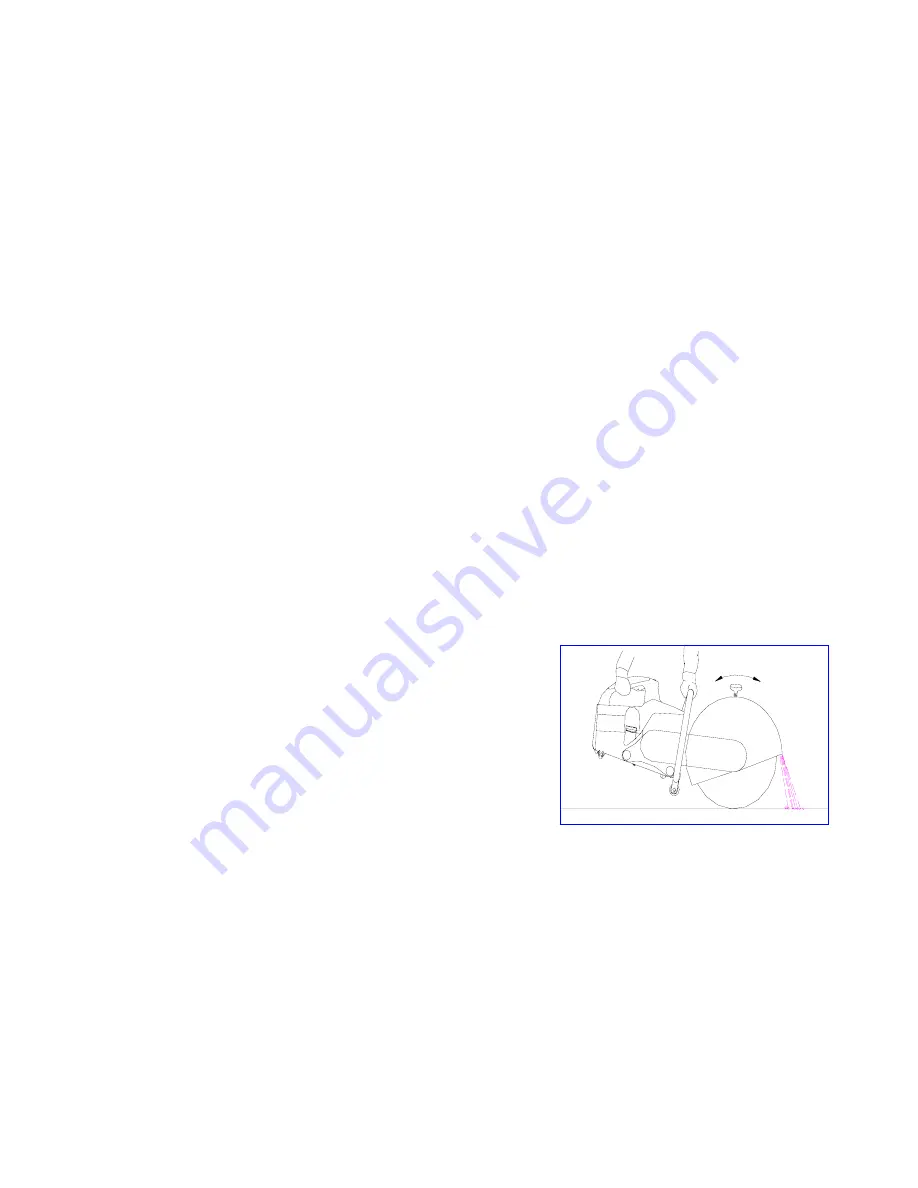
4. Inspection of the cutoff saw before use:
. Make sure there are no loose objects on or near the saw.
. Except for the carburetor adjustment screws, all other bolts, nuts, screws and the
fuel tank cap should be securely tightened. Make sure all rubber hoses for oil flow
are tightly connected with no leaks.
. Make sure the blade rotates smoothly; the starter rope can be pulled through and
guided back without being tangled.
. Check to make sure the Throttle Trigger, the Full Throttle Lock Button, the Choke
Lever, the Decompression Valve and the kill Switch all function well without failure.
. Check to make sure the blade guard has no
visual damage. Adjust the guard as necessary
so the spark beam generated during cutting
can be directed away from the operator. (Ref.
Fig.2)
Fig 2
16
Summary of Contents for EHS350A
Page 44: ...1 Crankshaft Housing Assembly Item Ref Description Qty 1 1E49F01011 Screw M5 20 10 43...
Page 46: ...2 Crankshaft Piston Assembly 45...
Page 48: ...3 Cylinder Muffler Assembly 47...
Page 50: ...4 Fuel Tank Carburetor 49...
Page 52: ...5 Handle Main Cover Assembly 51...
Page 54: ...6 Air Filter Assembly 53...
Page 56: ...7 Cutter Assembly 55...
Page 58: ...8 Transmission Box Assembly 57...