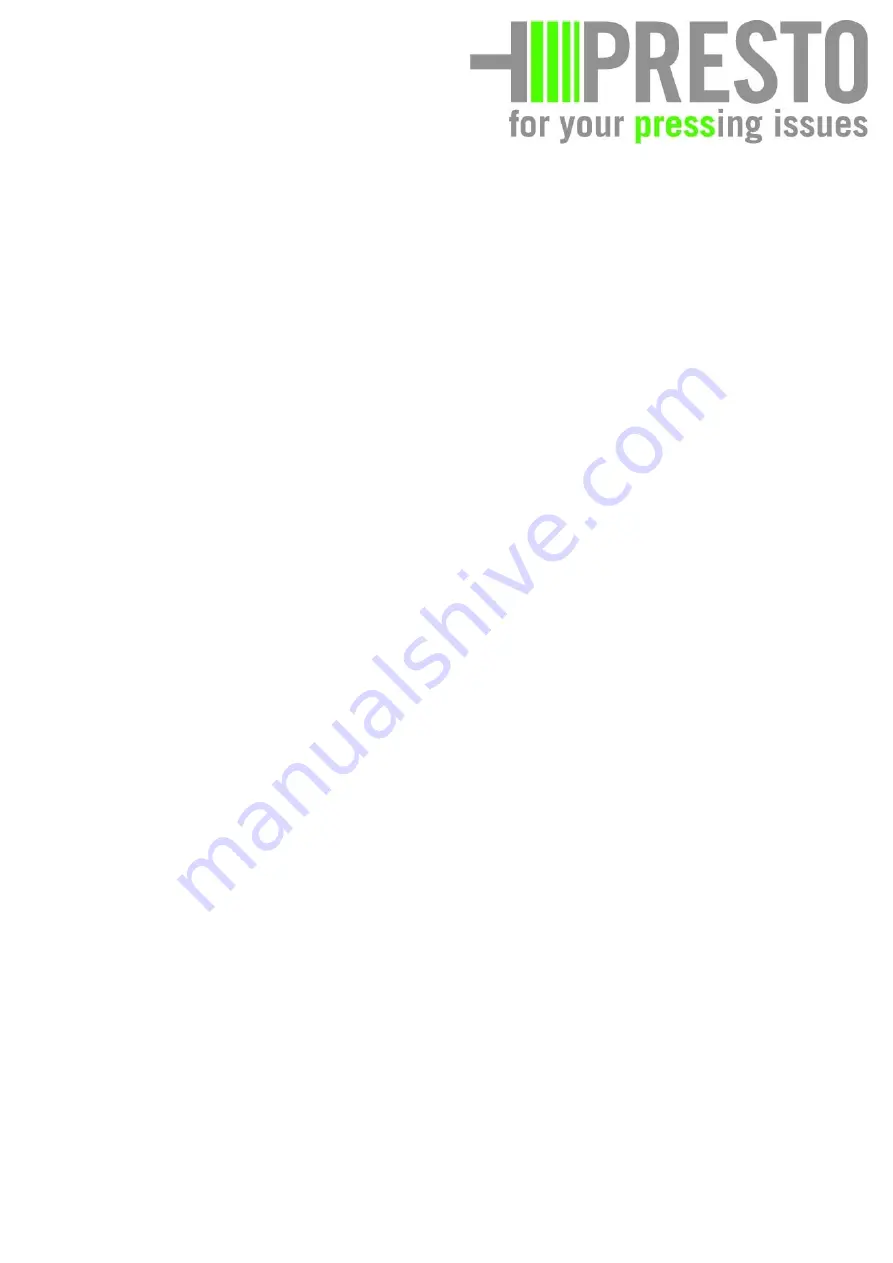
Original
version
Revision
status
04/15
Operating
manual
and
maintenance
instructions
CHANNEL
BALING
PRESS
TYPES:
CONTI
COMPACT
CC
‐
20
V,
CC
‐
30
V,
CC
‐
40
V
GmbH
&
Co.
KG
Gewerbepark
4
D
‐
49196
Bad
Laer
+49
(0)
5424
2927
0
Project:
Channel
Baling
Press
Type:
______________________
Machine.
‐
no.:
______________________
Year
of
construction:
______________________
Customer:
______________________