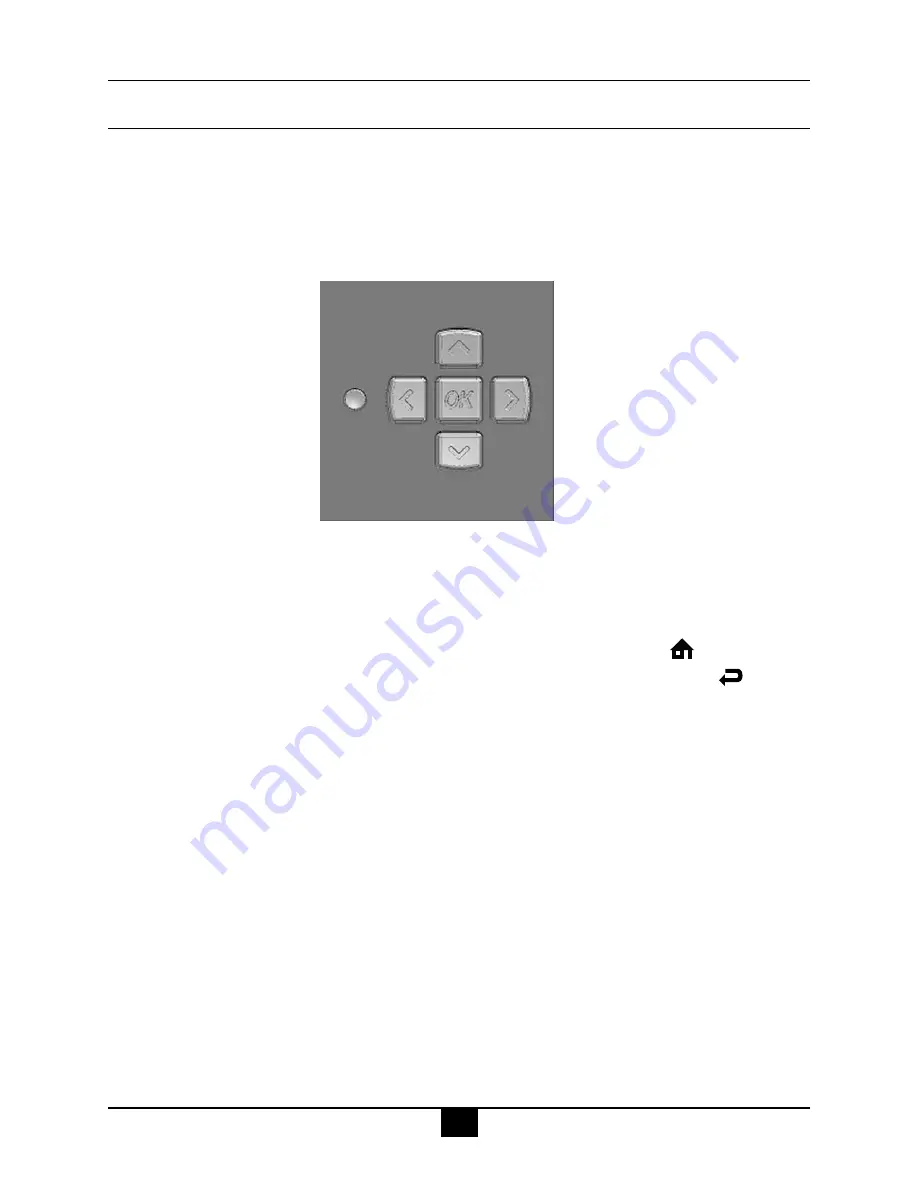
41
9.0
ACVMax Operation
9.1 ACVMax Navigation
Navigation is performed through four arrow buttons
UP
,
DOWN
,
LEFT
,
RIGHT
with a center
OK
button for making selections and entering information. The
INSTALLER
button (the small
round button) provides the installing contractor with full access to all available features after
entering a password. Reference the ACVMax Control Supplement for Installer level functions.
Figure 30 – ACVMax Navigation Buttons
The Main Menu can be entered from the Home Screen by pressing the
OK
button. The menu
system utilizes icons to represent each selection. The current selected menu is displayed as a
reversed image with a text description shown at the top of the display. Menus can be entered by
highlighting the desired icon and pressing the
OK
button. The Home Screen
icon at the bot-
tom of each screen returns to the Home Screen when selected. The Previous Screen
icon at
the bottom of each screen returns to the previous screen when selected.