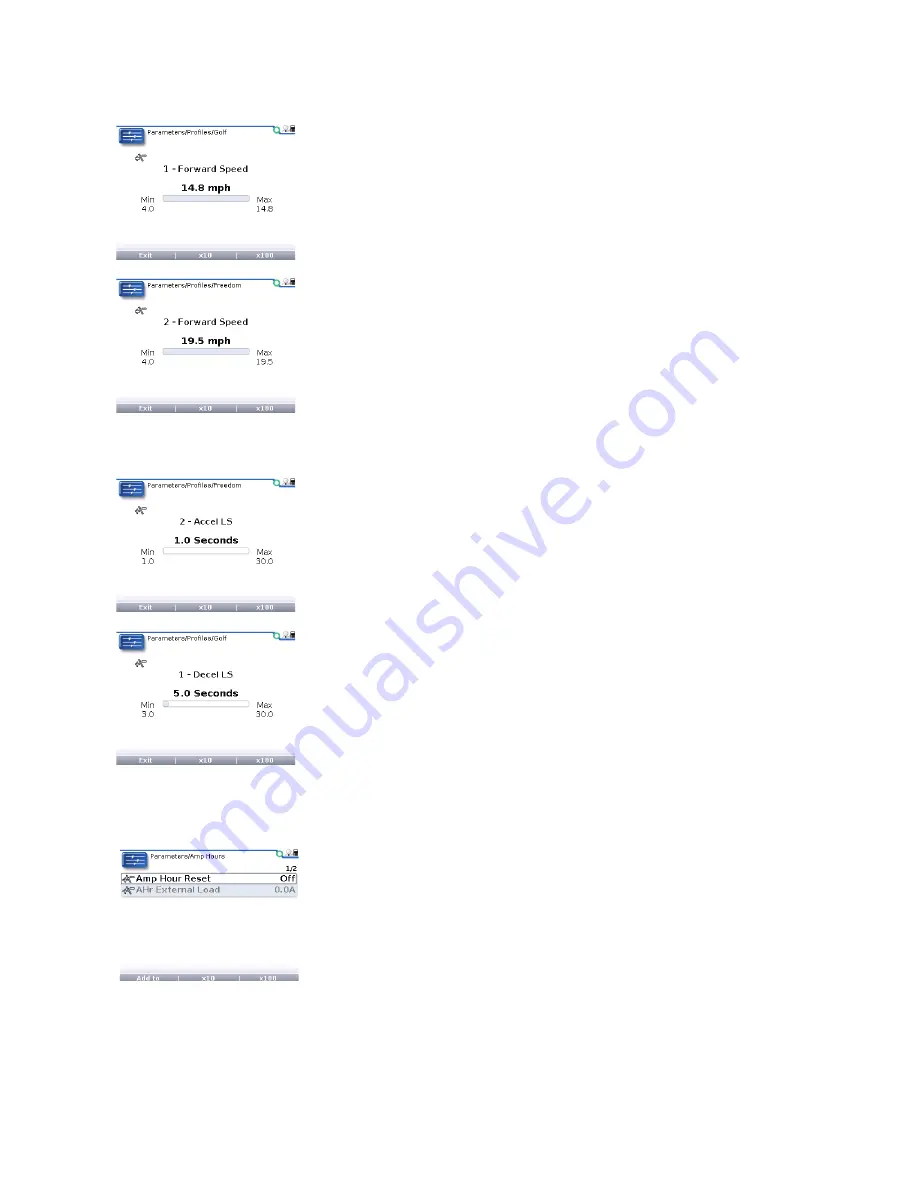
B
FAULT TESTING
Read all of SAFETY and this section before attempting any procedure. Pay particular attention to Notices, Cautions, Warnings and Dangers.
143
Repair and Service Manual
699327
The max speed can be adjusted under “Forward Speed” and “Reverse
Speed.”
•
Golf Vehicles
•
Forward
•
min value = 4.0 mph
•
max value = 14.8 mph
•
Reverse
•
min value = 3.0 mph
•
max value = 6.0 mph
•
Freedom Vehicles
•
Forward
•
min value = 4.0 mph
•
max value = 19.5 mph
•
Reverse
•
min value = 3.0 mph
•
max value = 6.0 mph
Parameters for acceleration and deceleration rates can be adjusted. Settings
are the same for both Golf and Freedom models.
•
Acceleration
•
HS
•
min value = 3.0 seconds
•
max value = 30.0 seconds
•
LS
•
min value = 1.0 second
•
max value = 30.0 seconds
•
Deceleration
•
Both HS and LS
•
min value = 3.0 seconds
•
max value = 30.0 seconds
•
Reverse Acceleration
•
Both HS and LS
•
min value = 7.0 seconds
•
max value = 30.0 seconds
The “Amp Hours” Submenu includes the parameters for “Amp Hour Reset”
(normal values are ON and OFF) and “AHr External Load” (normal values are
between 0.0 and 100.0).
Fig. 8 Handheld Tool Function (Continued)
PRELIMINARY