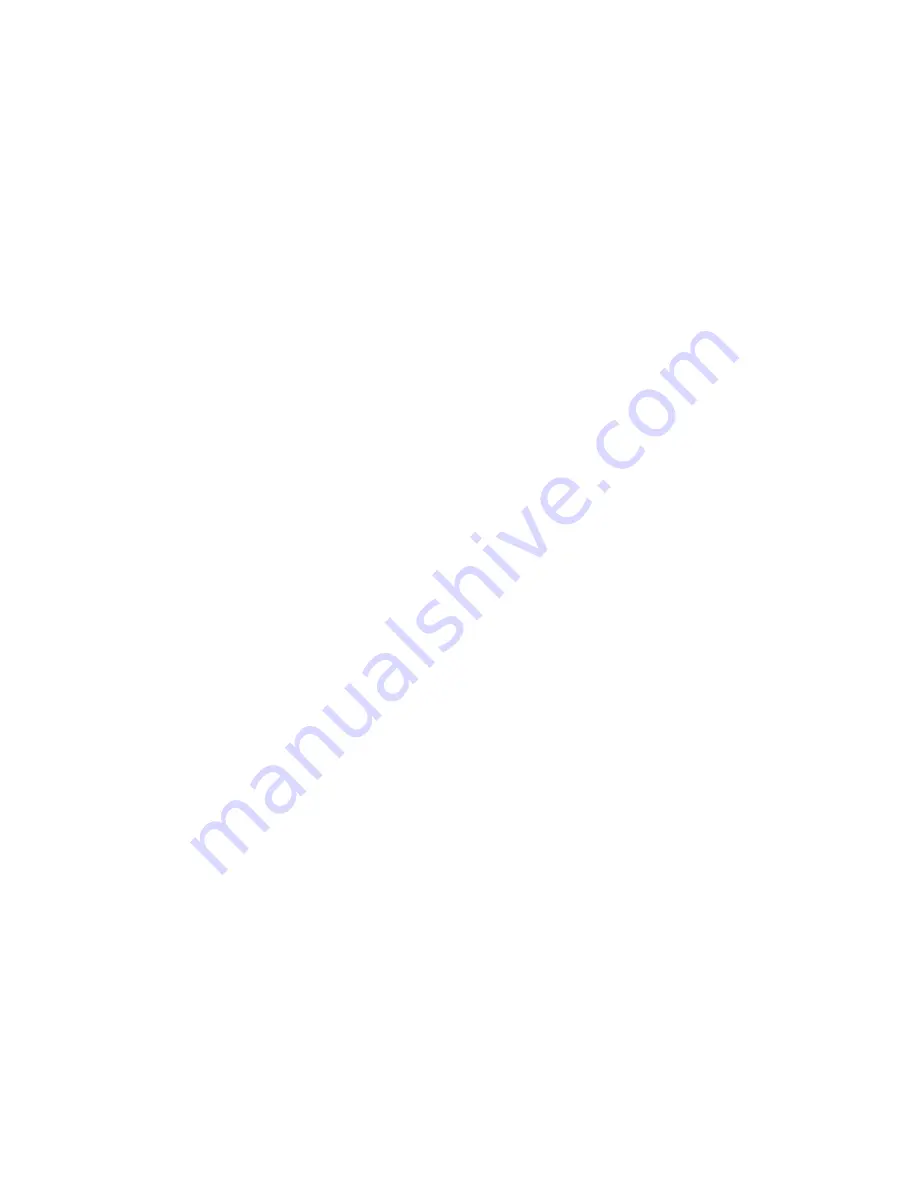
15
REVISED 5/31/05
Diagnostics:
The yaw rate sensor is only operational in conjunction with
an Advanced ABS ECU. No independent diagnostics can
be performed on the sensor.
Removal:
1. Unplug sensor cable assembly from body of sensor.
The connector must be twisted and pulled gently to
release.
2. In some mounting configurations, the sensor can be
removed independently from its mounting bracket.
Otherwise, remove entire assembly, then remove
sensor from bracket.
3. Take note of the direction in which the connector is
pointed.
Installation:
1. Obtain a new sensor. The sensor is not repairable in the
field. WARNING: Only Bendix-approved replacement
sensors must be used to prevent negatively affecting
antilock system reliability and braking performance
issues.
2. Assembly yaw rate sensor housing to mounting bracket.
The bracket must be the same design as used on the
original vehicle configuration.
3. Using three M8 size bolts, the fixing torque should be
between 18 and 22N. The connector should be facing
in the same direction as the removed sensor. The unit
must not be installed upside-down where there is a
pressure-balancing hole.
4. The sensor should be as level as possible and parallel
to the road surface when installed on the vehicle.
5. Reconnect the connector. Ensure that there will be no
force applied to the sensor because the connector is
pulling on the sensor body.
CAUTION: When removing or installing the sensor,
care must be used to prevent damage. Do not strike
or pry the sensor. Do not use an impact tool to install
the mounting hardware.
Sensor Location Modifications
The location and orientation of the Yaw Rate Sensor must
not be altered. When servicing, an identical component
must be used in the same orientation (using OEM brackets
& torque requirements). During installation follow the OEM
leveling guidelines.
Yaw Rate Sensor Calibration:
The yaw rate sensor calibration can only be achieved via
the Advanced ABS ECU. The sensor must be recalibrated
after any of these situations:
• Replacement of the sensor
• After an accident that may have led to damage of the
yaw rate sensor
The calibration procedure is preformed using Bendix
®
ACom
™
Diagnostics V4.0 or higher.
See “Troubleshooting Diagnostic Trouble Codes: Yaw Rate
Sensor” for the calibration procedure.
BRAKE DEMAND SENSOR CALIBRATION
Calibration must be performed under the following conditions:
• After servicing any pressure sensor related DTCs
• Replacement of any sensor
The calibration procedure is performed using Bendix
®
ACom
™
Diagnostics V4.0 or newer versions.
See “Troubleshooting Diagnostic Trouble Codes:
Brake Demand Sensor/Load Sensor” for the calibration
procedure.
PRESSURE SENSOR INSTALLATION
REQUIREMENTS
Service Checks:
1. Check all wiring and connectors. Make sure all
connections are free from visible damage.
2. Examine the sensor. Make sure the sensor and its
interface to the pressure location are not damaged.
Diagnostics:
The pressure sensor can be independently diagnosed
when supplied with a five volt voltage supply to the B
location and ground to the A location. Signal output on
the C location should read approximately 0.5V if there is
no pressure applied. The signal output should increase
proportionately as pressure is applied, up to a maximum
of 4.5V at 150 psi.
Removal:
1. Unplug sensor cable assembly from body of sensor.
Pull gently on the mounting tab and connector until it
disengages.
2. Remove sensor from its pressure mounting using
approved air brake push in fitting tools.
Installation:
1. Obtain a new sensor. The sensor is not repairable in
the field.
2. Insert sensor into pressure fitting using approved
tools.
3. Reconnect the connector. Ensure that there will be no
force applied to the sensor because the connector is
pulling on the sensor body.
4. If the wire harness leading to the sensor is being
replaced, ensure that it is adequately tie wrapped.
Pressure Sensor Calibration:
There is no need for pressure sensor calibration as long
as the part replaced its identical to the part removed and
a component approved for use with the Bendix Advanced
ABS system. However, replacement of brake demand
sensors or clearing of demand pressure sensor related
DTCs require the following:
1. Use of ACom V4 or newer to clear the active p-sensor
fault.
2. Carrying out the demand p-sensor initialization
procedure which involves applying service brakes of
90 psi or greater for 3 sec (while stationary).
Once this procedure is carried out successfully, if there are
no other active DTCs, ATC/ESP indicator will no longer
illuminate.
Summary of Contents for X3-45 Multiplex
Page 1: ...COACH MANUFACTURER MAINTENANCE MANUAL X3 COACHES PA1562 4th edition...
Page 13: ...Section 00 GENERAL INFORMATION 11 PA1562 FIGURE 16 METRIC US STANDARD CONVERSION TABLE 00005...
Page 14: ...Section 00 General Information PA1562 12 FIGURE 17 CONVERSION CHART 00006...
Page 30: ......
Page 110: ......
Page 236: ......
Page 253: ...FAULT CODE MANUAL Created on 00 04 25 15 30 1 FAULT CODE MANUAL B7L B7TL B12...
Page 278: ......
Page 317: ......
Page 318: ......
Page 319: ......
Page 320: ......
Page 321: ......
Page 322: ......
Page 323: ......
Page 324: ......
Page 325: ......
Page 326: ......
Page 327: ......
Page 328: ......
Page 329: ...DQD 6SLFHU ULYHVKDIW 6HUYLFH 0DQXDO 660 XO 6HULHV 8QLYHUVDO RLQWV DQG ULYHVKDIWV...
Page 372: ......
Page 379: ......
Page 439: ...Forward and Rear Axle Carrier Diagnostic Flowcharts TP 99125 Issued 12 99 TECHNICAL BULLETIN...
Page 484: ......
Page 494: ......
Page 500: ...Notes Copyright 2002 Maintenance Manual MM 0204 Page 4 ArvinMeritor Inc Issued 08 02...
Page 504: ...Notes Copyright 2002 Maintenance Manual MM 0204 Page 8 ArvinMeritor Inc Issued 08 02...
Page 526: ...16 BW2158 Honeywell Commercial Vehicle Systems Company 4 2001 Printed in USA...
Page 530: ......
Page 538: ......
Page 546: ......
Page 553: ......
Page 566: ......
Page 702: ......
Page 760: ......
Page 778: ......
Page 779: ......
Page 780: ......
Page 781: ......
Page 782: ......
Page 783: ......
Page 784: ......
Page 785: ......
Page 786: ......
Page 787: ......
Page 788: ......
Page 789: ......
Page 790: ......
Page 791: ......
Page 792: ......
Page 793: ......
Page 794: ......
Page 795: ......
Page 796: ......
Page 797: ......
Page 798: ......
Page 799: ......
Page 800: ......
Page 801: ......
Page 802: ......
Page 803: ......
Page 804: ......
Page 805: ......
Page 806: ......
Page 807: ......
Page 808: ......
Page 809: ......
Page 810: ......
Page 811: ......
Page 812: ......
Page 813: ......
Page 814: ......
Page 815: ......
Page 816: ......
Page 817: ......
Page 818: ......
Page 819: ......
Page 820: ......
Page 821: ......
Page 822: ......
Page 823: ......
Page 824: ......
Page 825: ......
Page 826: ......
Page 827: ......
Page 828: ......
Page 829: ......
Page 830: ......
Page 831: ......
Page 832: ......
Page 833: ......
Page 834: ......
Page 835: ......
Page 836: ......
Page 837: ......
Page 838: ......
Page 839: ......
Page 840: ......
Page 841: ......
Page 842: ......
Page 843: ......
Page 844: ......
Page 845: ......
Page 846: ......
Page 847: ......
Page 848: ......
Page 849: ......
Page 850: ......
Page 851: ......
Page 852: ......
Page 853: ......
Page 854: ......
Page 855: ......
Page 856: ......
Page 857: ......
Page 858: ......
Page 859: ......
Page 860: ......
Page 861: ......
Page 862: ......
Page 863: ......
Page 864: ......
Page 865: ......
Page 866: ......
Page 867: ......
Page 868: ......
Page 869: ......
Page 870: ......
Page 871: ......
Page 872: ......
Page 873: ......
Page 874: ......
Page 875: ......
Page 876: ......
Page 877: ......
Page 878: ......
Page 880: ......
Page 941: ...Initial Installation Section 2 Initial Installation Installation 14 Maintenance Tips 15...
Page 965: ...Glossary Section 5 Glossary Glossary 39...
Page 967: ......
Page 1012: ......
Page 1115: ......
Page 1116: ......
Page 1118: ......
Page 1119: ......
Page 1123: ......
Page 1124: ......
Page 1125: ......
Page 1126: ......
Page 1127: ......
Page 1128: ......
Page 1130: ......
Page 1133: ......
Page 1134: ......
Page 1136: ......
Page 1138: ......
Page 1139: ......
Page 1140: ......
Page 1141: ......
Page 1142: ......
Page 1196: ......
Page 1197: ...Compressor 62 11052 Rev A WORKSHOP MANUAL for MODEL 05G TWIN PORT COMPRESSOR R...
Page 1198: ...WORKSHOP MANUAL COMPRESSOR MODEL 05G TWIN PORT...
Page 1221: ...Compressor 62 11053 Rev B SERVICE PARTS LIST for MODEL 05G TWIN PORT COMPRESSOR 1 2 3 4 5 6 R...
Page 1249: ......
Page 1250: ......
Page 1251: ...1...
Page 1252: ...2...
Page 1253: ...3...
Page 1254: ...4...
Page 1255: ...5...
Page 1256: ...6...
Page 1257: ...7...
Page 1258: ...8...
Page 1259: ...9...
Page 1260: ......
Page 1265: ...Section 23 ACCESSORIES PA1562 5 FIGURE 2 AUDIO VIDEO CONNECTIONS...
Page 1278: ...Section 23 ACCESSORIES PA1562 18 FIGURE 26 FUNCTIONING OF LAVATORY 23051...
Page 1294: ......
Page 1301: ......
Page 1350: ......
Page 1351: ......
Page 1352: ......
Page 1353: ......
Page 1354: ......
Page 1355: ......
Page 1356: ......
Page 1357: ......
Page 1358: ......
Page 1359: ......
Page 1360: ......
Page 1361: ......
Page 1362: ......
Page 1363: ......
Page 1364: ......
Page 1365: ......
Page 1366: ......
Page 1367: ......
Page 1368: ......
Page 1369: ......
Page 1370: ......
Page 1371: ......
Page 1372: ......
Page 1373: ......
Page 1374: ......
Page 1375: ......
Page 1376: ......
Page 1377: ......
Page 1378: ......
Page 1379: ...LPCM OUTPUT...
Page 1380: ......
Page 1381: ......
Page 1382: ......
Page 1383: ......
Page 1384: ......
Page 1385: ......
Page 1386: ......
Page 1406: ......
Page 1410: ......
Page 1418: ......