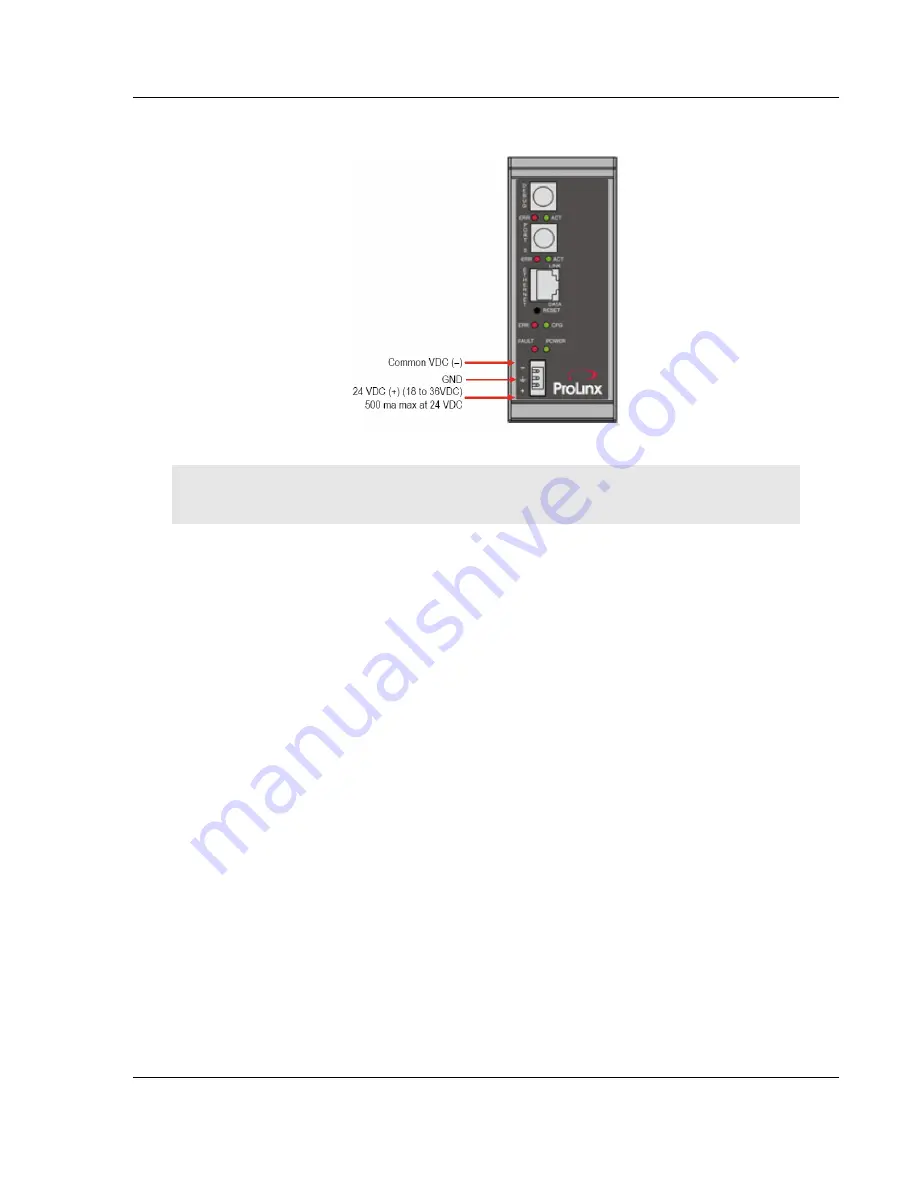
ProLinx-HART ♦ ProLinx Gateway
Start Here
HART Master with Analog I/O
Driver Manual
ProSoft Technology, Inc.
Page 13 of 104
October 13, 2011
1.4
Connecting Power to the Unit
WARNING:
Ensure that you do not reverse polarity when applying power to the
module. This will cause damage to the module’s power supply.