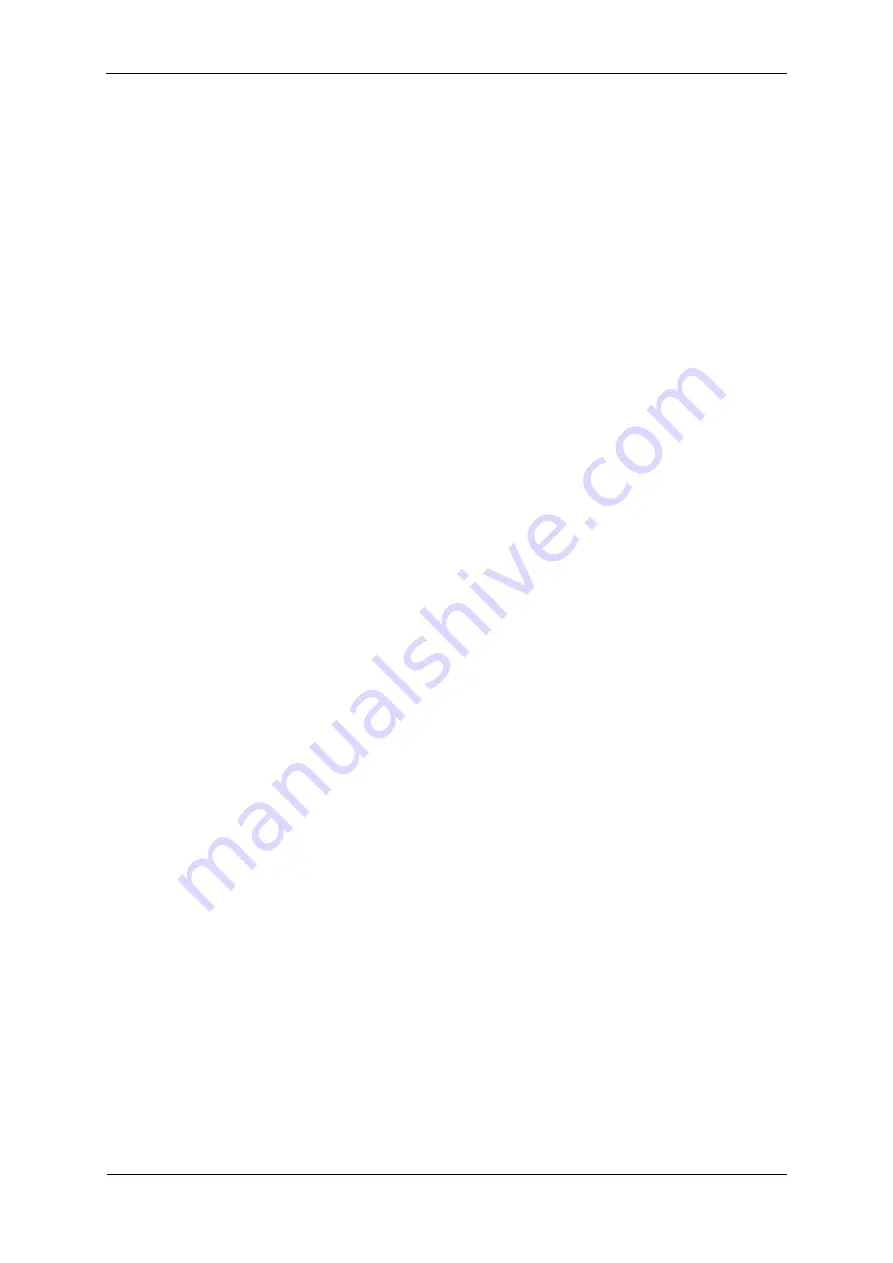
COMPACT 2 NDT
User Manual
5190-0-0002
PROTEC GmbH & Co. KG, In den Dorfwiesen 14, 71720 Oberstenfeld, Germany
30 von 65
5.3.2
Installation
1
Insert lower dryer part. Make sure that both slides at the lower part are assembled and pushed
down.
2
Put in the upper dryer part. Insert the lower edge of the upper part carefully into the middle
guidance of the lower part.
3
Check if side plates and gears of upper and lower part fit together correctly.
4
The dryer plate small (2) can now be assembled into the guidance. For this lift dryer plate large
(5) a bit, so that the small plate can be pushed in, completely.
5
Now push both black slides (1) up until the clips click into place.
5.4
Problems and Solutions
5.4.1
Advice on Film Defects
Your processor has been constructed for long term use. If however irregularities might occur, you will
find help to locate the problem below. Please check the listed points, before calling your service-
technician.
5.4.1.1
Films do not have enough density
•
Bath temperature is too low
•
Developing time too short
•
Exposure time is too short
•
Replenishment rate of developer too low
•
Developer chemicals are exhausted or too strong diluted: Renew
•
Fixer solution has been mixed into developer: Renew. Clean and rinse bath well before refilling
•
Circulation is broken down
5.4.1.2
Too high a density
•
Bath temperature too high
•
Developing time too long
•
Exposure time is too long
•
Replenishment rate of developer too high
•
Developer chemicals are too high diluted: Renew
•
After renewing chemicals: Starter is missing
•
Circulation is broken down
5.4.1.3
Films will not dry
•
If warm air comes out of the air channel in the dryer, chemicals and film type should be
checked
•
Fixer solution is exhausted or diluted
5.4.1.4
Film has a yellow-green surface
•
Not fixed correctly. Check the film type and fixer chemistry
•
Fixer solution is exhausted or diluted. Replenishment rate of fixer is too low
5.4.1.5
Scratches, pressure marks, dirt on film
•
Prior to processing films, run cleaner films through the processor
•
Pressure marks caused by careless handling, finger nails etc.
•
Rollers are polluted. Clean tanks and roller racks
5.4.1.6
Cloudy film
•
Level in developer is too low
•
First guide bar of fixer rack is dirty (condensate or crystals). Clean roller racks
•
Developer is old or circulation not working
•
Try processing films by infeeding them with emulsion side up