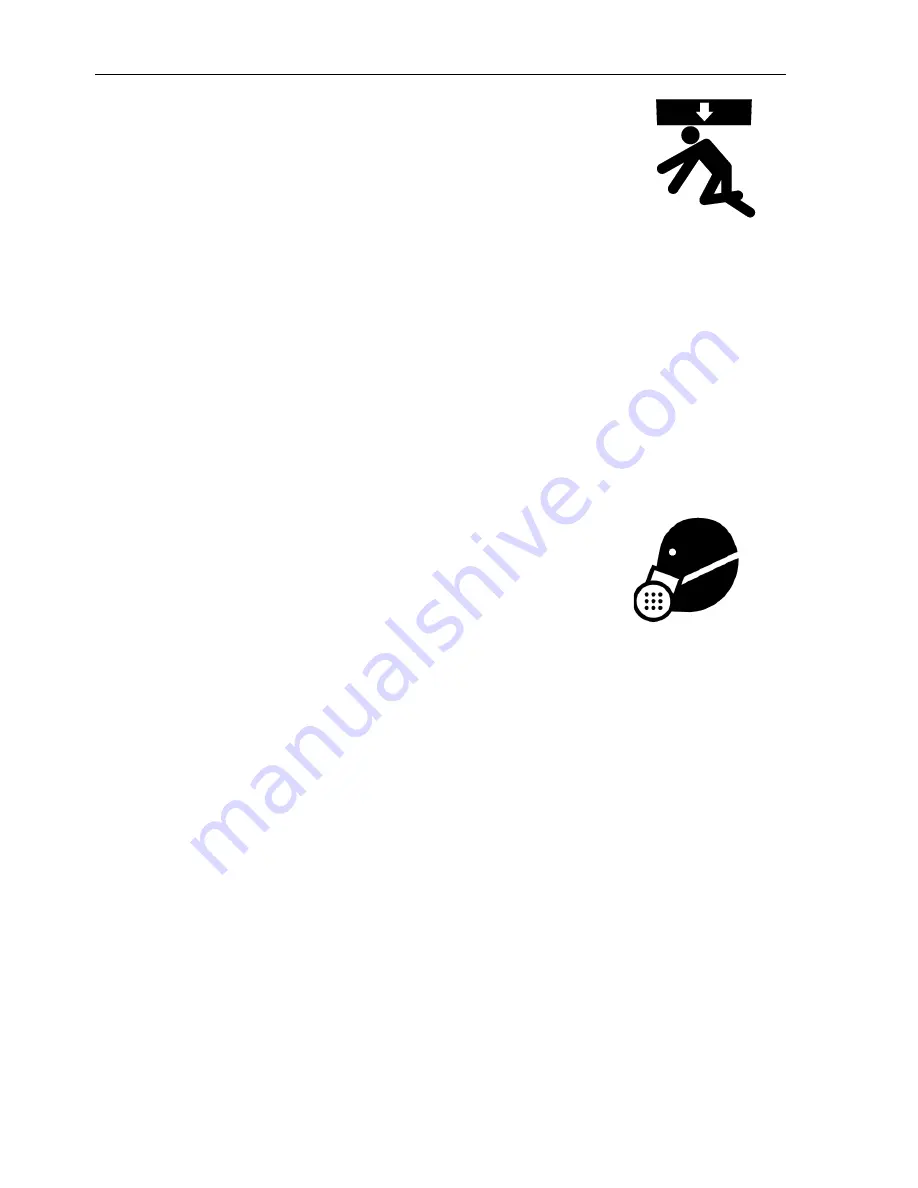
TD92
Operator’s Manual
12
•
Never perform service on a machine that is supported solely by a
jack. Always ensure proper blocking is placed to support load
during service.
Do not support the machine on cinder blocks,
hollow tiles or other members that may fail under continuous
load.
WELDING AND GRINDING WORK PRECAUTIONS
IMPORTANT! A fire extinguisher should be easily accessible during
all welding work.
Welding repairs are to be performed by a trained welder with proper
service instructions. Know the material to be welded and select the
correct welding procedure and materials (electrodes, rods, wire) that will
provide a weld metal strength equivalent to the parent material.
Move the machine to a clean, safe area before welding, grinding or using
a cutting torch on it. This type of work should only be done in a clean
area and not in places that contain combustible liquids, such as fuel
tanks, hydraulic pipes or similar.
Connect arc welder ground as close as possible to work area.
Work with extra care when welding, grinding or torch cutting near
flammable objects.
WORKING ON PAINTED SURFACES
Heated paint gives off poisonous gases. Therefore, paint must be
removed from an area with a radius of at least 4 in (10 cm) before
carrying out welding, grinding, or gas cutting. In addition to the health
hazard, the weld will be of inferior quality and strength if the paint is not
removed.
Methods and precautionary measures when removing paint:
Blasting
– use respiratory protective equipment and protective
goggles.
Paint remover or other chemicals
– use a portable air extractor,
respiratory protective equipment, and protective gloves.
Grinding
– use a portable air extractor, respiratory protective
equipment, and protective gloves and goggles.
WORKING ON GALVANIZED / PLATED SURFACES
Only qualified welders should attempt a weld repair on galvanized or
plated components. Proper pre-welding surface preparation is required.
Always ensure proper ventilation, wear proper respiratory protective
equipment and avoid direct contact with smoke emitted from welding
process.
Summary of Contents for TD 92
Page 2: ......
Page 48: ......
Page 52: ...TD92G Parts Manual ...
Page 54: ...TD92G Parts Manual 2 1 DECK ASSEMBLY 1 1 Blade Spindle Assembly 8 2020 ...
Page 55: ...TD92G Parts Manual 3 1 2 Blade Options ...
Page 56: ...TD92G Parts Manual 4 1 3 Gearbox Assembly ...
Page 57: ...TD92G Parts Manual 5 1 4 Wing Deck Assembly 8 8 2017 ...
Page 58: ...TD92G Parts Manual 6 1 5 Rear Deck Assembly ...
Page 59: ...TD92G Parts Manual 7 2 FRAME ASSEMBLY 2 1 Frame Assembly ...
Page 60: ...TD92G Parts Manual 8 2 2 Wing Lift Assembly ...
Page 61: ...TD92G Parts Manual 9 2 3 Tire Assemblies ...
Page 62: ...TD92G Parts Manual 10 2 4 Spare Tire Carrier Optional ...
Page 63: ...TD92G Parts Manual 11 3 HYDRAULICS 3 1 Hydraulics ...
Page 64: ...TD92G Parts Manual 12 3 2 Hydraulic Stabilizer Valves Optional ...
Page 65: ...TD92G Parts Manual 13 4 DRIVELINE 4 1 Driveline 9 2016 ...
Page 66: ...TD92G Parts Manual 14 4 2 Input PTO Shaft ...
Page 67: ...TD92G Parts Manual 15 4 3 Intermediate PTO Shaft ...
Page 68: ...TD92G Parts Manual 16 4 4 Deck PTO Shaft ...
Page 69: ...TD92G Parts Manual 17 4 5 Deck Gearbox ...