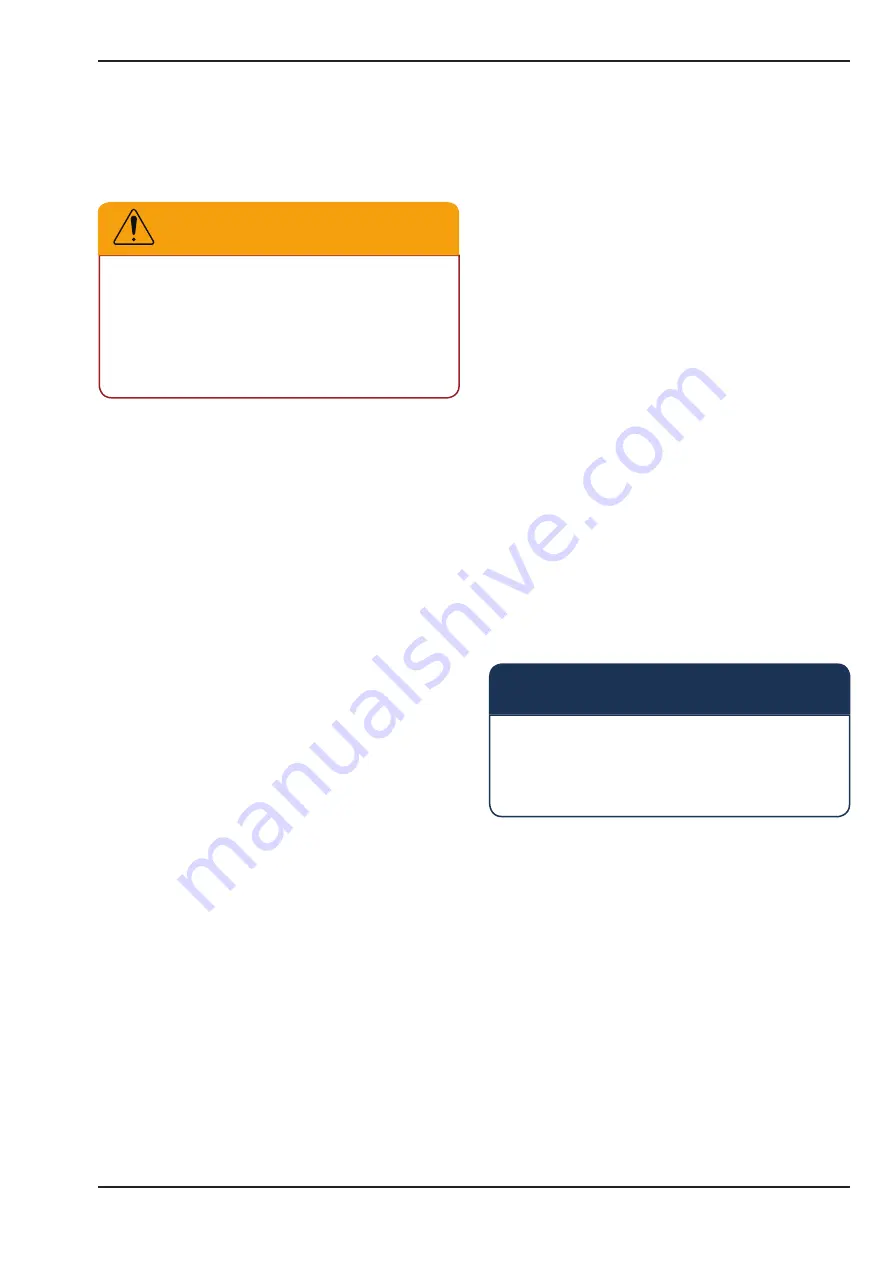
Section 6
6.11
PRONAR T700M/1
Maintenance
6.5 MAINTENANCE OF ELECTRICAL SYSTEM AND WARNING
ELEMENTS
Work connected with the repair, change
or regeneration of electrical system com-
ponents should be entrusted to specialist
establishments, having the appropriate
technology and qualifications for this type
of work.
The duties of the user include only tech-
nical inspection of electrical system and
reflectors.
PROCEDURE
• Connect trailer to tractor with appro-
priate connection lead.
• Check if the connection lead is re-
liable. Check connection sockets in
tractor and trailer.
• Check completeness and technical
condition of trailer lights.
•
Check completeness of all reflectors.
• Check correct mounting of the slow-
moving vehicle warning sign holder.
• Before driving on to public road,
check that the tractor is equipped
with a warning reflective triangle.
J.3.2.589.05.1.EN
TIP
Light-emitting diodes (LED) are used as the source
of light. Damaged lights can be replaced only as
complete units. It is impossible to repair or regener-
ate them.
Do NOT travel with out of order lighting system.
Damaged lamp lenses must be replaced immediate-
ly before travelling. Lost or damaged reflectors must
be replaced.
Before driving off, make certain that all lamps and
reflectors are clean.
IMPORTANT
Summary of Contents for T700M/1
Page 2: ......
Page 3: ...INTRODUCTION ...
Page 10: ...Introduction 8 PRONAR T700M 1 ...
Page 11: ......
Page 12: ......
Page 15: ...BASIC INFORMATION SECTION 1 ...
Page 30: ...Section 1 Basic information 1 16 PRONAR T700M 1 ...
Page 31: ...SAFETY ADVICE SECTION 2 ...
Page 48: ...Section 2 Safety advice 2 18 PRONAR T700M 1 ...
Page 49: ...DESIGN AND OPERATION SECTION 3 ...
Page 75: ...CORRECT USE SECTION 4 ...
Page 110: ...Section 4 Correct use 4 36 PRONAR T700M 1 ...
Page 111: ...TECHNICAL INSPECTION SCHEDULE SECTION 5 ...
Page 145: ...MAINTENANCE SECTION 6 ...
Page 161: ...TYRE SYSTEM SECTION 7 ...
Page 164: ...ANNEX A A 2 PRONAR T700M 1 ...
Page 165: ......
Page 166: ......