust the cylinder flush with the
top of the piston.
C.
Install valve components, gaskets and valve plates by lining them up as outlined in
Figure 6. Valves are pre-lined in the maintenance kit; however, they should be
checked. The leaves of the intake and discharge valves have been pre-bent and do not
require adjusting.
D.
Install the head assembly using the four heat bolts and finger tighten.
NOTE:
Clean all components with a non-flammable, non-toxic cleaning solvent.
DO NOT FLOOD THE PISTON WRIST PIN, OR CONNECTING ROD
MAIN BEARING WITH SOLVENT OR THE PERMANENT
LUBRICANT WILL BE WASHED AWAY.
NOTE:
Top dead center can be checked by using a straight edge across the
cylinder head and then moving the piston flush with the straight edge.
Move the piston up and down to insure there is no binding in the cylinder
and tighten the cylinder bolts.
NOTE:
The ends of the two fins on the cylinder head have been omitted.
They are always on the exhaust port.