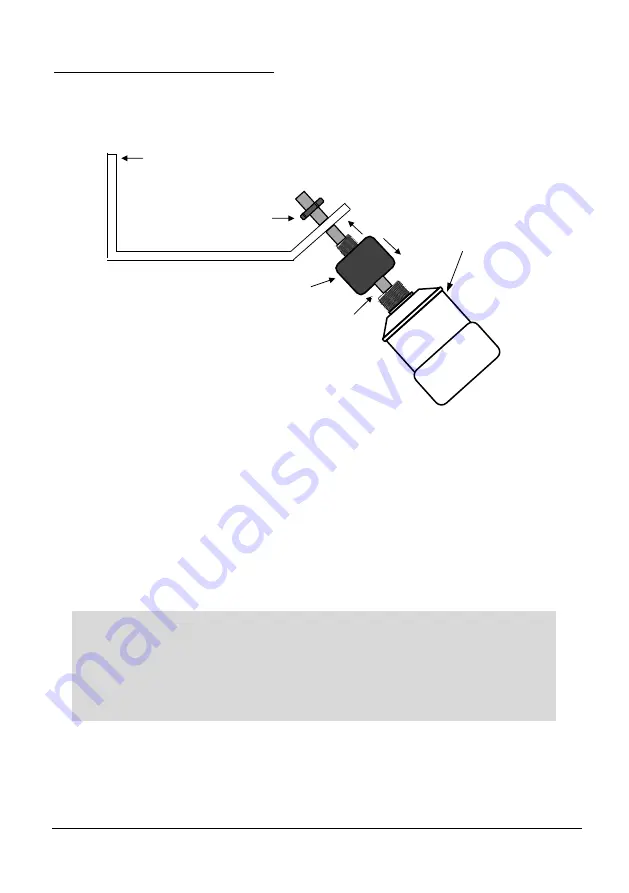
Page 15
Mounting sensor to a bracket
Mounting the sensor to the 45° angled bracket is done via an adapter and M20 nut, as
shown in Fig.3:
For correct installation, we recommend that the adapter is threaded on the cable, and
carefully screwed onto the
MicroFlow-i
before fitting to the bracket. This will reduce
the risk of any ’twisting’ in the cable.
Ensure that the sensor is tightened and the dot is in the correct position.
Important Information
When fixing the sensor to the adapter, ensure that care is taken when
pulling the sensor cable through. And once attached to the adapter, and
the M20 nut is tightened, the green dot should be central to the
movement of flow as shown in Fig.4.
Bracket
Adapter
Fig.3
Cable
M20 Nut
Green dot to be
displayed on top
Summary of Contents for MicroFlow-i
Page 1: ...MICROFLOW INSTRUCTION MANUAL...
Page 2: ......
Page 4: ......
Page 6: ......
Page 12: ...Page 6 EU Declaration of Conformity...
Page 27: ...Page 21 Diagram 4 Diagram 3 Distance Distance Distance Distance Distance...
Page 32: ...Page 26 This page is left blank intentionally...
Page 34: ...Page 28 This page is left blank intentionally...