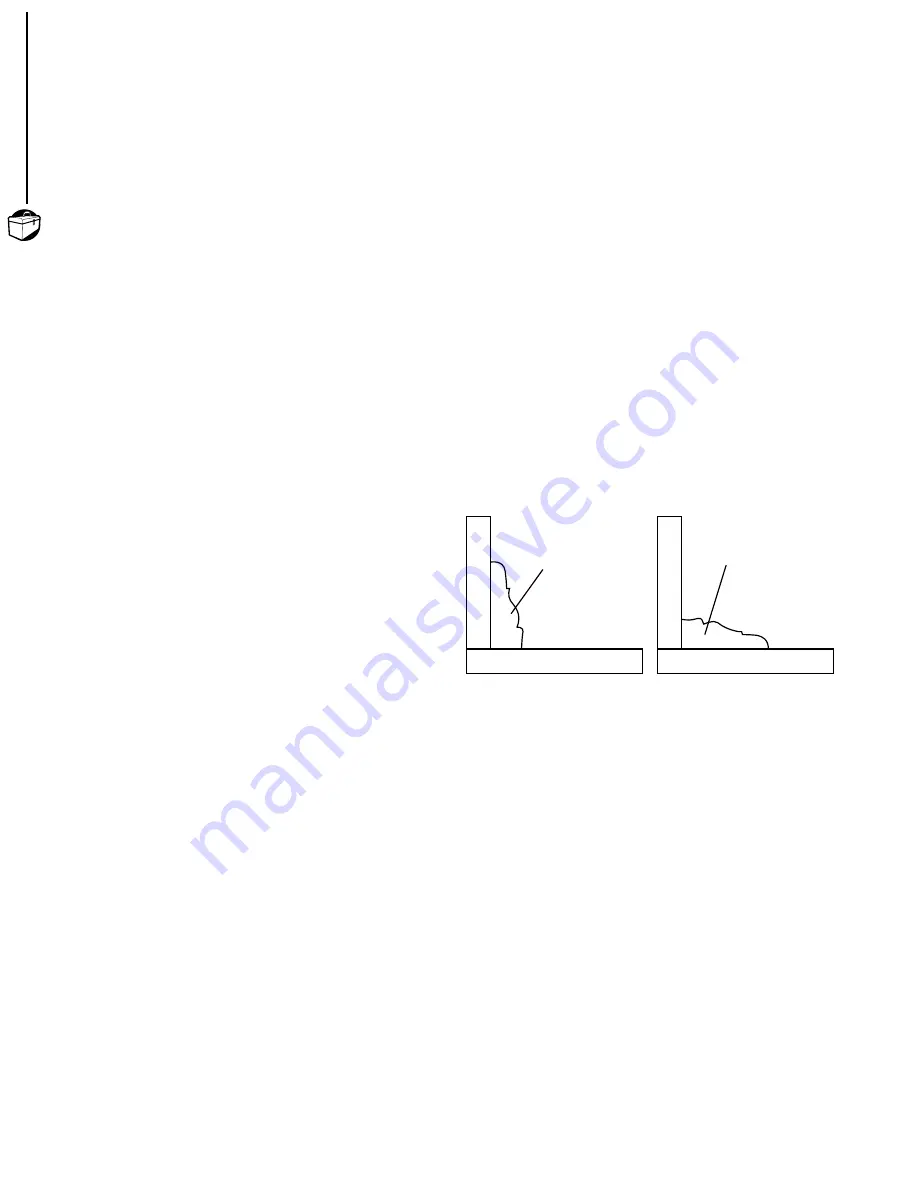
BASIC SAW OPERATION
• Place at least 6-3/4 in. away from the path of the
blade-out of the “no-hands zone”.
• Hold workpiece firmly against the fence to prevent
movement toward the blade.
• With the power switch OFF, bring the saw blade down
to the workpiece to see the cutting path of the blade.
• Press in lock-off switch in trigger switch handle.
• Squeeze trigger switch to start saw.
• Lower blade into workpiece with a firm downward
position.
• Hold the cutting arm in the down position .
• Release trigger switch and wait for all moving parts to
stop before moving your hands and raising the cutting
arm.
• If the blade doesn’t stop within 6 seconds unplug the
saw and follow the instructions in TROUBLESHOOTING
section.
SWITCH ACTIVATION
To reduce the likelihood of accidental starting a thumb
activated lock-OFF switch is located on top of the switch
handle. The lock –OFF switch must be pushed in before
the trigger switch can be activated and the miter saw
started.
MITER CUT
• Turn the miter handle counterclockwise to unlock the
miter table.
• While holding the miter handle, press down on the
positive stop locking lever to disengage the positive stop
locking lever.
• Rotate the miter table to the right or left with the miter
handle.
• When the table is in the desired position as shown on
the miter scale, release the positive stop clocking lever
handle and tighten the miter handle .The table is now
locked at the desired angle. Positive stops are provided
at 0°,15°,22.5°,31.6°, and 45°.
BEVEL CUT
• Loosen the bevel lock handle.
• Tilt the cutting head to the desired angle as shown on
the bevel scale. The blade can be positioned at any
angle from a 90° straight cut (0°on the scale) to a 45°
left bevel.
• Tighten the bevel lock handle to lock the cutting head in
position.
• Positive stops are provided at 0° and 45°.
COMPOUND CUT
• Loosen the bevel lock handle and position the cutting
head at the desired bevel position. Lock the bevel lock
handle.
• Loosen the miter table lock handle. Press down the
positive stop locking lever.
• Position the table at the desired angle.
• Release the positive stop locking lever and lock the
miter handle.
CUTTING BOWED MATERIAL
• A bowed workpiece must be positioned against the
fence and secured with a clamping device as shown
before cutting.
• Do not position workpiece incorrectly or try to cut the
workpiece without the support of the fence. . This will
cause the blade to bind and could result in personal
injury.
CUTTING BASE MOLDING
• Base moldings and many other moldings can be cut on
a compound miter saw. The setup of the saw depends
on molding characteristics and application .as shown.
• Always make sure molding rest firmly against fence and
table.
• Use hold-down or C-clamps, whenever possible, and
place tape on the area being clamped to avoid marks.
• Reduce splintering by taping the cut area prior to
making cut. Mark cut line directly on the tape.
• Splintering typically happens due to wrong blade
application and thinness of the material.
NOTE: Always perform a dry run cut so you can determine
if the operation being attempted is possible before power
is applied to the saw.
CUTTING CROWN MOLDING
• Crown molding must be cut exactly to fit properly.
• There are two ways to cut crown molding: flat on table
or angled to table and fence.
• The two surfaces on a piece of crown molding that fit
flat against the ceiling and wall are at angles that, when
added together equal exactly 90°.
• Most crown molding has a top rear angle (the section
that fits flat against the ceiling) of 52° and a bottom rear
angle (the section that fits flat against the wall ) of 38°.
• In order to accurately cut crown molding for a 90°inside
or outside corner, lay the molding with its broad back
surface flat on the saw table.
• When setting the bevel and miter angles for compound
miters, remember that the settings are interdependent
changing one changes the other as well .
Figure 21
10
MAINTENANCE
F
e
n
c
e
Workpiece
Miter Saw Table
miter at 45º, bevel at 0º
F
e
n
c
e
Workpiece
Miter Saw Table
miter at 45º, bevel at 0º