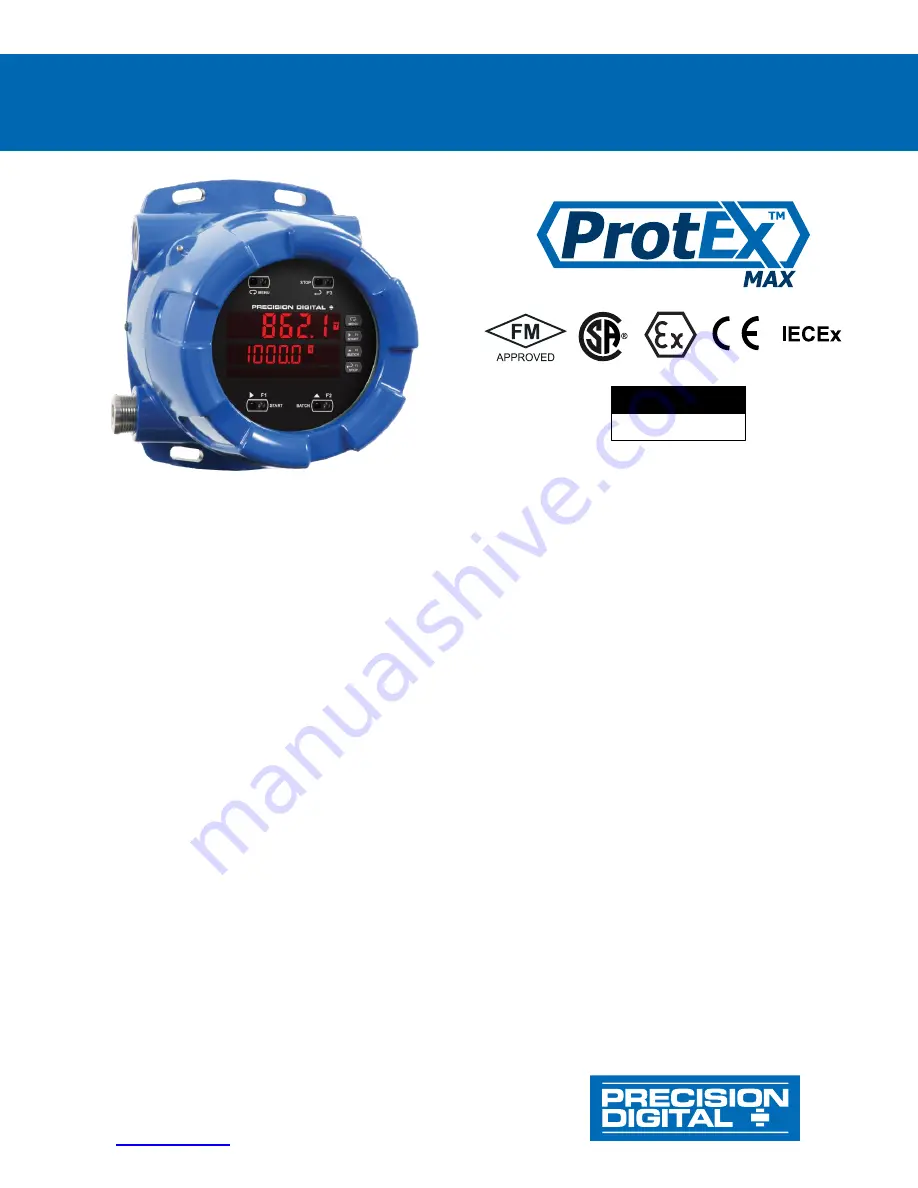
ProtEX-MAX PD8-6210 Explosion-Proof Batch Controller
Instruction Manual
PRECISION DIGITAL CORPORATION
233 South Street • Hopkinton MA 01748 USA
Tel (800) 343-
1001 • Fax (508) 655-8990
•
Fully-Approved Explosion-Proof Batch Controllers
•
0-20 mA, 4-20 mA, 0-5 V, 1-5 V, and ±10 V Inputs with ±0.03% Accuracy
•
Dual-Line 6-Digit Display, 0.6" (15 mm) & 0.46" (12 mm)
•
SafeTouch Through-Glass Button Programming
•
Display Mountable at 0°, 90°, 180°, & 270°
•
Isolated 24 VDC @ 25 mA Transmitter Power Supply
•
Easy Field Scaling in Engineering Units without Applying an Input
•
4 Relays with Interlocking Capa Isolated 4-20 mA Output
•
Free PC-Based, On-Board, MeterView Pro USB Programming Software
•
SunBright Display Standard Feature; Great for Outdoor Applications
•
Start / Pause / Stop, Change Batch with Front Panel Buttons
•
Display Batch Total, Rate, Grand Total, Count or Preset
•
Single or Multi-Stage Batch Control (Up to 4 Relays)
•
Front Panel or Remote Total Reset
•
Automatic Overrun Correction
•
Automatic or Manual Batch Control
•
Low or High Flow Alarms while Batching
•
32-Point Linearization, Square Root Extraction and Programmable Exponent Function
•
Operating Temperature Range: -40 to 60°C (-40 to 140°F)
•
FM Approved as Explosion-Proof / Dust-Ignition-Proof / Flame-Proof
•
CSA Certified as Explosion-Proof / Dust-Ignition-Proof / Flame-Proof
•
ATEX and IECEx Certified as Flame-Proof
•
Input Power Options: 85-265 VAC / 90-265 VDC or 12-24 VDC / 12-24 VAC
•
Programmable Display, Function Keys & Digital Inputs
•
Flanges for Wall or Pipe Mounting
•
Explosion-Proof, IP68, NEMA 4X Die-Cast Aluminum Enclosure
•
On-Board RS-485 Serial Communications
•
Modbus RTU Communication Protocol Standard
•
Password Protection
•
Four 3/4" NPT Threaded Conduit Openings (Two Plugs Installed)
•
3-Year Warranty
MeterView Pro
USB Install