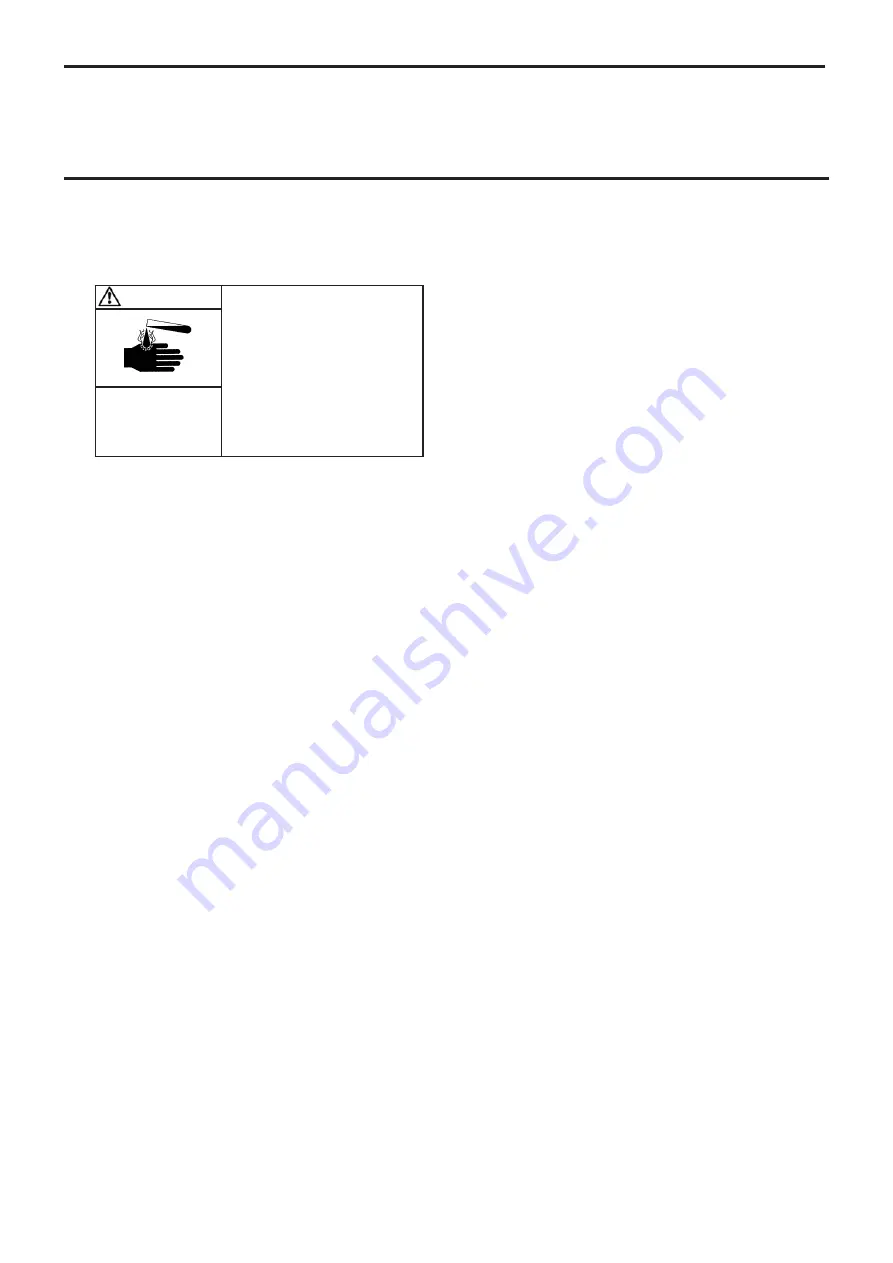
25/28
NT 1004-C00 03 18 SLC12 i - SLC18 i - SLC12 i HT - SLC18 i HT e
If necessary, refer to § MAINTENANCE for pump disassembly.
13.1 Short duration (≤ 1 month)
MOUVEX pumps and motor-driven pumps are well lubri-
cated when delivered to protect the internal parts during
brief storage in a building where :
• the temperature remains between 10°C and 50°C.
• the relative humidity does not exceed 60%.
• exposure to vibration is limited.
• pump is stored in an area sheltered from bad wea-
ther and sun.
13.2 Long duration (> 1 month)
The recommendations from the manufacturer should be
followed if the pump is stored with its gear motor.
Pump ports should be filled with a non-corrosive liquid
that it compatible with the pump components in order to
prevent corrosion.
Unpainted external surfaces of the pump (e.g. shafts,
couplings, etc.) should be covered in some form of anti-
corrosion protection.
If storage was made after a period of operation, the
transmission oil must be replaced before storage (see §
DRAINING).
The transmission will be filled with oil at breather level
(see § DRAINING).
If pump storage lasted more than one year, the oil
should be replaced in time to prevent an excessive
degradation of its qualities.
The best storage conditions are inside a building that
meets the conditions set out above.
If inside storage is not possible, the materials should be
covered to prevent direct exposure to sun and bad wea-
ther. This protection should also prevent condensation.
The pump should be turned a few revolutions manually
every two months.
13.3 Restarting
Follow the standard start-up procedure for the pump/
motor-driven pump, as well as the instructions below.
Turn the pump by hand to make sure the parts move
freely.
If the storage duration has exceeded one year, replace
the oil transmission (see § DRAINING for removal ins-
tructions).
If the pump has a safety bypass, remove it and inspect
the parts and make sure they move freely.
In all cases, the oil should be replaced after more than
two years after its commissioning.
WARNING
IF PUMPING HAZARDOUS OR TOXIC
FLUIDS, THE SYSTEM MUST BE FLUSHED
PRIOR TO PERFORMING ANY SERVICE
OPERATION.
Toxic or hazardous
fluids can cause
serious injury.
13. STORAGE
12. OPTIONS
12.1 Bellows monitoring system
See Instructions 1011-S00.