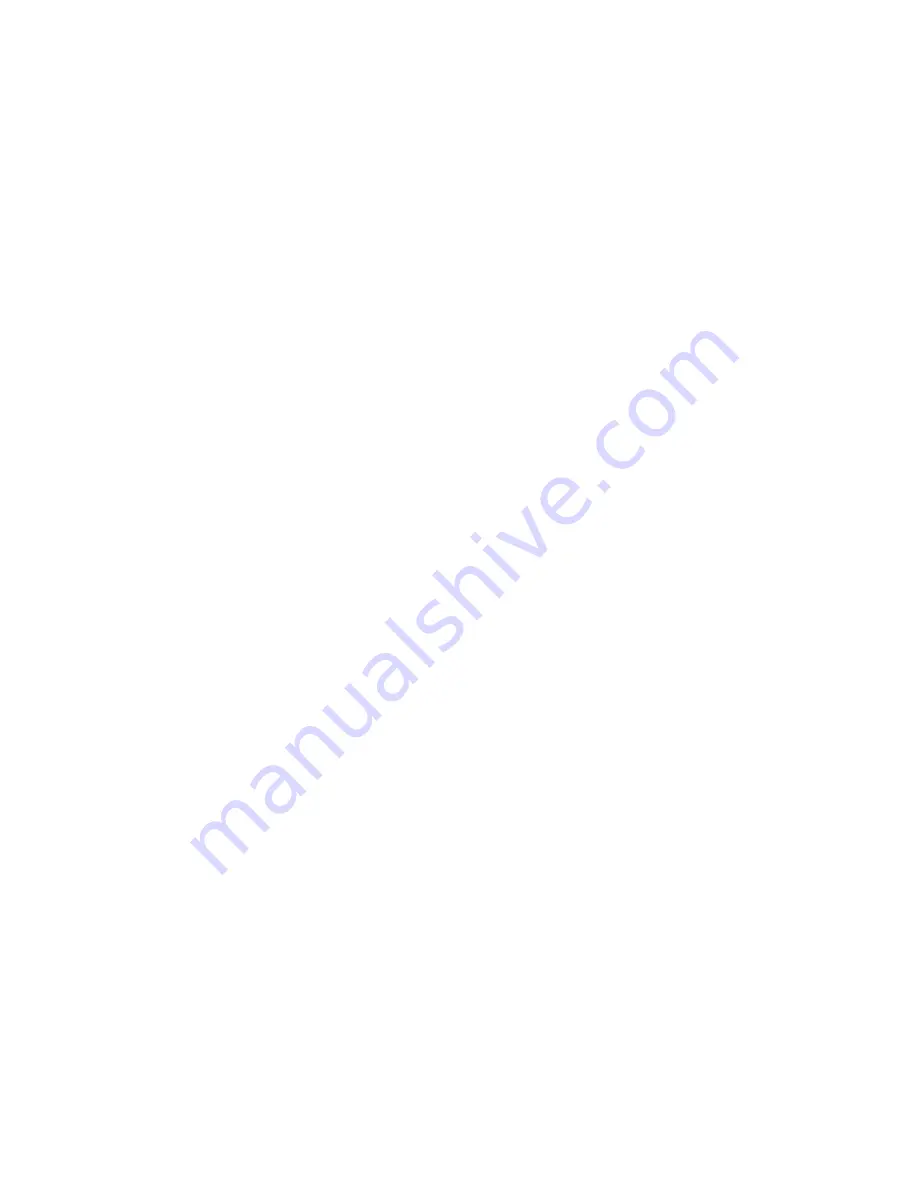
8
REVISED 5/31/05
WARNING: The ABS off-road mode should not be
used on normal, paved road surfaces because vehicle
stability and steerability may be reduced. The ABS
Indicator Lamp will flash slowly to indicate to the driver
that the ABS off-road mode is engaged.
CAUTION: When ABS off-road mode is engaged,
stability functions are disabled at speeds below
approximately 25 mph. The ATC/ESP dash lamp will
illuminate to indicate to the driver that the stability
system is disabled.
The vehicle manufacturer should provide the optional ABS
off-road function only for vehicles that operate on unpaved
surfaces or that are used in off-road applications, and is
responsible for insuring that vehicles equipped with the ABS
off-road function meet all FMVSS-121 requirements and
have adequate operator indicators and instructions.
The vehicle operator activates the off-road function with a
switch on the dash panel. A flashing ABS Indicator Lamp
indicates to the driver that the ABS off-road function is
engaged. To exit the ABS off-road mode, depress and
release the switch. A new ignition cycle will also cause the
ECU to exit the ABS off-road mode.
All-Wheel Drive (AWD) Vehicles
AWD vehicles with an engaged interaxle differential (steer
axle to rear axle)/AWD transfer case may have negative
effects on ABS performance. Optimum ABS performance
is achieved when the lockable differentials are disengaged,
allowing individual wheel control.
Advanced EC-60
™
controllers can be programmed
specifically for this configuration to control the differential
lock/unlock solenoid in the AWD transfer case. When
programmed to do so, the ECU will disengage the locked
interaxle/AWD transfer case during an ABS event and
reengage it once the ABS event has ended.
ATC OPERATION
ATC Functional Overview
Just as ABS improves vehicle stability during braking,
ATC improves vehicle stability and traction during vehicle
acceleration. The EC-60
™
controller ATC function uses
the same wheel speed information and modulator control
as the ABS function. The EC-60
™
controller detects
excessive drive wheel speed, compares the speed to the
front, nondriven wheels, and reacts to help bring the wheel
spin under control. The controller can be configured to use
engine torque limiting and/or differential braking to control
wheel spin. For optimal ATC performance, both methods
are recommended.
ATC/ESP Lamp Output/ATC Mud/Snow Switch
Input
Advanced ECUs control the ATC/ESP dash lamp as
follows.
The ATC/ESP dash lamp illuminates:
1. During power up (e.g. when the vehicle is started) for
approximately 2.5 seconds and turns off after the self
test is completed, providing no diagnostic trouble codes
are present.
2. When ESP or ATC is disabled for any reason.
3. During an ESP or ATC event (the lamp will flash rapidly
at a rate of 2.5 per second).
4. When the ECU is placed in the ATC off-road mode
(the lamp will flash steadlily at a rate of once per 2.5
seconds). This notifies the vehicle operator that the
ATC Mud/Snow mode is active.
5. When the ECU is placed in the ABS off-road mode.
When in this mode, ESP will be disabled below 25 mph
and its inactive status will be indicated by a steadily
illuminated ATC/ESP lamp.
Differential Braking
Differential braking within ATC is automatically activated
when drive wheel(s) on one side of the vehicle are spinning
excessively, which typically occurs on road surfaces with
patches of ice. The traction system will then lightly apply the
brake to the drive wheel(s) that are spinning excessively.
The vehicle differential will then drive the wheels on the
other side of the vehicle.
Differential braking as part of ATC functionality is available
at vehicle speeds up to 25 MPH.
Disabling ATC Differential Braking
ATC differential braking is disabled under the following
conditions:
1. During power up (e.g. when the vehicle is started), until
the ECU detects a service brake application.
2. If the ECU receives a J1939 message indicating that
the vehicle is parked.
3. When the dynamometer test mode is active. The
dynamometer test mode is entered using the diagnostic
blink code switch or by using a diagnostic tool (such as
Bendix
®
ACom
™
Diagnostics).
4. In response to a serial communications request from
a diagnostic tool.
5. If "ATC Differential Braking" function is activated for a
long time period to avoid overheating of the brakes,
it would take approximately 3 continuous minutes of
activation for the timeout to occur. Once timed out,
approixmately 2 minutes of "cool off" time would be
required before ATC Differential Braking can be used
again.
6. When certain diagnostic trouble code conditions are
detected.
Engine Torque Limiting with Smart ATC
™
Traction Control
The EC-60
™
controller uses Engine Torque Limiting to
control drive axle wheel slip. This is communicated to the
engine control module (using J1939), and is available at
all vehicle speeds.
Summary of Contents for X3-45 Multiplex
Page 1: ...COACH MANUFACTURER MAINTENANCE MANUAL X3 COACHES PA1562 4th edition...
Page 13: ...Section 00 GENERAL INFORMATION 11 PA1562 FIGURE 16 METRIC US STANDARD CONVERSION TABLE 00005...
Page 14: ...Section 00 General Information PA1562 12 FIGURE 17 CONVERSION CHART 00006...
Page 30: ......
Page 110: ......
Page 236: ......
Page 253: ...FAULT CODE MANUAL Created on 00 04 25 15 30 1 FAULT CODE MANUAL B7L B7TL B12...
Page 278: ......
Page 317: ......
Page 318: ......
Page 319: ......
Page 320: ......
Page 321: ......
Page 322: ......
Page 323: ......
Page 324: ......
Page 325: ......
Page 326: ......
Page 327: ......
Page 328: ......
Page 329: ...DQD 6SLFHU ULYHVKDIW 6HUYLFH 0DQXDO 660 XO 6HULHV 8QLYHUVDO RLQWV DQG ULYHVKDIWV...
Page 372: ......
Page 379: ......
Page 439: ...Forward and Rear Axle Carrier Diagnostic Flowcharts TP 99125 Issued 12 99 TECHNICAL BULLETIN...
Page 484: ......
Page 494: ......
Page 500: ...Notes Copyright 2002 Maintenance Manual MM 0204 Page 4 ArvinMeritor Inc Issued 08 02...
Page 504: ...Notes Copyright 2002 Maintenance Manual MM 0204 Page 8 ArvinMeritor Inc Issued 08 02...
Page 526: ...16 BW2158 Honeywell Commercial Vehicle Systems Company 4 2001 Printed in USA...
Page 530: ......
Page 538: ......
Page 546: ......
Page 553: ......
Page 566: ......
Page 702: ......
Page 760: ......
Page 778: ......
Page 779: ......
Page 780: ......
Page 781: ......
Page 782: ......
Page 783: ......
Page 784: ......
Page 785: ......
Page 786: ......
Page 787: ......
Page 788: ......
Page 789: ......
Page 790: ......
Page 791: ......
Page 792: ......
Page 793: ......
Page 794: ......
Page 795: ......
Page 796: ......
Page 797: ......
Page 798: ......
Page 799: ......
Page 800: ......
Page 801: ......
Page 802: ......
Page 803: ......
Page 804: ......
Page 805: ......
Page 806: ......
Page 807: ......
Page 808: ......
Page 809: ......
Page 810: ......
Page 811: ......
Page 812: ......
Page 813: ......
Page 814: ......
Page 815: ......
Page 816: ......
Page 817: ......
Page 818: ......
Page 819: ......
Page 820: ......
Page 821: ......
Page 822: ......
Page 823: ......
Page 824: ......
Page 825: ......
Page 826: ......
Page 827: ......
Page 828: ......
Page 829: ......
Page 830: ......
Page 831: ......
Page 832: ......
Page 833: ......
Page 834: ......
Page 835: ......
Page 836: ......
Page 837: ......
Page 838: ......
Page 839: ......
Page 840: ......
Page 841: ......
Page 842: ......
Page 843: ......
Page 844: ......
Page 845: ......
Page 846: ......
Page 847: ......
Page 848: ......
Page 849: ......
Page 850: ......
Page 851: ......
Page 852: ......
Page 853: ......
Page 854: ......
Page 855: ......
Page 856: ......
Page 857: ......
Page 858: ......
Page 859: ......
Page 860: ......
Page 861: ......
Page 862: ......
Page 863: ......
Page 864: ......
Page 865: ......
Page 866: ......
Page 867: ......
Page 868: ......
Page 869: ......
Page 870: ......
Page 871: ......
Page 872: ......
Page 873: ......
Page 874: ......
Page 875: ......
Page 876: ......
Page 877: ......
Page 878: ......
Page 880: ......
Page 941: ...Initial Installation Section 2 Initial Installation Installation 14 Maintenance Tips 15...
Page 965: ...Glossary Section 5 Glossary Glossary 39...
Page 967: ......
Page 1012: ......
Page 1115: ......
Page 1116: ......
Page 1118: ......
Page 1119: ......
Page 1123: ......
Page 1124: ......
Page 1125: ......
Page 1126: ......
Page 1127: ......
Page 1128: ......
Page 1130: ......
Page 1133: ......
Page 1134: ......
Page 1136: ......
Page 1138: ......
Page 1139: ......
Page 1140: ......
Page 1141: ......
Page 1142: ......
Page 1196: ......
Page 1197: ...Compressor 62 11052 Rev A WORKSHOP MANUAL for MODEL 05G TWIN PORT COMPRESSOR R...
Page 1198: ...WORKSHOP MANUAL COMPRESSOR MODEL 05G TWIN PORT...
Page 1221: ...Compressor 62 11053 Rev B SERVICE PARTS LIST for MODEL 05G TWIN PORT COMPRESSOR 1 2 3 4 5 6 R...
Page 1249: ......
Page 1250: ......
Page 1251: ...1...
Page 1252: ...2...
Page 1253: ...3...
Page 1254: ...4...
Page 1255: ...5...
Page 1256: ...6...
Page 1257: ...7...
Page 1258: ...8...
Page 1259: ...9...
Page 1260: ......
Page 1265: ...Section 23 ACCESSORIES PA1562 5 FIGURE 2 AUDIO VIDEO CONNECTIONS...
Page 1278: ...Section 23 ACCESSORIES PA1562 18 FIGURE 26 FUNCTIONING OF LAVATORY 23051...
Page 1294: ......
Page 1301: ......
Page 1350: ......
Page 1351: ......
Page 1352: ......
Page 1353: ......
Page 1354: ......
Page 1355: ......
Page 1356: ......
Page 1357: ......
Page 1358: ......
Page 1359: ......
Page 1360: ......
Page 1361: ......
Page 1362: ......
Page 1363: ......
Page 1364: ......
Page 1365: ......
Page 1366: ......
Page 1367: ......
Page 1368: ......
Page 1369: ......
Page 1370: ......
Page 1371: ......
Page 1372: ......
Page 1373: ......
Page 1374: ......
Page 1375: ......
Page 1376: ......
Page 1377: ......
Page 1378: ......
Page 1379: ...LPCM OUTPUT...
Page 1380: ......
Page 1381: ......
Page 1382: ......
Page 1383: ......
Page 1384: ......
Page 1385: ......
Page 1386: ......
Page 1406: ......
Page 1410: ......
Page 1418: ......