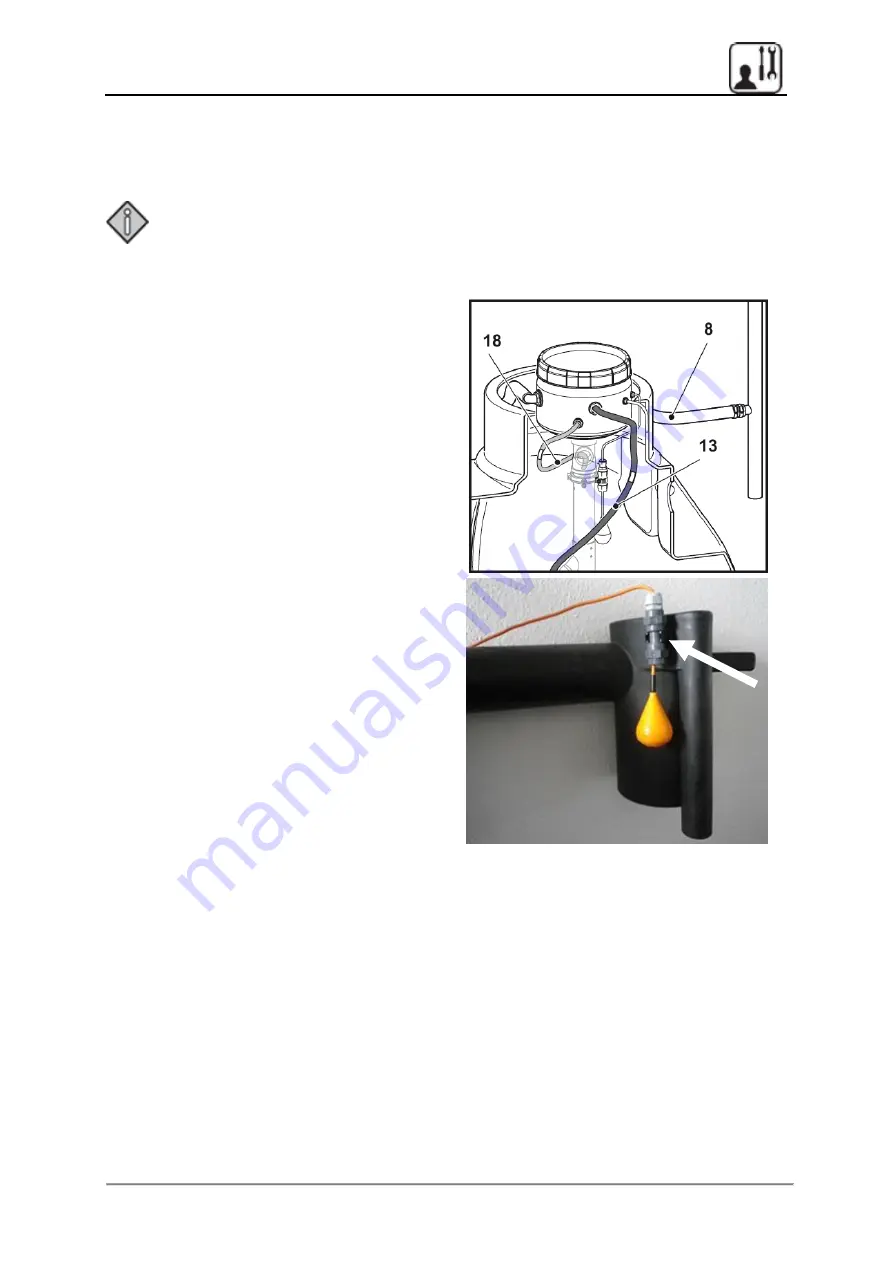
7. Installation and start-up
Premier Tech
38 / 64
Solido SMART
DOKK5110E 15.04.2020
7.3.6
Connecting the technology capsule
•
Remove the supply air hose (
8
), the blue compressed air hose (
18
) that is pre-assembled
in the container, and the white tube diffuser hose (
13
).
•
If necessary, shorten the compressed air hoses to the required lengths.
Note:
The length of the hoses is sufficient for installation with a shaft design of max.
1.20 m. With the standard version as per the scope of delivery, shortening the
hoses by up to 60 cm is recommended).
•
Connect the hoses according to the
colour coding.
•
Connect the supply air house to the
capsule outside the shaft.
•
Loosely bundle the hoses using a cable
tie, and place them around the capsule.
•
Lock the SWS float switch in place on
the pre-assembled retaining clip for the
sampling bottle in the container.
•
Fix overfill alarm (float switch SWS) to
the pre-installed clip at the sample pot
•
Please check that the clip clicks between
the two sleeves (see white flash).
7.3.7
Inserting the technology capsule
•
Slightly turn the capsule when lowering it onto the shaft, so that the hoses are placed
around the capsule.
•
Carefully place the technology capsule onto the holder on the top end of the clearwater
lifter so that the capsule is positioned securely. For larger installation depths, the capsule
can be positioned on an extension pipe (HT DN75, 1 m long, purchase order number
KKZT0033) to improve accessibility.
•
Make sure that all hoses are connected properly so that they lie next to the capsule in the
shaft and ensure that it is possible to remove the capsule for maintenance purposes.
7.3.8
Notes for plants with pumped outlet KWP (option)
Please note information for plants with pumped outlet in separate manual DOKK7314E,
which is included in the delivery and part of warranty conditions.