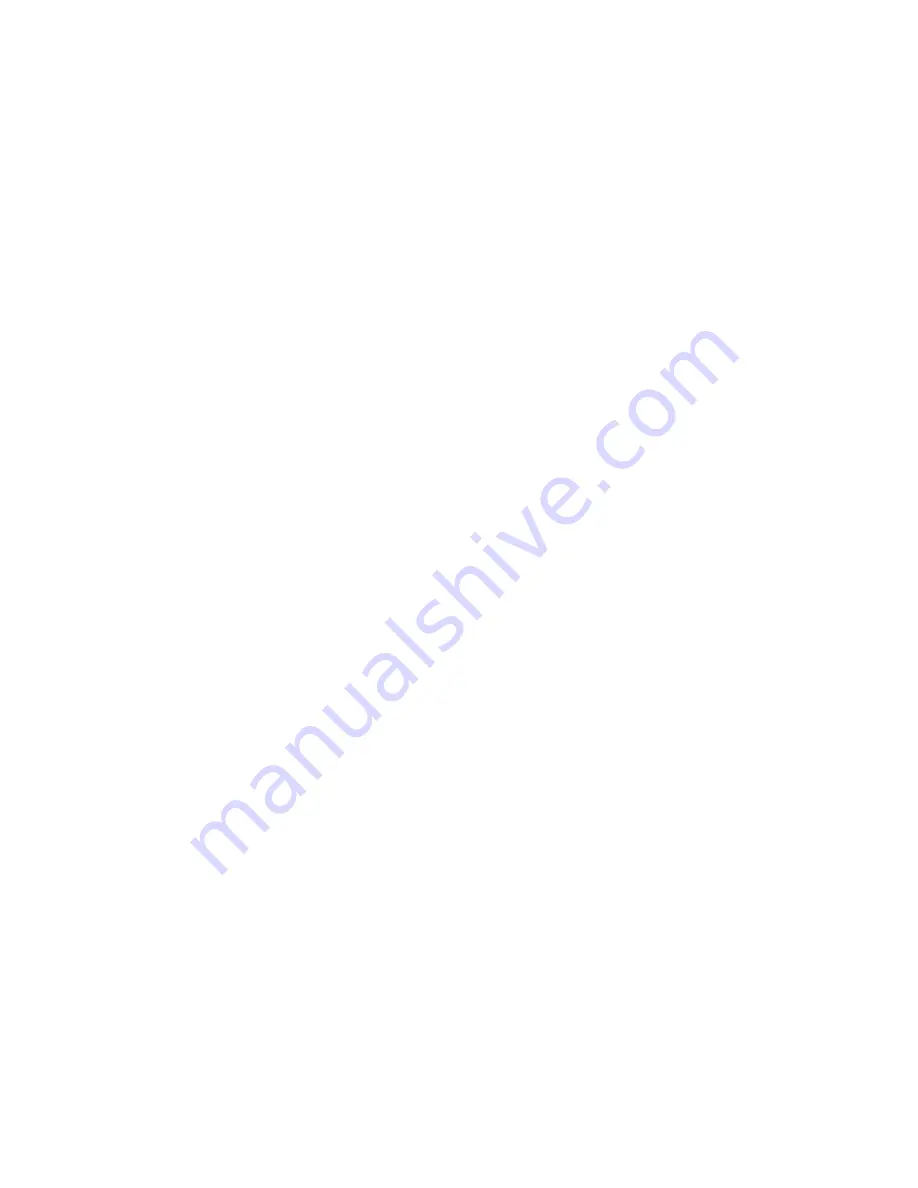
SEAL REPLACEMENT:
There are 7 seals that may require replacement. We
recommend that you have your POWERNAIL Dealer replace
the Seals.
SEAL KIT:
You may choose to buy a Seal Replacement Kit and replace
the seals yourself. It is good practice to replace all seals at one
time regardless if only one seal needs replacement.
SEAL DESCRIPTION & NUMBER:
1. Piston U cup Lip Seal (#19)
2. Return Cylinder U cup Lip Seal (#20)
3. Piston Rod U cup Lip Seal (#21)
4. Rubber Seat (#30)
5. Plunger Seal Set (#32)
6. Plunger Wiper Seal (#33)
7. Return Cylinder 0 Ring Gasket (#34)
To change Seals follow these procedures. Be sure the air
line is disconnected from the Nailer first before making any
repairs. Consult the illustration for the name and location of
the following component parts.
DRIVING BLADE ASSEMBLY REMOVAL:
1. Disconnect the air supply.
2. Remove Rubber Plunger Cap (#18).
3. Unscrew & remove Body Cap (#2).
4. Push Safety Yoke (#26) aside and unscrew the three 10-32
cap screws holding the Plunger (#13) to the Return Cylinder
(#12).
5. Pull the Plunger up and out of the Nailer Body (#1) cavity.
6. Remove the Return Cylinder 0 Ring Gasket (#34) located
on the top of the Return Cylinder under the Plunger.
7. Turn the Nailer over and remove the four cap screws (#48),
that fasten the Adapter Foot and Nail Channel Assembly to the
Nailer Body and lift the Assembly off the Body.
8. Remove the Rubber Bumper (#31).
9. Pull the Driving Blade Assembly out of the Nailer Body by
pulling on the Driving Blade.
10. Hold the Piston Rod (#10) with an 11/16" socket over
its hex end opposite the Piston.
Do not use pliers or a vise
anywhere on the metal parts, they can damage the sealing
surfaces.
11. Use the supplied box wrenches to remove the 5/8"-18 Jam
Nut (#49). Remove the Dowel Pin (#42) and Driving Blade
(#17).
12. Unscrew the Piston from the Piston Rod using the supplied
box wrenches and separate the Piston, Piston Rod and Return
Cylinder.
TO REPLACE THE SEALS:
Plunger Seal Set (#32):
1. Remove the Teflon
® Seal and its O-ring expander from
the Plunger groove using a bent paper clip or pick. Be sure
not to scratch the inside walls of the seal groove with the
wire hook.
2. Clean out the seal groove. Place a new O-ring into the
seal groove by stretching it over the Plunger body. Make
sure the O-ring is not twisted in the groove. Place a new
Teflon
® Seal Ring into the seal groove over the O-ring.
3. Carefully push the Teflon® Seal Ring over the edge of the
Plunger with your thumbs and into the groove. Do this as
quickly as possible to reduce stretching of the Teflon
® Seal
Ring. DO NOT OVER STRETCH THE TEFLON® SEAL
RING. Be sure the Teflon
® Seal Ring is centered all around
the seal groove and not twisted.
4. Wipe off the Seal surface with a clean rag and lubricate
it generously with the supplied lubricant, O-ring grease or
petroleum jelly.
Rubber Seat (#30):
1. Remove the Cylinder Sleeve (#14). The Cylinder Sleeve
would slide out of the Nailer Body when you pull out the
Driving Blade
2. Remove the metal Support Ring (#29) and Rubber Seat
from inside the Nailer body. NOTE THAT THE CHAMFER
ON THE INSIDE OF THE RUBBER SEAT FACES THE
BOTTOM OF THE NAILER. Do not reverse the direction
of the chamfer when you replace the Rubber Seat.
3. Replace the Rubber Seat, Support Ring and Cylinder
Sleeve. Be sure to re install the steel Cylinder Sleeve with
the chamfered inside edge facing the BOTTOM of the
Nailer.
Piston U Cup Lip Seal (#19):
1. Remove the old Piston U Cup Lip Seal from the Piston
using a bent paper clip or pick, being careful not to scratch
the inside walls of the seal groove or the edge of the Piston
with the wire hook.
2. Clean out the seal groove. Place a new U-Cup Lip Seal
into the groove. Make sure the lip seal is not twisted in the
groove and the lips face the top of the Nailer. See the sketch
on next page (#19).
3. Carefully wipe off the U Cup Lip Seal surface with a
clean rag and lubricate it generously with the supplied
lubricant, O-Ring grease or petroleum jelly.
5
Summary of Contents for 50P FLEX
Page 7: ...7 33 21 20 19 30 32 34 ...