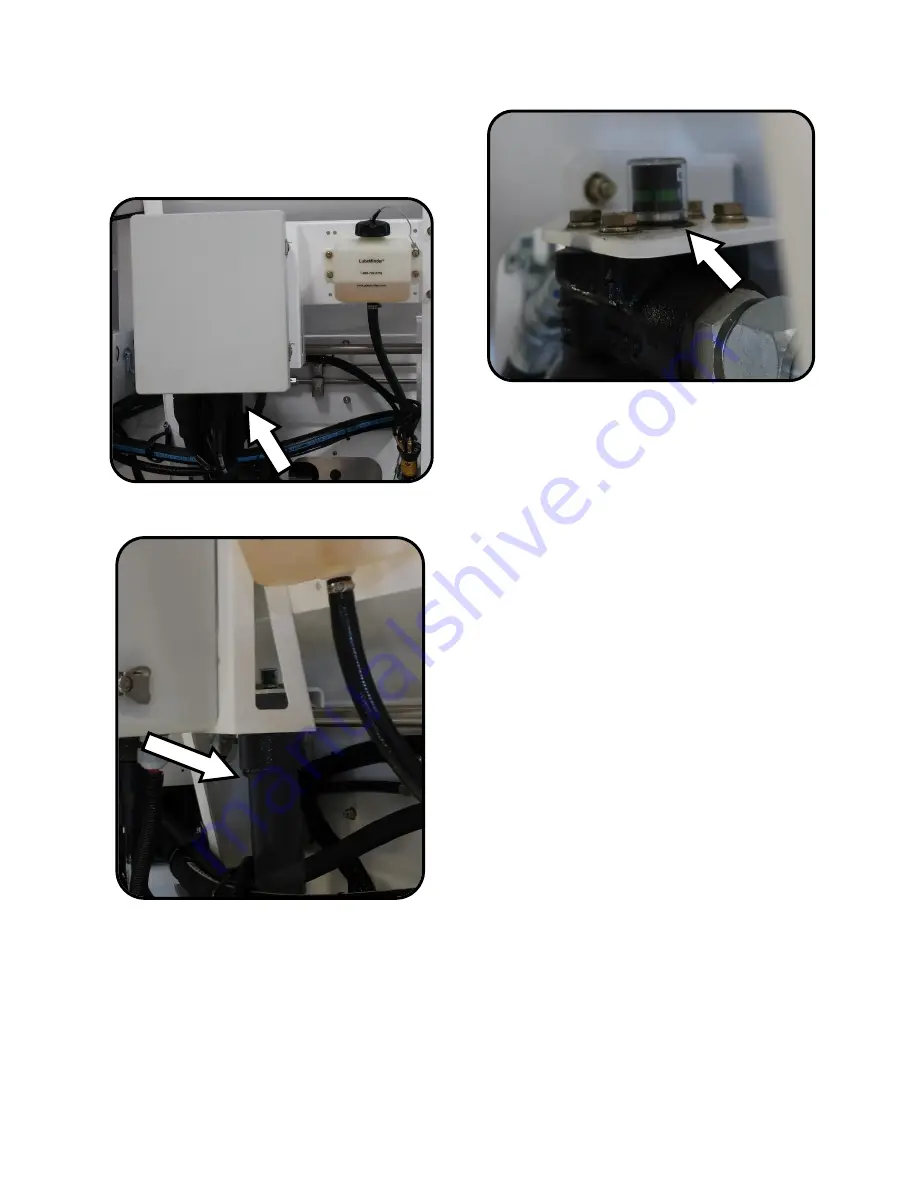
MX05001
7-2
Rev.
1
3 March 2022
Hydraulic Oil Filter
The high-pressure hydraulic oil filter is included
with the machine for the conveyor belt.
Figure 22. General location. Located behind distribution
box
Figure 23. High Pressure hydraulic oil filter
The filters are equipped with indicator showing
the status of the filter. Green indicates the filter
is working properly. Red indicates flow through
the filter is restricted requiring maintenance.
Figure 24. High pressure filter indicator.
Wear Plates
The mix auger is equipped with replaceable wear
plates, designed to protect the auger from
premature wear. The wear plates must be
inspected frequently and replaced when they
wear down to the auger flighting.
IMPORTANT:
Never allow the plates to wear into
the mounting holes drilled into the flighting. The
complete auger or portion of it will have to be
replaced if this occurs.
Inspect the wear plates during clean up and
monitor their condition. Also, be aware of the
nature of upcoming pours, this will help prevent
a wear plate failure part way through a large,
remote pour.
Remove the old wear plates by cutting the nuts
off with a chisel or cutting torch, being careful
not to damage the auger flighting. When using a
torch, be careful not to scorch the rubber
portions of the auger trough.
IMPORTANT:
When attaching the new wear
plates, it is important that they are against a
firm, even surface at the bolting area. Excessive
pressure on an uneven surface may cause
breakage.
Summary of Contents for G Series
Page 1: ...ProAll Mobile Mixer Operator s Manual G Model MX05001 3 March 2022 Rev 1 ...
Page 6: ......
Page 10: ......
Page 12: ...MX05001 2 2 Rev 1 3 March 2022 Decal 1 Decal 2 Decal 3 1 2 1 3 4 4 6 ...
Page 13: ...MX05001 2 3 Rev 1 3 March 2022 Decal 4 Decal 5 Decal 6 Decal 7 Decal 8 ...
Page 28: ......
Page 42: ......
Page 47: ...MX05001 7 5 Rev 1 3 March 2022 2 13 14 10 8 7 6 9 11 12 15 5 4 ...
Page 54: ......
Page 56: ......