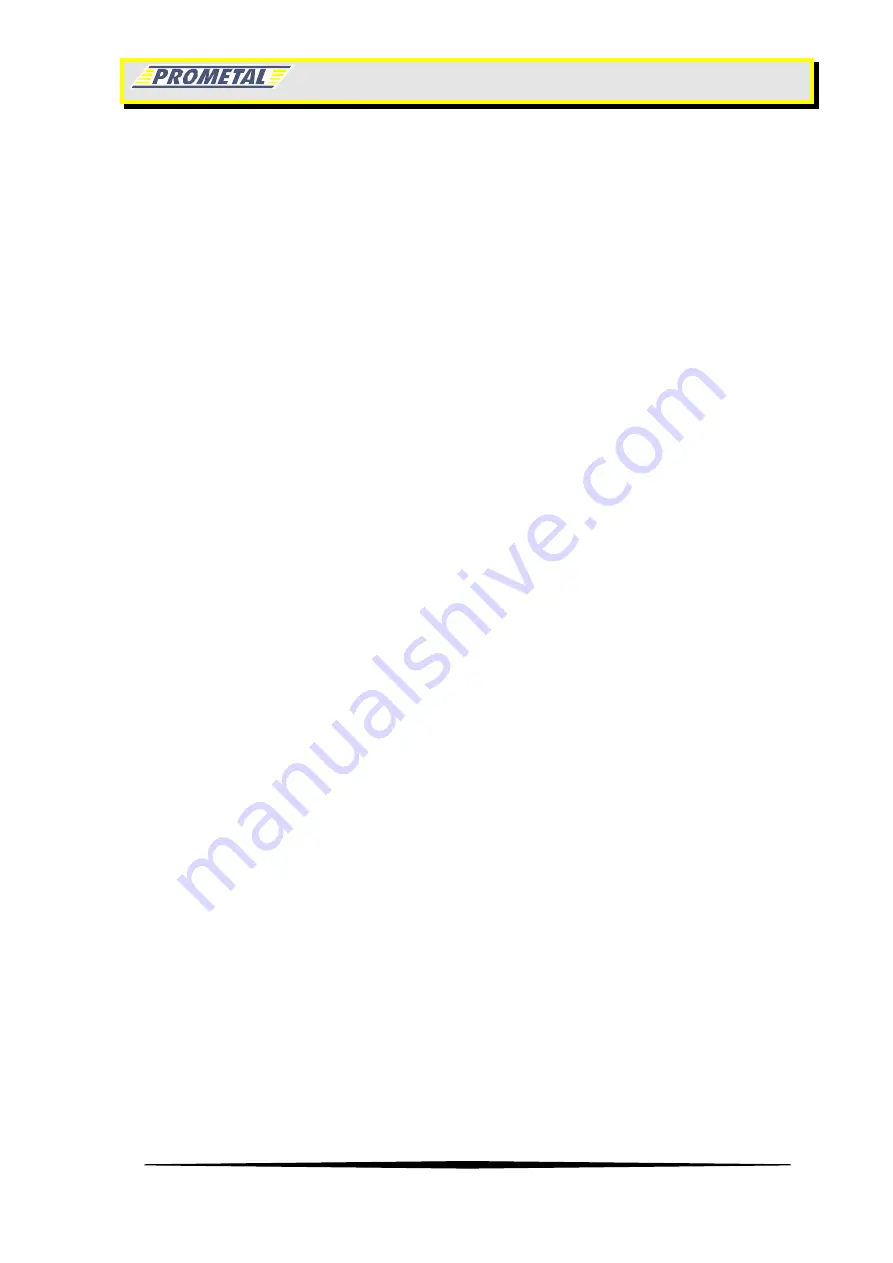
Maintenance manual Universal-1000
P R O M E T A L
15
Maintenance
-Cleaning-
Cleaning at the end of production is essential prerequisite for proper functioning of the
machine.
It is appropriate to start with filler boxes and hoppers by knocking off residual concrete. After
this, open hopper outlets to enable the loose concrete to drop into filler boxes with which the
concrete is moved into mould and removed from the machine together with the pallet.
Tamper head brushes are likewise to be cleaned.
Special care needs to be taken when cleaning mould. Especially if mould is of complex design
(e.g. hollow block mould), which is more difficult, but also more important. Old solid
concrete on the tamper head and mould, and above all on the tamper head plates, on the
bottom of the mould and between the webs promotes wear and the finished products are then
often no longer true to size and shape. Blowing out with compressed air has proven to be and
effective means of general cleaning. Then loose concrete falls into machines pit, from where
it is easy to be removed.
Rubber buffers, rubber profile strips, rubber discs and bronze parts should not be allowed to
come into contact with oil, grease or other media which have an adverse effect on them, as
this would shorten service life.
-Lubrication-
The number of lubrication points on the machine has been kept to the minimum. Types of
lubricants to be used are given in our lubricant table. The points concerned are listed in a
separate lubrication chart outlining the lubrication intervals.
-Servicing-
By its very nature, a heavy-duty vibration machine is subject to considerable loading and
there is bound to be component wear. Design measures and the use of appropriate materials
help to offset this factor. It is then up to customers to do the same by keeping the machine in
good condition and performing systematic service work. The information given in the
following is designed to provide assistance with the above. It is important to have good
cooperation between the machine operators and the maintenance staff (mechanics and
electricians). A brief production stoppage to tighten a loose screw is better and cheaper than
waiting until the screw drops out and causes major damage.
-Vibration unit-
Check tightness of all screws on vibration unit as these are subject to particularly severe
stress. Renew damaged rubber buffers. The scraper plates bolted to the vibration table needs
to be renewed if severely worn. Renew damaged rubber universal joints at articulated shafts.
The brake shoes of the vibrator brakes must move freely to enable them to lift rapidly off the
brake disc after braking. Renew worn brake pads in good time, so as to prevent subsequent
damage to braking discs/motors. Renew worn brake discs. To check the vibrator bearings, the
Summary of Contents for UNIVERSAL 1000
Page 19: ...Maintenance manual Universal 1000 P R O M E T A L 19 ...
Page 25: ...Maintenance manual Universal 1000 P R O M E T A L 25 Hydraulic system ...
Page 26: ...Maintenance manual Universal 1000 P R O M E T A L 26 ...
Page 52: ...Maintenance manual Universal 1000 P R O M E T A L 52 Now lower down tamper head and mould ...
Page 53: ...Maintenance manual Universal 1000 P R O M E T A L 53 Pull out cart with mould on itself ...
Page 58: ...Maintenance manual Universal 1000 P R O M E T A L 58 After adjustment is done ...
Page 65: ...Maintenance manual Universal 1000 P R O M E T A L 65 Vibrator table maintenance ...